The Physics Behind Aluminium Formwork Stability
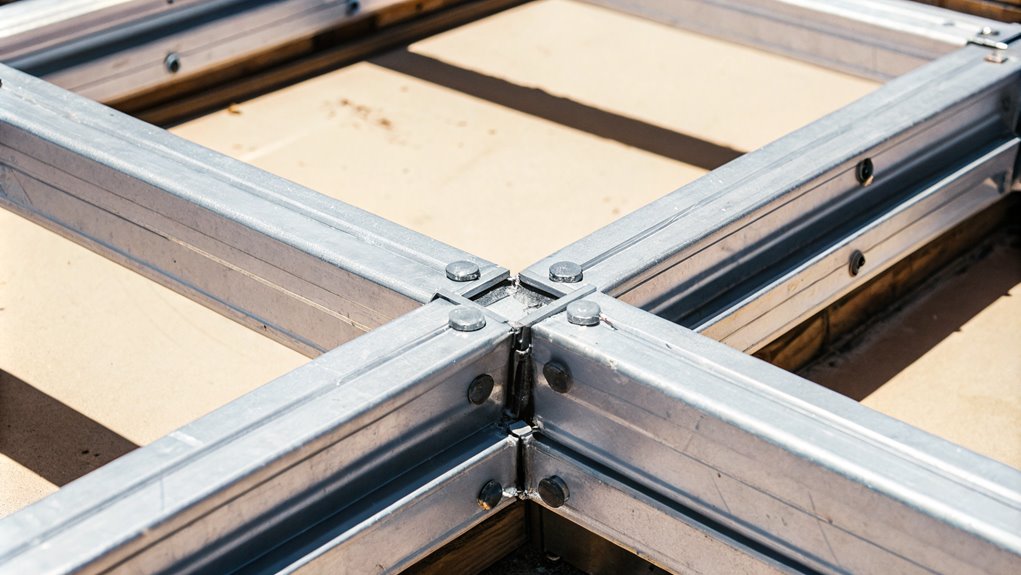
The physics behind aluminium formwork stability hinges on its exceptional material properties and meticulous design. We leverage aluminium's high strength-to-weight ratio, corrosion resistance, and thermal conductivity to guarantee it efficiently conducts heat away from concrete as it sets. Our designs focus on load-bearing capacity, stiffness, and secure connections to prevent failure points. We distribute loads evenly, guarantee beam and column interaction, and maintain foundation stability. Environmental factors like temperature, moisture, wind, and seismic activity are carefully considered. Through advanced stress and strain analysis, including finite element analysis, we optimize the formwork to withstand dynamic loads and material fatigue. By integrating these elements, we create stable and efficient formwork systems that guarantee the integrity of the concrete structure—continuing to explore these principles will reveal even more about how we achieve this stability.
Material Properties of Aluminium
When we discuss the material properties of aluminium, we often find ourselves highlighting its versatility and strength. Aluminium is a lightweight metal with a high strength-to-weight ratio, making it an ideal choice for formwork in construction.
This property allows aluminium formwork to support significant loads without adding excessive weight to the structure, which is vital for maintaining stability and safety on site.
Another key characteristic of aluminium is its corrosion resistance. Unlike steel, aluminium doesn't rust when exposed to air and moisture, reducing the need for protective coatings and extending the lifespan of the formwork.
This resistance also means that aluminium formwork can be reused multiple times without degrading, making it a cost-effective option in the long run.
Aluminium's thermal conductivity is another important factor. It efficiently conducts heat away from concrete as it sets, which helps in achieving uniform curing and preventing thermal cracks.
This guarantees that the concrete develops its full strength and durability, enhancing the overall structural integrity of the building.
The malleability of aluminium is also significant. It can be easily shaped and molded into various forms, allowing for precise and complex designs that would be difficult or costly to achieve with other materials.
This flexibility in design enables architects and engineers to push the boundaries of innovation in building construction.
Structural Design Considerations
With aluminium's material properties firmly established, we turn our attention to the structural design considerations that maximize its benefits in formwork. When designing aluminium formwork, it's vital to consider the load-bearing capacity and stiffness of the material. Aluminium's high strength-to-weight ratio makes it an ideal choice for formwork, but it must be carefully engineered to withstand the pressures and stresses imposed during concrete pouring and curing.
We must guarantee that the formwork system is rigid enough to maintain its shape and resist deformation under load. This often involves using a combination of aluminium panels, beams, and support systems that are precisely calculated to distribute loads evenly.
The structural integrity of the formwork is also dependent on the connections between components; robust and secure joints are essential to prevent any failure points.
Another key consideration is the formwork's ability to resist lateral loads and wind forces, particularly in tall structures or those exposed to harsh weather conditions. Here, we often employ bracing systems and tie rods to enhance stability and prevent any unwanted movement.
Additionally, we need to evaluate the ease of assembly and disassembly of the formwork system. Modular designs that allow for quick setup and teardown can substantially reduce construction time and costs.
Load Distribution and Transfer
Load distribution and transfer are critical components in ensuring the stability of aluminium formwork systems. When we design and implement these systems, it's essential to understand how loads are distributed across the structure and how they're transferred to the foundation or supporting elements.
Key Factors in Load Distribution and Transfer
- Uniform Load Distribution: Aluminium formwork should be designed to distribute loads evenly across the entire system. This can be achieved through a well-thought-out grid pattern that guarantees no single point bears an excessive amount of weight.
- Beam and Column Interaction: The interaction between beams and columns is vital. Beams should be adequately supported by columns, and columns should be strong enough to bear the transferred loads without buckling or failing.
- Connection Points: The strength of connection points between aluminium components is paramount. Properly secured connections guarantee that loads are transferred efficiently without compromising the integrity of the formwork.
- Foundation Stability: The stability of the foundation upon which the formwork rests is essential. A solid foundation guarantees that transferred loads don't cause instability or settlement issues.
By focusing on these aspects, we can guarantee that our aluminium formwork systems are robust and capable of withstanding various types of loads, from concrete pressure to environmental forces like wind and seismic activity. Effective load distribution and transfer mechanisms also benefit from the use of reusable formwork, which can be employed up to 150 times, enhancing the overall efficiency and success of construction projects.
Effective load distribution and transfer mechanisms not only enhance safety but also contribute to the overall efficiency and success of construction projects.
In essence, understanding load distribution and transfer empowers us to create resilient and reliable aluminium formwork systems that stand the test of time and external pressures.
This vision of stability liberates us from the constraints of traditional construction methods, allowing for more innovative and sustainable building practices.
Concrete-Formwork Interaction
Having guaranteed the stability of our aluminium formwork through effective load distribution and transfer, we now turn our attention to the critical interface between the formwork and the concrete it supports. This interaction is pivotal because it directly influences the quality of the finished concrete surface and the overall integrity of the structure.
When concrete is poured into aluminium formwork, several key factors come into play. First, the surface finish of the formwork itself plays a vital role. A smooth, non-porous surface guarantees that the concrete doesn't adhere excessively to the formwork, making it easier to strip once the concrete has set.
This not only saves time but also reduces the risk of damaging either the formwork or the concrete.
The chemistry between concrete and aluminium is another important consideration. Aluminium formwork can react with certain chemicals in the concrete, potentially leading to defects or discoloration. To mitigate this, we use coatings or treatments on the formwork that prevent such reactions, guaranteeing a clean and consistent finish.
Additionally, the temperature and moisture conditions at the interface are critical. Properly controlled temperatures and moisture levels help in achieving uniform curing and reducing shrinkage cracks in the concrete.
This careful management guarantees that the concrete sets evenly and maintains its structural integrity.
Environmental Factors Impact
How do environmental factors influence the stability and performance of aluminium formwork? This is a vital question for anyone involved in construction, as the environment can substantially impact the integrity and effectiveness of your formwork.
When we examine environmental factors, we're not just talking about weather conditions; we're also looking at the broader context in which the formwork is used.
Here are some key environmental factors to ponder:
- Temperature Variations: Extreme temperatures can affect the expansion and contraction of aluminium, potentially altering its shape and stability. High temperatures can also accelerate chemical reactions that might degrade the material over time.
- Humidity: Moisture in the air can lead to corrosion, especially if the aluminium isn't properly protected. This is particularly relevant in coastal or humid climates where rust and corrosion are more common.
- Wind and Seismic Activity: Strong winds or seismic activity can exert considerable forces on the formwork, testing its structural integrity. In areas prone to earthquakes or high winds, additional bracing and anchoring may be necessary.
- Chemical Exposure: Chemical substances present at construction sites, such as those found in certain types of concrete or cleaning agents, can react with aluminium and weaken it.
Understanding these environmental factors allows us to take proactive steps to guarantee our aluminium formwork remains stable and performs as intended.
By selecting appropriate coatings, using protective measures against corrosion, and designing with local conditions in mind, we can enhance the durability and reliability of our formwork systems.
This not only guarantees project success but also contributes to a safer working environment for everyone involved.
Stress and Strain Analysis
When it comes to guaranteeing the stability and performance of aluminium formwork, conducting a thorough stress and strain analysis is crucial. This analysis isn't just a theoretical exercise but a critical step in guaranteeing that the formwork can withstand the various loads it will encounter during construction.
We must consider both the static and dynamic forces that will act on the formwork, including the weight of concrete, personnel, and equipment, as well as any environmental factors like wind or seismic activity.
We start by identifying the key stress points in the aluminium structure. These are typically areas where loads are concentrated, such as at connections between different sections of formwork or where supports are anchored.
Using finite element analysis (FEA) or other numerical methods, we can model these stresses accurately and predict how the material will behave under different loading conditions.
Next, we analyze the strain on the material. Aluminium has a relatively high strength-to-weight ratio, but it's still susceptible to deformation under load. By calculating the strain at various points, we can determine whether the formwork will maintain its shape and integrity throughout the construction process.
Our goal is to guarantee that the aluminium formwork remains stable and doesn't fail under load. This involves not only designing the formwork to withstand maximum anticipated loads but also considering factors like material fatigue and potential corrosive environments that could affect its performance over time.
Additionally, ensuring compliance with building codes is essential to validate the structural integrity and safety of the formwork.
In essence, a meticulous stress and strain analysis allows us to design and construct aluminium formwork that isn't just safe but also efficient and durable. By leveraging advanced analytical tools and a deep understanding of material behavior, we can push the boundaries of what's possible with aluminium formwork, enabling more complex and ambitious construction projects than ever before.
Stability Under Dynamic Loads
As we guarantee the stability of aluminium formwork under static loads, we must also consider the impact of dynamic forces. Dynamic loads, such as those from wind, seismic activity, or even the movement of workers and equipment, can substantially affect the structural integrity of our formwork systems.
Understanding and mitigating these dynamic forces is essential for ensuring that our aluminium formwork remains stable and secure.
Here are some key considerations:
- Wind Loads: Wind can exert considerable pressure on the formwork, especially in tall structures or open sites. We need to calculate wind loads accurately and design our formwork to withstand these forces without compromising its stability.
- Seismic Activity: In seismically active areas, formwork must be designed to resist earthquake forces. This involves ensuring that the formwork is securely anchored and can absorb or distribute seismic energy effectively.
- Dynamic Movement: The movement of workers, cranes, and other equipment can introduce dynamic loads that must be accounted for. Proper planning and execution are essential to minimize these impacts.
- Resonance: Dynamic loads can sometimes cause resonance in the structure, leading to amplified vibrations and potential failures. We must analyze the natural frequencies of our formwork to avoid resonance issues.
Optimizing Formwork System Design
Optimizing the design of our aluminium formwork systems is crucial for guaranteeing both stability and efficiency. When we set out to enhance these systems, we focus on several key aspects that collectively contribute to their overall performance.
First, we prioritize the material selection and fabrication process. Aluminium is chosen for its lightweight yet robust properties, but we also guarantee that the alloy used is of high quality and resistant to corrosion. This not only extends the lifespan of the formwork but also maintains its structural integrity over time.
Next, we explore the geometric design of the formwork components. A well-engineered system should have a balanced distribution of weight and load-bearing capabilities. We use advanced computational tools to simulate various loading scenarios and optimize the shape and size of each component to maximize stability.
Another critical factor is the connection system between different parts of the formwork. Secure and reliable connections are essential for preventing any structural failure under load. We design these connections with precision, guaranteeing they're easy to assemble and disassemble while maintaining their strength.
Finally, we integrate safety features into our designs. This includes safety rails, access points, and other protective measures to guarantee that workers can operate safely during construction.
By combining these elements—material quality, geometric optimization, secure connections, and safety features—we create aluminium formwork systems that aren't only stable but also efficient and safe to use.
Our approach is driven by a commitment to innovation and a vision for constructing better, faster, and safer. By continuously optimizing our formwork system designs, we empower builders to achieve their goals with confidence and precision.
Frequently Asked Questions
How Often Should Aluminium Formwork Be Inspected for Damage?
We need to inspect aluminium formwork regularly to guarantee safety and efficiency. Daily checks are vital, especially after each use or when conditions change.
Weekly inspections should focus on wear and tear, while monthly checks should be more thorough, examining for any structural damage or corrosion. This proactive approach prevents accidents and extends the lifespan of the formwork.
Can Aluminium Formwork Be Used in Extreme Weather Conditions?
We can confidently use aluminium formwork in extreme weather conditions, but with caution. Its durability and resistance to corrosion make it a viable option.
However, we must guarantee proper anchoring and bracing to withstand high winds and heavy loads. Regular inspections are vital to identify any potential weaknesses or damage.
What Are the Safety Protocols for Handling Aluminium Formwork?
When handling aluminium formwork, we guarantee safety by wearing protective gear like gloves and hard hats.
We inspect the formwork for any damage or corrosion before use. Proper lifting techniques are vital to avoid injuries, and we always secure the formwork firmly to prevent it from shifting during construction.
Regular maintenance and storage in dry areas are also key to maintaining its integrity and longevity.
How Does the Reuse of Aluminium Formwork Affect Its Stability?
When we reuse aluminium formwork, its stability can be affected in several ways. Each reuse cycle can introduce minor damage, such as scratches or bends, which weaken the structure.
Additionally, repeated assembly and disassembly can loosen joints and reduce the overall rigidity of the formwork.
Regular inspections and proper maintenance are vital to guarantee that the aluminium formwork retains its stability and safety over multiple uses. We must be vigilant to maintain its integrity.
Are There Specific Storage Guidelines for Aluminium Formwork?
When it comes to storing aluminium formwork, we must be meticulous. We guarantee that the formwork is cleaned and dried thoroughly to prevent corrosion.
We store it in a dry, protected area, away from direct sunlight and moisture. We also avoid stacking formwork pieces tightly, as this can cause damage.
Conclusion
In summary, grasping the physics behind aluminium formwork stability is vital for constructing robust and efficient structures. By leveraging aluminium's material properties, optimizing structural design, managing load distribution, and considering concrete-formwork interaction, environmental factors, and dynamic loads, we can guarantee the stability and longevity of our constructions. Through meticulous stress and strain analysis, we can push the boundaries of what is possible in building design. This approach not only enhances safety but also drives innovation in the construction industry.