The Future of Aluminium Formwork in Modular Construction
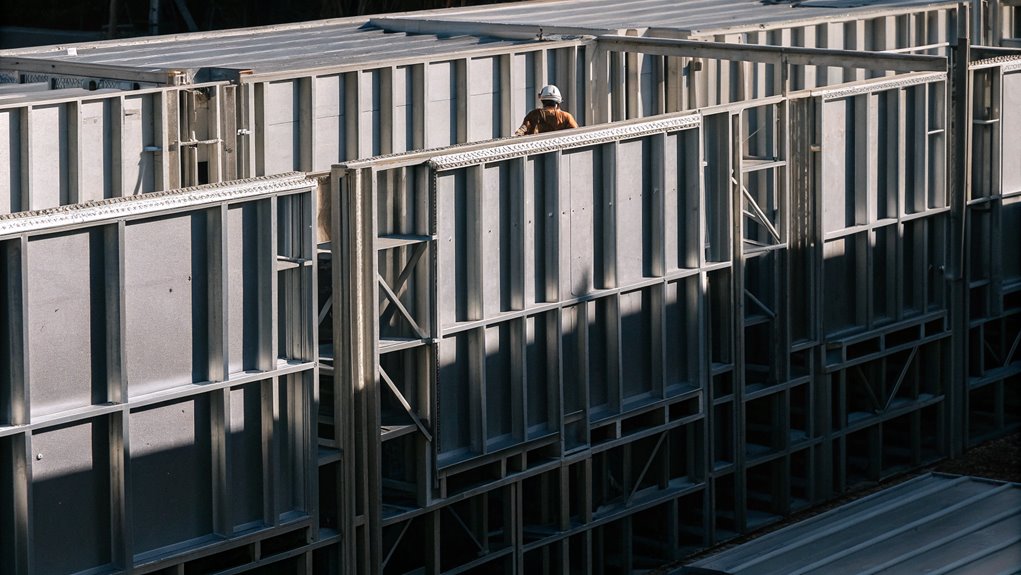
The future of aluminium formwork in modular construction looks incredibly promising. We're seeing significant advancements in its lightweight and durable properties, which make it easier to transport, handle, and install, reducing the risk of injury and speeding up the construction process. Aluminium formwork allows for faster assembly and disassembly, enabling project timelines to be shortened dramatically, with each floor potentially completed in as little as 4-7 days. Its precision engineering guarantees high-quality finishes, minimizing the need for additional surface treatments. With the ability to be reused up to 250 times, it offers substantial cost savings and environmental benefits. As we continue to integrate technologies like BIM and IoT, aluminium formwork is set to revolutionize the way we build, making construction more efficient, sustainable, and safe. If you're interested in how this technology can transform your next project, there's even more to explore.
Lightweight and Durable Properties
When it comes to the lightweight and durable properties of aluminium formwork, it's clear why this material has become a staple in modular construction. One of the most substantial advantages of aluminium formwork is its lightweight design. Unlike traditional steel formwork, aluminium is markedly lighter, making it easier to transport, handle, and install on-site.
This reduces the risk of injury during handling and speeds up the construction process, saving both time and labor costs.
The durability of aluminium formwork is equally impressive. It's designed to withstand numerous cycles of concrete pouring and stripping without considerable wear and tear. This reusability is a game-changer, as it makes aluminium formwork a cost-effective solution in the long run.
We can reuse these systems multiple times, reducing the overall cost of materials and labor on large projects.
Aluminium formwork also stands strong against various weather conditions, whether it's scorching heat, intense cold, or pouring rain. This resilience guarantees the continuity of the construction process, even in challenging environmental conditions.
Additionally, the strength and rigidity of aluminium allow it to maintain the desired shape while the concrete solidifies, guaranteeing a high-quality finish with fewer defects and imperfections.
In our experience, the combination of lightweight and durable properties makes aluminium formwork an indispensable tool in modular construction. It not only enhances efficiency and safety but also contributes to a more sustainable construction practice by reducing waste and the demand for new materials.
As we continue to innovate and adopt more sustainable construction methods, aluminium formwork remains at the forefront, offering a reliable and efficient solution for building high-quality structures.
Efficiency in Construction Processes
In the domain of modular construction, the efficiency of aluminium formwork is a key factor that sets it apart from traditional methods. When we talk about efficiency, we're not just discussing speed; we're also looking at precision, cost-effectiveness, and the overall streamline of the construction process.
Aluminium formwork systems are designed to accelerate every phase of construction. Here are some key ways they enhance efficiency:
- Faster Assembly and Dismantling: The modular nature of aluminium formwork allows for quick assembly and dismantling, markedly reducing the time spent on these tasks. This rapid turnover enables construction teams to complete repetitive tasks, like slab casting, in shorter cycles.
- Reduced Construction Time: By enabling faster formwork cycles, aluminium formwork systems dramatically shorten project timelines. For instance, each floor can be completed in as short as 4-7 days, which is vital for large-scale housing developments or high-rise buildings.
- Enhanced Precision: Aluminium formwork systems are manufactured with millimeter-level accuracy, ensuring perfectly aligned and smooth concrete surfaces. This precision reduces the need for post-casting corrections, saving time and labor.
- Lightweight and Easy to Handle: Aluminium is much lighter than traditional steel formwork, making it easier to transport, assemble, and reposition on-site. This not only speeds up construction but also reduces the dependency on heavy machinery.
- Cost Efficiency: While the initial investment in aluminium formwork may be higher, the long-term savings are substantial. Faster project completion reduces labor costs, and the reusability of panels minimizes material expenses. Additionally, aluminium formwork can be reused up to 150 times, further enhancing its cost-effectiveness and reducing overall construction costs.
Precision and Quality Finishes
Precision and Quality Finishes are where aluminium formwork truly shines, building on the efficiency gains we've discussed. When it comes to achieving high-quality concrete finishes, aluminium formwork systems stand out due to their precision and consistency.
One of the key advantages of aluminium formwork is its ability to produce seamless, precisely sized concrete structures. Unlike traditional formwork, which often requires additional surface treatments like plastering, aluminium formwork delivers flawless finishes right from the start. This is largely due to the millimeter-level accuracy in the manufacturing of these systems, ensuring perfectly aligned and smooth concrete surfaces.
Here is a comparison of the quality and precision aspects of different formwork types:
Formwork Type | Surface Finish | Precision | Need for Post-Casting Corrections |
---|---|---|---|
Aluminium Formwork | Flawless, smooth | High | Minimal to none |
Traditional Timber | Rough, uneven | Low | High |
Steel Formwork | Fair, some unevenness | Medium | Moderate |
This precision not only enhances the aesthetic quality of the building but also improves its structural integrity. With aluminium formwork, you can expect monolithic constructions where walls and slabs are cast simultaneously, reducing the need for additional structural elements and ensuring a more durable final product.
The high quality of the finishes also means less maintenance and repair work down the line. This is particularly important for family homes and residential buildings, where durability and low maintenance are vital for long-term comfort and peace of mind. By opting for aluminium formwork, you are not just building a structure; you are creating a lasting, high-quality space that will serve your needs for years to come.
Reusability and Cost Savings
Aluminium formwork's reusability is a substantial factor in its cost-saving potential, making it an attractive option for construction projects. When we choose aluminium formwork, we aren't just selecting a material; we're investing in a system that can be used multiple times, markedly reducing our overall costs.
Here are some key points that highlight the reusability and cost savings of aluminium formwork:
- High Reusability: Aluminium formwork can be reused up to 200 times, and in some cases, even up to 250 times, without compromising its structural integrity.
- Reduced Material Costs: By reusing the same formwork multiple times, we minimize the need for new materials, which translates into substantial cost savings over the long term.
- Lower Labor Expenses: The ease of assembly and disassembly of aluminium formwork reduces labor costs by up to 30%, as it eliminates the need for complex and time-consuming setup processes.
- Minimal Wastage: Aluminium formwork's durability and recyclability mean that very little waste is generated. Even when the formwork reaches the end of its useful life, it can be recycled and recast into new formwork components.
- Long-Term Cost Savings: While the initial investment in aluminium formwork may be higher than traditional methods, its long-term reusability and minimal maintenance needs result in considerable cost savings, especially in large-scale or repetitive projects.
Incorporating aluminium formwork into our construction projects not only enhances our environmental footprint but also provides a robust financial advantage. It allows us to deliver high-quality buildings efficiently, while also contributing to a more sustainable and cost-effective construction process.
While the initial investment in aluminium formwork may seem higher than traditional methods, its long-term benefits are significant. The reusability of aluminium formwork and its minimal maintenance needs result in considerable cost savings over time.
Environmental and Safety Benefits
When we opt for aluminium formwork, we're not just choosing a material; we're embracing a system that substantially reduces our environmental footprint and enhances safety on construction sites.
From an environmental perspective, aluminium formwork is a game-changer. Its high reusability means it can be used up to 200 or even 300 times without losing its integrity. This markedly reduces the amount of construction waste generated, particularly when compared to traditional timber formwork which often ends up as disposable waste.
Aluminium is also 100% recyclable, allowing it to be reused again at the end of its life cycle, contributing to a more sustainable construction process.
In terms of safety, aluminium formwork offers several critical advantages. Its lightweight yet durable nature reduces manual handling risks, minimizing the likelihood of musculoskeletal injuries and accidents caused by dropped materials.
The high strength-to-weight ratio of aluminium guarantees that the formwork can bear the loads of fresh concrete without deformation or failure, preventing collapses or structural failures during concrete pouring.
Additionally, aluminium formwork is non-combustible, enhancing fire safety on construction sites and protecting workers and property. The ergonomic design of these panels, with features like easy-to-grip edges and pre-drilled holes, makes handling safer and more efficient.
This design reduces the risk of hand injuries and other mishaps. By generating less waste and maintaining a clean site, aluminium formwork also reduces tripping hazards and the risk of accidents caused by construction debris.
Versatility in Construction Applications
In virtually every construction project, the versatility of aluminium formwork stands out as a significant advantage. This technology has revolutionized the way we build, allowing us to tackle a wide range of projects with ease and efficiency.
When we talk about versatility, we're not just referring to the ability to use aluminium formwork in different types of buildings; we're talking about its adaptability to various architectural designs and construction needs.
Here are some key ways aluminium formwork demonstrates its versatility:
- Residential High-Rise Buildings: Aluminium formwork excels in the construction of residential high-rise buildings due to its ability to provide precise and consistent shapes for walls, floors, and staircases. This guarantees uniformity and high-quality finishes, which are essential in repetitive floor layouts.
- Commercial Complexes: From shopping malls to office buildings and hotels, aluminium formwork can handle complex designs with ease. It reduces the need for additional finishing work and allows for the creation of intricate architectural features.
- Mass Housing Projects: In areas where mass housing is essential, aluminium formwork accelerates the construction process while maintaining high quality and reducing costs. Its ease of assembly and disassembly makes it ideal for large-scale housing initiatives.
- Sustainable and Eco-Friendly Buildings: Aluminium formwork is a boon for sustainable construction. Being recyclable, it reduces waste and minimizes environmental impact. This makes it a perfect choice for green buildings and eco-friendly developments.
- Custom Architectural Designs: Aluminium formwork can be molded into various shapes and sizes, making it perfect for crafting structures with unconventional designs. This versatility allows builders to bring complex architectural visions to life without compromising on quality or efficiency.
The ability of aluminium formwork to fit seamlessly into different construction scenarios is what makes it such a valuable tool in the industry.
Whether we're building high-rise apartments, shopping malls, or sustainable homes, aluminium formwork offers the flexibility and precision needed to deliver superior results.
Future Trends and Industry Impact**
As we look to the future, how will aluminium formwork continue to shape the construction industry? The answer lies in several key trends and innovations that are already transforming the way we build.
First, technological integration will play a vital role. The adoption of Building Information Modeling (BIM) software, IoT devices, and automated systems will continue to enhance formwork planning, visualization, and optimization. These technologies enable real-time monitoring, data analytics, and predictive maintenance, making construction projects more efficient and sustainable.
Another major trend is the advancement in modular and customizable formwork systems. These systems, with their precision-engineered connections and standardized parts, allow for faster assembly and disassembly. This modularity is particularly beneficial in high-rise construction and urban environments where time and space are limited.
It enables consistent quality, boosts productivity, and reduces labor costs and waste.
Sustainability is also at the forefront of future trends in aluminium formwork. The reusability of aluminium components greatly reduces the need for traditional timber formwork, protecting natural resources and minimizing environmental impact.
Additionally, the accuracy and efficiency of aluminium formwork cut down on construction time and energy use, substantially decreasing the carbon footprint of projects.
As cities expand vertically to accommodate growing populations, the demand for efficient and sustainable construction solutions will increase. Aluminium formwork, with its lightweight nature, structural integrity, and adaptability, is poised to meet this demand.
It will continue to be a driving force in the construction industry, enabling the creation of high-quality, aesthetically pleasing, and environmentally responsible buildings.
Frequently Asked Questions
How Do Labour Shortages Impact the Use of Aluminium Formwork?
Labour shortages substantially impact our use of aluminium formwork. We face a global crisis of skilled labourers, which slows down our construction projects.
Without the right expertise, we struggle to assemble, dismantle, and maintain these systems efficiently. This shortage increases wear and tear, reduces the number of possible repetitions, and hikes labour costs due to the need for specialized training and increased manpower to compensate for the skill gaps.
What Are the Common Design Flaws in Aluminium Formwork Systems?
When designing aluminium formwork systems, we often encounter several common flaws. One major issue is inadequate load calculations, which can lead to catastrophic failures due to unrealistic estimates of weight and stress.
Another problem is poor material selection, where the wrong alloy or finish compromises the system's integrity.
Additionally, incompatible component sourcing can create significant logistical issues, and design flaws such as misalignment or insufficient bracing can cause warping or buckling of the formwork.
How Does Thermal Conductivity Affect Concrete Curing in Aluminium Formwork?
When we use aluminum formwork, thermal conductivity can affect concrete curing in several ways. Aluminum's high thermal conductivity can lead to rapid heat transfer, which might accelerate or unevenly distribute the heat from the setting concrete.
This can result in inconsistent curing rates, potentially causing cracks or weaknesses in the concrete structure. To mitigate this, we need to guarantee proper insulation and control the curing environment carefully.
What Are the Requirements for Accurate Mold Matching in Aluminium Formwork?
For accurate mold matching in aluminium formwork, we need to guarantee several key points. First, the design must be precise to avoid on-site installation and modification of the mold design. This extends the assembly and repair time.
The aluminum formwork should be produced without any wrong or missing plates, reducing the need for repairs and finishing. Additionally, the openings and punching must be accurate, with no deviations or missing punches.
Clear packaging with detailed numbers reflecting column, beam, and plate numbers is also vital for efficient material handling.
How Should Aluminium Formwork Be Packaged and Transported to the Construction Site?
When we package and transport aluminium formwork, accuracy is key. We guarantee each package has clear numbers and reflects the requirements of column, beam, and plate numbers according to the drawing numbers.
This facilitates easy material lifting and prevents confusion on site. A detailed packing list must be provided, recording all formwork packaging details to avoid any mistakes during delivery and installation.
Conclusion
As we look to the future, aluminum formwork is poised to revolutionize modular construction even further. Its lightweight and durable properties will continue to streamline our building processes. With efficiency in construction cycles, precision in finishes, and significant cost savings through reusability, we're not only building faster and better, but also greener and safer. Its versatility and environmental benefits make it an indispensable tool, shaping a more sustainable and efficient construction industry for generations to come.