Streamlining Workflow: The Role of On-Site Aluminium Formwork Training
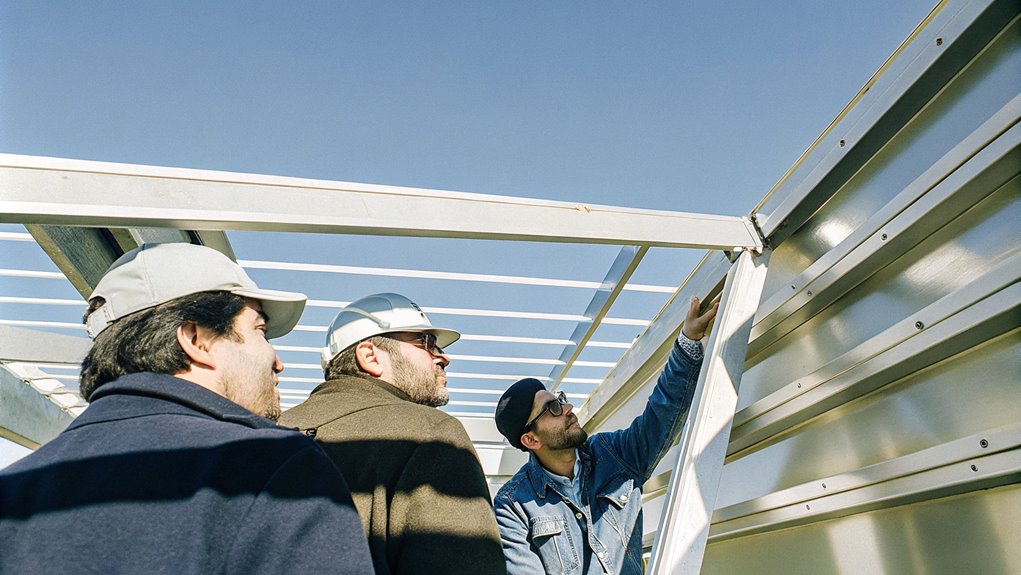
On-site training for aluminium formwork installation is pivotal for streamlining our construction workflow. By providing hands-on experience in the actual work environment, we bridge the gap between theory and practice, addressing the significant skills gaps in the industry. This approach allows us to immediately apply what we've learned, enhancing safety, productivity, and project efficiency. We guarantee workers are equipped with the latest techniques and best practices, and regular updates on safety protocols and maintenance procedures are essential. Proper training also fosters a sense of camaraderie and shared knowledge among team members, leading to faster project completion and higher quality finishes. As we continue to focus on these methods, we'll see even more improvements in our overall project timeline efficiency.
Importance of On-Site Training
The success of any construction project hinges on the expertise of its workforce, and when it comes to aluminium formwork, on-site training is paramount. As we explore the world of rapid and efficient construction, it's clear that the skills of our team members are the backbone of our operations. On-site training for aluminium formwork isn't just a necessity; it's a game-changer.
When we invest in on-site training, we guarantee that our workers are equipped with the latest techniques and best practices. This hands-on approach allows them to grasp the modular design and ease of assembly of aluminium formwork systems quickly.
By training directly on the construction site, our team can immediately apply what they've learned, streamlining the entire process. This not only speeds up construction cycles but also enhances the quality of the final product.
Safety is another critical aspect where on-site training excels. Aluminium formwork systems are designed with safety in mind, featuring lightweight panels, built-in safety rails, and non-slip surfaces. However, it's the thorough training that guarantees our workers can navigate these systems safely and efficiently.
Regular updates on safety protocols and the latest assembly and disassembly methods keep our workforce ahead of potential risks, creating a safer working environment for everyone.
Moreover, on-site training fosters a sense of camaraderie and shared knowledge among team members. As workers learn together, they develop a deeper understanding of each other's roles and responsibilities, leading to smoother collaboration and reduced errors.
This collective expertise translates into faster project completion, higher quality finishes, and significant cost savings. Additionally, with the expertise in aluminium formwork redesign, we can maximize the reusability of existing formwork, further enhancing efficiency and cost-effectiveness.
In essence, on-site aluminium formwork training is our key to accessing efficient, safe, and high-quality construction practices. By prioritizing this training, we empower our workforce to excel, guaranteeing our projects are completed swiftly, safely, and to the highest standards.
Safety Protocols and Guidelines
When it comes to working with aluminium formwork, safety protocols and guidelines are at the heart of our operations. Ensuring the well-being of our workers and the integrity of the structure we're building is paramount, and this starts with meticulous attention to safety.
First and foremost, proper installation and inspection are vital. We make sure each component of the aluminium formwork is meticulously connected and secured to guarantee structural stability.
Regular inspections by qualified personnel help detect any potential defects or signs of wear and tear, allowing us to address issues before they become serious problems.
Fall protection is another critical aspect; we provide safety harnesses, guardrails, and stable work platforms to prevent falls.
Electrical safety is also a top concern; we guarantee all electrical equipment is regularly inspected and grounded to prevent electrical accidents. Electrical wires are properly insulated and kept away from water sources to minimize risks.
Lifting and handling aluminium formwork panels require careful planning and execution. We use cranes or hoists for heavy lifting and train our workers in safe lifting procedures.
The use of slings or other lifting devices is essential to prevent accidents. We also guarantee that the load capacity of the formwork isn't exceeded and that the ground conditions can support the weight.
Moreover, we shield the aluminium formwork from extreme weather conditions like high winds or heavy rain, which can compromise stability or cause debris to fall.
Worker training is indispensable; our team is familiar with the correct installation, handling, and safety protocols associated with the formwork system, ensuring compliance with building codes.
Regular safety briefings and job-site inspections help maintain a culture of safety.
Assembly and Disassembly Techniques
To guarantee the efficient and safe assembly and disassembly of aluminium formwork, we follow a meticulous step-by-step process.
Assembly Techniques
When we begin assembling the aluminium formwork, we start by setting out the layout and marking the positions where the formwork panels will be placed. This involves verifying that the slab panels are assembled from the corner inwards, filling out the entire slab area by pinning the panels together securely.
Next, we install the reinforcement (rebar), mechanical and electrical (M&E) components, and plumbing before proceeding to assemble the wall, beam, and slab formworks.
It's vital to level and plumb the formwork to confirm it's perfectly aligned and supported with modifiable steel props. We also make sure to attach external working brackets to facilitate safe access and working conditions.
Before concreting, we conduct a thorough pre-check to confirm all components are correctly positioned and the formwork is stable. During the concreting process, we monitor closely to prevent any discrepancies or potential failures.
Disassembly Techniques
For the disassembly process, we follow a specific sequence to avoid damaging the concrete or the formwork. We start by dismantling the components that bear no load, such as the shuttering forming the vertical faces of walls, beams, and column sides.
This is followed by the removal of the shuttering forming the soffit of slabs, and finally, the heavily loaded shuttering like those forming the soffit of beams and girders.
We dismantle the hanging formwork and iron boxes promptly to avoid the difficulty of removing them once the concrete is fully solidified. The reinforcement system is removed in a specific order, starting with the panel struts and waling.
Finally, we dismantle the iron accessories, wall panels, beam panels, and slab panels systematically to confirm a smooth and safe process. By following these steps, we can confirm that the aluminium formwork is assembled and disassembled efficiently and safely.
Maintenance and Inspection Best Practices
Maintaining our aluminium formwork is essential for its longevity and performance. To guarantee our equipment remains in top condition, we must adhere to strict maintenance and inspection best practices.
First and foremost, cleaning is a fundamental step. We need to clean the formwork thoroughly between uses, removing all residue, including concrete remnants and any other foreign materials. This prevents degradation and makes the formwork easier to use and maintain.
Regularly oiling the formwork before and after each use is also vital; it forms a protective barrier that prevents concrete from sticking and shields the formwork from rust and corrosion.
Inspections are another critical aspect of maintenance. We conduct regular functional and safety checks on the full formwork inventory, including accessories, to guarantee everything meets strict quality standards.
This includes checking for scratches, holes, or any damaged sections that need repair. The plastic facing on our formwork can be repaired using the same material, without the need for chemical additives or glues, by heating and welding the polypropylene to create a stable thermal bond.
Professional repair services are also essential. Skilled technicians use advanced welding techniques to repair and refurbish the formwork, guaranteeing it aligns with industry standards.
Additionally, regeneration services can rejuvenate our formwork, involving an extensive range of repairs such as re-coating panel frames, cleaning, repairing, and upgrading used facings.
Optimizing Construction Workflow
Optimizing our construction workflow with aluminium formwork involves several key strategies that can substantially enhance efficiency and productivity. Here are some of the most effective approaches we can implement:
Streamlined Formwork Assembly and Disassembly
One of the primary advantages of aluminium formwork is its modular nature, which allows for quick assembly and disassembly. This feature enables us to complete construction phases faster, particularly in high-rise projects where we can achieve a four to five-day cycle per floor.
Efficient Scheduling and Planning
Proper planning is essential for optimizing our workflow. We need to determine the specific dimensions, loads, and finishes required for the project and select aluminium formwork systems that meet these specifications. Early integration of formwork planning into the design phase guarantees compatibility and optimizes efficiency.
Repetitive Use and Standardization
Aluminium formwork is ideal for projects with typical floors or repetitive layouts. By using standardized formwork systems and components, we can reduce material waste and increase efficiency. The repetitive use of ASF panels is another significant advantage, especially in projects with minimal design variations.
Training and Skill Updates
Ensuring our workforce is well-trained is critical. Thorough training programs on assembly, disassembly, and maintenance procedures help maintain safety and efficiency. Regular updates on the latest techniques and safety protocols related to aluminium formwork usage are also essential.
Comparison of Key Factors
Here's a comparison of key factors between conventional formwork and aluminium formwork to help visualize the benefits:
Requirement | Conventional Formwork | Aluminium System Formwork |
---|---|---|
Quality | Poor quality – in dismantling | Good quality – in dismantling |
Speed | Erection done at the site | Walls and floors cast together, daily cycle |
Repetitive Use | Limited repetitions | High number of repetitions possible |
Time Consumption | Nearly two weeks for 4,000 sqft floor | Approximately four days for the same area |
Evaluating Training Effectiveness
When it comes to evaluating the effectiveness of on-site aluminium formwork training, we need to focus on several key metrics that measure the impact on our construction workflow and workforce competence. The first step is to assess the knowledge retention and application of the training participants. This can be done through written tests and practical assessments, as seen in the holistic training programs offered by companies like JUSTFORM.
Participants are required to give PowerPoint presentations on what they've learned and undergo written tests to confirm they understand the material.
Another critical aspect is monitoring the time saved in installation and the reduction in errors. For instance, training packages that focus on formwork component identification and reading various formwork drawings can substantially streamline the construction process. By reducing the time spent on identifying components and making modifications on site, we can enhance overall productivity and efficiency.
Safety is also a crucial metric. Effective training should result in fewer accidents and a safer working environment. By emphasizing safety protocols, tools, and tackles, as outlined in the training program by VIP ALUFORM, we can guarantee that our workforce is better equipped to handle the demands of aluminium formwork construction safely.
Finally, feedback from the participants and site supervisors is essential. Regular review sessions and PowerPoint presentations, as part of the training schedule, help identify gaps in learning and allow for immediate adjustments to the training program. This continuous evaluation confirms that the training is tailored to meet the specific needs of our project, leading to a more competent and confident workforce.
Frequently Asked Questions
What Are the Different Types of Aluminium Formwork Systems?
When it comes to aluminium formwork systems, we've several types that cater to different construction needs.
We use beam-based systems, which are flexible and adaptable, made from individual aluminum beams.
Modular systems consist of pre-fabricated modules that assemble quickly on-site, offering speed and efficiency.
There are also monolithic systems, which are single, self-contained units providing exceptional strength and durability.
Additionally, we've precast, cast-in-place, and post-tensioned forms, each with its own advantages and suitable applications.
How Often Should Workers Be Updated With New Techniques and Safety Protocols?
We need to keep our workforce updated with the latest techniques and safety protocols regularly. This is vital for guaranteeing both safety and efficiency on the construction site.
We should provide thorough training programs and make certain our workers receive regular skill updates, especially whenever new safety standards or methods are introduced. This way, we can prevent accidents and maintain a high level of productivity.
Can Aluminium Formwork Be Customized for Unique Architectural Designs?
We can definitely customize aluminium formwork for unique architectural designs. These systems are tailored to accommodate complex shapes and structural elements, making them ideal for projects that require specific and intricate details.
Customized aluminium formwork guarantees that every aspect of the design is met with precision and accuracy, allowing us to bring innovative and complex architectural visions to life efficiently.
What Is the Typical Duration of an Aluminium Formwork Training Program?
When it comes to aluminium formwork training, the duration can vary, but we've found that exhaustive programs typically last around 5 days.
For instance, the VIP ALUFORM training program spans 5 days with 2 hours of classes each day, totaling 14 hours of instruction. This timeframe allows for thorough coverage of key topics, ensuring we're well-equipped to handle the system efficiently.
Are There Specific Physical Fitness Requirements for Handling Aluminium Formwork Panels?
When handling aluminium formwork panels, we need to take into account the physical demands of the job. While aluminium formwork is lightweight, it still requires physical strength and stamina.
The work involves heavy lifting and working in challenging conditions, so a good level of physical fitness is essential. This includes the ability to handle panels that, although lighter, can still be cumbersome and require significant effort to maneuver and assemble.
Conclusion
By investing in on-site aluminium formwork training, we streamline our workflow, enhance safety, and boost efficiency. Proper training guarantees our team follows strict safety protocols, masters assembly and disassembly techniques, and maintains the formwork meticulously. This not only optimizes our construction process but also extends the lifespan of our equipment. Effective training evaluation helps us identify areas for improvement, making our projects safer, faster, and more successful.