Top Challenges Faced by Aluminium Formwork Manufacturers Today
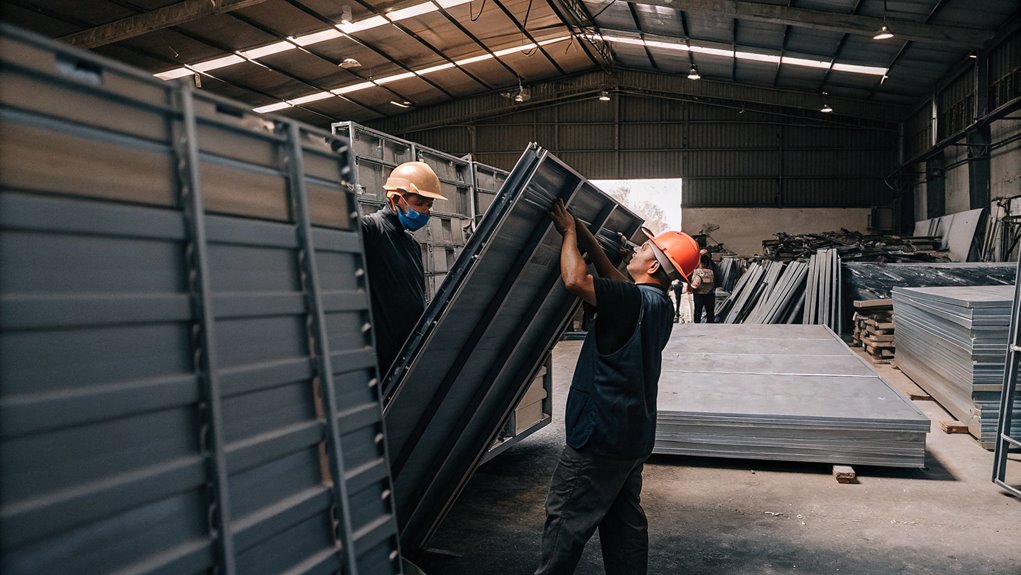
Aluminium formwork manufacturers today face several critical challenges. Rising material costs, especially for aluminium, are hitting our bottom line hard, necessitating strategic supply chain diversification and innovative cost-saving measures. Regulatory compliance issues across different regions add complexity to our operations, making continuous monitoring and strong relationships with regulatory bodies essential. Labor shortages and skill gaps impact production timelines and quality, prompting investments in apprenticeships and automation. The demand for sustainable products pushes us to develop eco-friendly solutions and implement recycling programs. Technological advancements in R&D, such as CNC machines and digital design tools, are vital for staying competitive. As we navigate these pressures on profit margins, embracing innovation is key to our future success. If you're looking to stay ahead, understanding these challenges in depth can provide valuable insights.
Rising Material Costs
Rising material costs are a significant challenge we face as aluminium formwork manufacturers. The increasing prices of raw materials, particularly aluminium, have directly impacted our production costs and profitability. This trend isn't just a temporary fluctuation but a persistent issue that requires strategic planning and innovative solutions.
We are seeing these rising costs ripple through every aspect of our business. From sourcing high-quality aluminium to maintaining the efficiency of our manufacturing processes, each step is now more expensive than it was just a few years ago.
This escalation in costs forces us to reevaluate our pricing strategies and look for ways to maintain competitiveness without compromising on the quality of our products.
One of the key strategies we're implementing is diversifying our supply chain. By exploring alternative suppliers and negotiating better terms, we aim to minimize the impact of price hikes on our operations.
Additionally, we're investing in research and development to find more efficient manufacturing techniques that can help offset the increased material costs.
Another critical approach is enhancing our relationships with clients. Transparent communication about the reasons behind any potential price increases helps build trust and understanding.
We also focus on highlighting the long-term benefits of using aluminium formwork, such as its durability and reuse capabilities, which can justify higher initial costs. For instance, aluminium formwork can be reused up to 150 times, which significantly reduces long-term expenses.
Ultimately, we believe that by being proactive, innovative, and transparent, we can navigate these challenges successfully and continue to deliver top-quality aluminium formwork solutions to our clients.
Regulatory Compliance Issues
As aluminium formwork manufacturers, we face another significant challenge in the form of regulatory compliance issues. These regulations, while essential for ensuring safety and quality, can be complex and ever-evolving, making it difficult to keep up with the latest requirements.
One of the primary issues is the variability in regulations across different regions. What's compliant in one country or state may not be in another, which complicates our manufacturing process and distribution strategies.
This means we've to invest significant resources into understanding and adapting to local regulations, which can be time-consuming and costly.
Moreover, regulatory changes often happen without much notice, leaving us little time to adjust our production lines and processes. This unpredictability can lead to delays and additional expenses as we rush to meet new standards.
For instance, if a new regulation requires changes to the material composition or structural integrity of our formwork, we may need to redesign our products entirely.
To navigate these challenges effectively, we must stay informed about upcoming regulatory changes through continuous monitoring of legislative updates and industry trends. Building strong relationships with regulatory bodies and industry associations can also provide us with valuable insights and support.
Additionally, ensuring our clients receive proper technical support is crucial in helping them comply with changing regulations and maintain the quality and safety of our aluminium formwork systems.
Ultimately, our commitment to regulatory compliance isn't just about avoiding fines or legal issues; it's about ensuring the safety and quality of our products for our customers. By staying proactive and adaptable, we can turn these challenges into opportunities for innovation and excellence in the aluminium formwork industry.
Demand for Sustainable Products
The demand for sustainable products is reshaping the aluminium formwork industry in substantial ways. As consumers and regulatory bodies increasingly prioritize environmental sustainability, we're facing a new era of challenges and opportunities.
At the heart of this shift is the need to produce formwork that not only meets construction standards but also minimizes environmental impact.
We must adapt our manufacturing processes to incorporate more sustainable practices. This includes sourcing raw materials from environmentally responsible suppliers, reducing energy consumption during production, and implementing recycling programs for used formwork.
The use of recycled aluminium, for instance, can noticeably lower the carbon footprint of our products.
Moreover, we need to innovate our product designs to be more durable and reusable. Aluminium formwork is already known for its longevity and reusability compared to traditional timber or steel alternatives. However, we can further enhance these qualities by developing smarter, more versatile designs that reduce waste and extend the lifespan of each piece.
Meeting the demand for sustainable products also involves transparent communication with our customers about our ecological footprint. We must be willing to disclose our production methods, material sourcing, and environmental impact data to build trust and credibility in the market.
Ultimately, embracing sustainability isn't just a compliance issue; it's a strategic imperative that can drive innovation, reduce costs, and open up new market opportunities. By leading the way in sustainable aluminium formwork production, we can contribute to a greener future while maintaining our competitive edge in the industry.
Labor Shortages and Skill Gaps
Labor shortages and skill gaps are among the most pressing challenges we face in the aluminium formwork industry. As manufacturers, we're constantly seeking innovative solutions to overcome these hurdles, but they persist as significant barriers to our growth and efficiency.
The labor shortage is a multifaceted issue. On one hand, the construction industry as a whole is experiencing a dearth of skilled workers due to aging populations and a lack of new entrants. This scarcity affects us directly because we rely on skilled labor to design, manufacture, and install our aluminium formwork systems.
Without an adequate workforce, production timelines are extended, and quality can suffer.
On the other hand, the skill gap exacerbates this problem. The aluminium formwork industry requires specialized skills that aren't easily replaceable. Training programs are essential but take time to yield results. Meanwhile, we struggle with a workforce that may not possess the necessary expertise to handle complex projects efficiently.
To address these challenges, we must be proactive. Investing in apprenticeships and vocational training programs can help bridge the skill gap over time. Additionally, adopting more automated processes where feasible can reduce our reliance on manual labor. Ensuring that our manufacturing engineers have a strong background in manufacturing processes and quality control is also crucial for maintaining production standards and efficiency.
However, these solutions require significant investment and strategic planning.
Ultimately, it's vital for us to collaborate with educational institutions and industry partners to develop robust training programs that equip future generations with the skills needed for this specialized field. By doing so, we can guarantee a sustainable future for our industry despite current labor shortages and skill gaps.
This collaborative approach is key to driving innovation and maintaining our competitive edge in an increasingly demanding market.
Technological Advancements and R&D
We're at the forefront of a technological revolution in the aluminium formwork industry, where innovations in research and development (R&D) are transforming how we design, manufacture, and install our systems. This era of technological advancement presents both opportunities and challenges that we must navigate carefully.
On one hand, advancements in technology have enabled us to create more efficient and durable formwork solutions. For instance:
- Automated Manufacturing: We can now use CNC machines and robotic assembly lines to produce formwork components with higher precision and speed, reducing human error and increasing productivity.
- Advanced Materials: R&D has led to the development of new alloys and coatings that enhance the strength, corrosion resistance, and sustainability of aluminium formwork.
- Digital Design Tools: Utilizing BIM (Building Information Modelling) and other digital design tools allows for more accurate planning, simulation, and optimization of formwork systems before they're even built.
However, these advancements also bring new complexities. The cost of investing in cutting-edge technology can be prohibitive for some manufacturers. Additionally, there's a need for continuous training and upskilling of our workforce to keep pace with evolving technologies.
Despite these challenges, we're committed to embracing innovation. By investing in R&D and adopting new technologies, we aim to deliver better value to our clients through improved quality, reduced costs, and faster project completion times.
This vision aligns with our goal of liberation from traditional constraints, enabling us to build more efficiently and sustainably. As we move forward, we're confident that technological advancements will continue to be a driving force behind our success in the aluminium formwork industry.
Pressure on Profit Margins
In an industry where margins are already slim, the rising costs of raw materials, energy, and advanced technologies are putting significant pressure on our profit margins. As aluminium formwork manufacturers, we face a constant battle to maintain profitability while adhering to the high standards of quality and innovation that our clients demand.
The surge in raw material prices, particularly for aluminium, directly eats into our bottom line. Every dollar increase in the cost of aluminium translates to reduced profit margins unless we can pass these costs on to our customers, which is not always feasible.
Energy costs are another significant factor. With the global push towards sustainability and energy efficiency, modern manufacturing processes require more sophisticated and energy-intensive equipment. While these advancements are necessary for maintaining competitiveness, they add to our operational expenses.
Advanced technologies, though essential for staying ahead in the market, also come with a hefty price tag. Investing in R&D and adopting new technologies is vital but strains our financial resources.
Effective procurement strategies are crucial in managing these costs, as they help in identifying and evaluating potential suppliers and negotiating better terms to ensure cost-effective procurement.
To navigate these challenges, we must be visionary in our approach, assertive in our strategy, and pragmatic in our execution. This includes exploring cost-saving measures without compromising on quality, leveraging technology to enhance efficiency, and fostering stronger relationships with suppliers to negotiate better terms. By being proactive and innovative, we can mitigate the pressure on our profit margins and secure sustainable growth in the industry.
Cost Component | Current Trend | Impact on Profit |
---|---|---|
Raw Materials | Increasing | Reduced Profit |
Energy Costs | Rising | Higher Operational Costs |
| Advanced Technologies | Evolving Rapidly | Increased Investment Required
Market Competition and Innovation
As we navigate the challenges of maintaining profitability, another critical landscape we must address is the intense market competition and the relentless drive for innovation. In the aluminium formwork industry, standing still isn't an option; we must continuously evolve to stay ahead.
The market is saturated with competitors, each vying for a share of the construction sector. To differentiate ourselves, we need to innovate constantly.
Here are some key areas where innovation can make a significant impact:
- Advanced Materials and Technologies: Investing in research and development to create lighter, stronger, and more sustainable aluminium formwork systems can give us a competitive edge. This could include integrating new materials or technologies that enhance durability and ease of use.
- Automation and Digitalization: Embracing automation and digital tools can streamline our production processes, reduce costs, and improve precision. This includes using CAD designs, robotic assembly lines, and data analytics to optimize manufacturing.
- Sustainable Practices: As the world moves towards more sustainable building practices, developing eco-friendly aluminium formwork solutions that are recyclable and energy-efficient can attract environmentally conscious clients and regulatory favor.
Innovation isn't just about staying competitive; it's about leading the market. By embracing cutting-edge technologies and sustainable practices, we can't only meet but exceed industry standards.
This proactive approach will help us remain relevant in a rapidly changing landscape and guarantee our continued success in the aluminium formwork industry.
In essence, market competition and innovation are interlinked challenges that require us to be visionary, assertive, and pragmatic.
Frequently Asked Questions
How Do Manufacturers Ensure Consistent Quality in Aluminium Formwork Production?
We guarantee consistent quality in aluminium formwork production by implementing rigorous quality control protocols at every stage. From raw material selection to the final inspection, we adhere to strict standards.
We invest in advanced manufacturing technology and continuous training for our workforce. Regular audits and customer feedback also help us refine our processes, guaranteeing that every piece of formwork meets our high standards and exceeds customer expectations.
What Are the Most Common Types of Aluminium Used in Formwork?
We use several types of aluminium in formwork, each chosen for its unique properties.
Aluminium 6061 is a favorite due to its high strength-to-weight ratio and excellent corrosion resistance.
Aluminium 6063 is another popular choice, known for its good weldability and finish.
For more demanding projects, we opt for Aluminium 6082, which offers superior mechanical properties and durability.
These alloys guarantee our formwork is robust, reliable, and efficient.
Can Aluminium Formwork Be Reused Multiple Times Without Degradation?
We can confidently say that aluminium formwork is designed to be reused multiple times without significant degradation. Its durability and resistance to wear make it an excellent choice for repetitive use in construction projects.
With proper maintenance and handling, aluminium formwork can withstand numerous cycles of use, saving time and resources while maintaining its structural integrity. This reusability is a key advantage that sets it apart from other materials.
How Does Weather Affect the Durability of Aluminium Formwork?
Weather substantially impacts the durability of aluminium formwork. Exposure to harsh conditions like excessive rain, extreme temperatures, and direct sunlight can accelerate corrosion and wear.
However, high-quality aluminium formwork is designed to withstand these elements. We guarantee our products are treated with durable coatings and alloys that resist corrosion, maintaining their integrity even in challenging weather conditions.
This way, we guarantee long-term performance and reuse without degradation.
Are There Any Specific Safety Protocols for Handling Aluminium Formwork on Site?
When handling aluminium formwork on site, we prioritize strict safety protocols. We guarantee all workers wear personal protective equipment, including hard hats, gloves, and safety glasses.
Proper lifting techniques are mandatory to avoid injuries. Regular inspections of the formwork for any damage or corrosion are also vital.
Clear communication and well-defined workflows help prevent accidents and guarantee a safe working environment. We take no shortcuts; safety is our top priority.
Conclusion
As aluminium formwork manufacturers, we face a myriad of challenges today. Rising material costs and regulatory compliance issues are constant pressures. The demand for sustainable products is growing, while labor shortages and skill gaps hinder our productivity. Technological advancements require continuous R&D investment, further squeezing our profit margins. Amidst fierce market competition, innovation is key to our survival and success. We must adapt, innovate, and prioritize sustainability to thrive in this evolving landscape.