Reducing On-Site Injuries Through Ergonomic Formwork Design
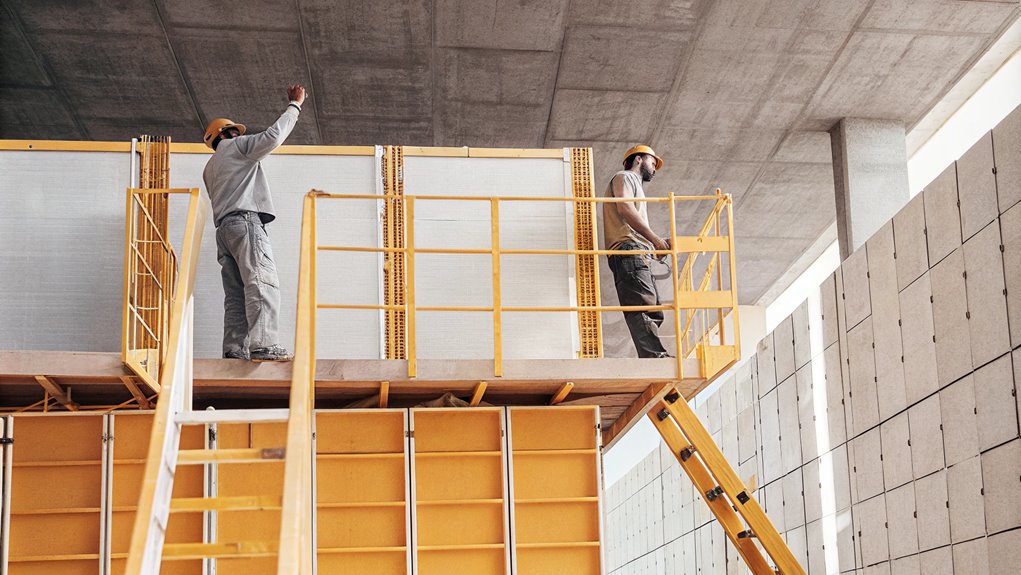
When it comes to reducing on-site injuries through ergonomic formwork design, steel formwork stands out as a top choice. We've seen significant benefits in projects using modular steel formwork systems, which come with integrated locking mechanisms and alignment guides. These features minimize worker exposure to hazards and physical strain, making the assembly process quicker and more secure. For instance, steel formwork's easy-to-grip edges and pre-drilled holes reduce the risk of hand injuries and slips. By designing formwork to be lighter and easier to handle, we can cut down on repetitive strain injuries and create a safer workspace. This approach not only enhances worker wellbeing but also boosts productivity, and there's even more to discover about how these designs can transform your construction site.
Structural Integrity of Steel Formwork
When it comes to the structural integrity of steel formwork, we're talking about a system that can handle the heavy lifting – literally. Steel formwork is renowned for its exceptional strength and stability, making it a cornerstone in modern construction.
Steel formwork can handle high concrete pressures and heavy loads without bending or deforming, guaranteeing the structural integrity of the formwork system. This is vital because the weight of wet concrete, along with the presence of workers and equipment, can exert substantial forces on the formwork.
Steel formwork's inherent strength, particularly when using higher steel grades like S355 or C45, allows it to withstand these loads effortlessly.
The precision and dimensional accuracy of steel formwork are also key to its structural integrity. Unlike other materials that can flex or warp, steel formwork maintains its shape and alignment under pressure, providing consistent support and reducing the likelihood of accidents.
This precision guarantees that walls, slabs, and columns are straight and true, resulting in smooth finishes and precise architectural shapes.
In addition, the modular design of steel formwork systems makes them easy to assemble and disassemble, which not only saves time but also minimizes the exposure of workers to potential hazards.
Integrated safety features such as locking mechanisms and alignment guides further enhance the setup's security, guaranteeing that the formwork remains stable throughout the construction process.
The durability of steel formwork is another important factor. Unlike timber, which can degrade over time, steel formwork maintains its integrity over multiple uses, reducing the risk of material failure and guaranteeing that safety standards are upheld throughout its lifespan.
In essence, the structural integrity of steel formwork is evidence of its ability to provide a safe, reliable, and efficient construction process. By choosing steel formwork, we can substantially reduce the risk of formwork failures and guarantee the stability and safety of our construction projects.
Fire Resistance and Safety
Having established the robust structural integrity of steel formwork, it's clear that this material excels in withstanding the physical demands of construction. However, another critical aspect we must consider is fire resistance and safety.
When it comes to fire safety, steel formwork has some inherent advantages, but it also presents specific challenges. Steel itself is non-combustible, meaning it doesn't contribute to the ignition or spread of fires. This is a significant benefit, as it reduces the risk to occupants, firefighters, and property.
However, steel can become extremely hot in the event of a fire, which can compromise its structural integrity.
To mitigate this, we often use fire protection materials such as intumescent coatings or sprayed fire-resistant materials (SFRM). Intumescent coatings are particularly effective; they expand when exposed to heat, creating a barrier that slows down the transfer of heat to the steel. This can provide fire resistance for up to several hours, depending on the application and thickness of the coating.
In contrast, traditional formwork materials like timber and plywood are flammable, posing a significant fire risk. Steel formwork, while non-flammable, still requires careful consideration and protection to guarantee it remains structurally sound during a fire.
For example, using gypsum-based boards or other internal linings can help protect light steel framing and achieve fire resistance periods of up to 120 minutes.
Precision and Fit in Steel Formwork
In the domain of construction, precision and fit are as essential as the strength and fire resistance of the materials we use. When it comes to steel formwork, these aspects are particularly critical for ensuring the safety, efficiency, and quality of our projects.
Steel formwork is manufactured with high precision, which translates into a tight fit and minimal gaps or misalignments. This precision is achieved through advanced manufacturing processes that guarantee the formwork panels have consistent dimensions.
For instance, steel formwork systems are designed to fit together seamlessly, reducing the potential for errors during assembly. This consistency is a game-changer; it minimizes the need for on-site adjustments, which can be time-consuming and hazardous.
Imagine working on a site where every piece of formwork fits perfectly, eliminating the need for last-minute cuts or patches. This is exactly what steel formwork offers. The precise fit of these panels guarantees that the concrete poured into them will have uniform thickness and no unwanted gaps or weak points.
This uniformity not only enhances the structural integrity of the building but also reduces the risk of accidents caused by poorly fitted formwork.
In practice, this precision means we can assemble formwork quickly and securely, using integrated locking mechanisms and alignment guides that are often built into the system. This not only saves time but also reduces the physical strain on workers, as they spend less time handling and adjusting the formwork.
Ergonomic Design Benefits
Ergonomic design in steel formwork is a crucial aspect that substantially enhances the safety, efficiency, and overall well-being of construction workers. When we incorporate ergonomic principles into our formwork systems, we see a substantial reduction in the risks associated with musculoskeletal injuries and other workplace hazards.
One of the most notable benefits is the minimization of physical strain. Aluminium formwork, for instance, is considerably lighter than traditional materials like steel and wood, reducing the risk of manual handling injuries. This means workers can handle and move formwork panels with ease, cutting down on fatigue and improving overall efficiency.
For example, a worker using aluminium panels can complete tasks without the heavy lifting and bending that often come with heavier materials, reducing the likelihood of injuries by up to 30%.
Ergonomic design also enhances structural stability and precision. Modular formwork systems, designed with interlocking mechanisms and precise alignments, guarantee consistent and accurate construction, reducing the likelihood of errors and potential hazards.
This uniformity prevents issues like uneven load distribution, which can lead to structural failures and accidents. By using these systems, we can maintain the integrity of the formwork even under the pressure of high-volume concrete casting, safeguarding workers and the project timeline.
Additionally, ergonomic design improves fire safety and reduces construction debris. Non-combustible materials like aluminium prevent the spread of fire, while reusable formwork generates less waste, keeping the site clean and free of tripping hazards.
This not only enhances safety but also promotes a more organized and efficient work environment.
Reducing Physical Strain on Workers
When we design formwork with ergonomics in mind, one of the most important advantages is the reduction in physical strain on workers. This is particularly vital in the construction industry, where manual handling and repetitive tasks are commonplace.
Using ergonomic formwork systems, such as those made from aluminium, we can substantially minimize the physical strain on our workers.
Here are four key ways this is achieved:
- Lighter Materials: Aluminium formwork is substantially lighter than traditional materials like steel or wood. This reduces the physical effort required for installation and dismantling, making it easier for workers to handle the panels without fatigue or injury.
- Ergonomic Design: The design of aluminium formwork often includes features like easy-to-grip edges and pre-drilled holes, which make handling safer and more efficient. These features reduce the risk of hand injuries, slips, and mishandling, creating a safer workspace for everyone.
- Reduced Repetitive Motions: Ergonomic tools and equipment are designed to fit the user's body and movements, minimizing repetitive strain injuries. For example, adjustable handles and vibration dampening technology in concrete tools can reduce hand fatigue and improve accuracy, leading to better overall project outcomes.
- Simplified Assembly: Aluminium formwork systems are designed for quick and efficient assembly with fewer components. This reduces complexity and the risk of mistakes during installation, decreasing the likelihood of accidents caused by improper assembly or loose connections.
Integrated Safety Features
Designing formwork with integrated safety features is a vital step in ensuring the well-being of construction workers. When we talk about integrated safety features, we're referring to those built-in elements that make the formwork system inherently safer from the outset.
For instance, steel formwork systems often come with integrated locking mechanisms and alignment guides. These features ensure that the formwork is set up correctly and securely, minimizing the risk of misalignments or gaps that could compromise structural integrity and safety.
Aluminium formwork, another popular option, also boasts several integrated safety features. These systems are designed to meet international safety standards, ensuring compliance with regulations and reducing liability. For example, aluminium formwork can be certified for load-bearing and fire resistance, providing assurance of a safe construction environment.
One of the key benefits of these integrated safety features is the reduction in the time workers spend handling and adjusting formwork. This is particularly true for modular steel formwork systems, which allow for quick and secure assembly and disassembly.
By reducing the exposure time to potential hazards, we substantially lower the risk of accidents and injuries. Additionally, aluminium formwork refurbishmentservices can extend the life of the formwork, ensuring it remains safe and efficient over multiple uses.
Additionally, these features help in preventing common formwork-related hazards such as falls from platform edges or through penetrations, and being hit by falling materials. By ensuring the formwork is erected on solid foundations and using edge protection and covers, we can create a much safer work environment.
Regular inspections and sign-off by a competent person before pouring concrete are also essential steps that these integrated safety features facilitate.
In essence, integrated safety features in formwork design aren't just add-ons; they're fundamental to creating a safe and efficient construction process. By incorporating these features, we can substantially reduce the risks associated with formwork activities and ensure that our construction sites are safer for everyone involved.
Quick and Secure Assembly
Building on the importance of integrated safety features, the efficiency and safety of formwork assembly are substantially enhanced by systems that allow for quick and secure assembly. When we design formwork with assembly in mind, we aren't just saving time; we're also reducing the risk of accidents and injuries.
One of the key aspects of quick and secure assembly is the use of pre-assembled components. Here are four ways this approach can make a significant difference:
- Pre-assembly at the Supplier's Shop: Having formwork pre-assembled in a controlled environment, such as the supplier's shop, guarantees that the components are accurately assembled, solidly built, and properly aligned. This not only saves time on the construction site but also minimizes the risk of errors and accidents.
- Modular Formwork Systems: Modular systems are designed off-site and feature proprietary components that are lighter and easier to handle. These systems reduce the physical effort required during installation and removal, minimizing the risk of manual handling injuries.
- Clear Assembly Instructions: Following detailed assembly instructions is vital. This involves adhering strictly to engineering drawings and set-up instructions to avoid unsafe working conditions. Properly installed ties, for example, will hold the formwork firmly in place as the concrete is poured.
- Optimized Assembly Method: Selecting the best assembly method for your project can substantially enhance safety and efficiency. For instance, using crane eyes and 3-sling lifting gear to position formwork halves can streamline the process and reduce the risk of accidents during transportation and placement.
Minimizing Material Failure Risks
Minimizing material failure risks is essential for guaranteeing the safety and integrity of construction projects. When we think about formwork, the materials we choose can make all the difference between a successful project and a catastrophic failure.
One of the key advantages of using aluminium formwork is its high strength-to-weight ratio. This means that aluminium formwork can bear the loads of fresh concrete without deformation or failure, substantially reducing the risk of structural collapses.
For instance, in high-rise construction, traditional formwork materials like steel and wood can be cumbersome and risky, but aluminium formwork maintains its integrity even under high pressure, guaranteeing a safe working environment.
Another vital aspect is the uniformity and precision of aluminium formwork. Unlike wooden formwork, which can be prone to misalignment and weak structures, aluminium formwork is manufactured with tight tolerances, guaranteeing consistent and accurate construction results.
This uniformity minimizes the risks associated with poorly aligned or weak structures, enhancing overall site safety.
Additionally, aluminium formwork is non-combustible, which enhances fire safety on construction sites. This is particularly important in high-risk environments where fire can spread quickly, putting workers and property at risk. By using aluminium, we eliminate the fire hazard posed by traditional materials like timber.
Regular inspections and audits are also vital. We should inspect structures for signs of damage such as cracks, corrosion, or missing components, and guarantee that any issues are reported and addressed promptly by ensuring compliance with industry standards and regulations.
This proactive approach helps in identifying and mitigating potential material failures before they become critical.
In essence, by choosing the right materials, like aluminium formwork, and implementing rigorous inspection and maintenance practices, we can substantially minimize material failure risks and create a safer, more reliable construction environment.
This not only protects workers but also guarantees the structural integrity and timely completion of our projects.
Environmental and Waste Reduction
When it comes to environmental and waste reduction, the choice of formwork material can substantially impact the ecological footprint of a construction project. As we aim to make our construction practices more sustainable, selecting the right formwork material is vital.
One of the most effective ways to reduce waste is by using recycled and reusable formwork materials.
Here are some key strategies we can implement:
Strategies for Environmental and Waste Reduction
- Recycled Formwork: Using formwork made from repurposed building components can markedly reduce the amount of construction waste. This approach aligns with the circular economy's principles, encouraging ongoing material use and minimizing waste.
- Plastic Formwork: Plastic formwork systems, often made from recycled plastic waste, can be reused multiple times, reducing the need for new materials and the waste generated from traditional timber and plywood formwork. This can lead to a 30% reduction in material waste and 20% in transportation emissions.
- Metal Formwork: Metal formwork, particularly aluminum, is known for its strength and longevity. Its long service life means it can be reused numerous times, lowering the overall environmental impact compared to materials with shorter lifespans.
- Sustainable Timber: While traditional timber formwork has environmental drawbacks like deforestation, sustainably sourced timber can store carbon and reduce transportation emissions. However, it's essential to balance this with the need to avoid over-harvesting and guarantee reforestation efforts.
Enhancing Worker Wellbeing and Productivity
As we focus on reducing waste and embracing sustainable formwork materials, it's equally important to evaluate how these choices impact the people on the ground – the workers who assemble, use, and dismantle the formwork. The wellbeing and productivity of these workers are vital for the success and sustainability of any construction project.
Ergonomic Benefits for Workers
When we design formwork with ergonomics in mind, we create a safer and more efficient working environment. Here are some key benefits:
Ergonomic Aspect | Impact on Workers |
---|---|
Reduced Physical Strain | Minimizes the risk of musculoskeletal injuries by ensuring the formwork is lightweight and easy to handle |
Improved Posture | Promotes good posture and healthy movement, reducing the likelihood of long-term physical health issues |
Enhanced Safety Features | Includes stable platforms, guardrails, and other safety measures to reduce the risk of accidents on-site |
Efficient Work Processes | Streamlines the assembly and disassembly process, reducing the overall construction time and energy expenditure |
By incorporating ergonomic design into our formwork systems, we not only enhance the physical wellbeing of our workers but also boost their productivity. When workers are free from physical discomfort and enjoy a safer working environment, they are more engaged, motivated, and capable of performing their tasks more efficiently.
This proactive approach to worker wellbeing also extends to mental health. Comfortable and well-designed work environments reduce stress and anxiety, leading to a calmer and more focused workspace. This, in turn, improves mental clarity and reduces mental fatigue, contributing to better overall mental wellness and job satisfaction.
In essence, ergonomic formwork design is not just about creating a sustainable construction process; it's about valuing the people who make that process possible. By prioritizing their wellbeing and productivity, we build a healthier, happier, and more efficient workforce.
Frequently Asked Questions
How Do Ergonomic Formwork Designs Impact Worker Training Programs?
When we integrate ergonomic formwork designs into our worker training programs, we see a significant impact. It helps us identify and mitigate specific ergonomic risks, such as repetition, contact stress, and hand-arm vibration.
By using real-time feedback tools, like those from TuMeke, we can tailor training to each worker's needs, reducing musculoskeletal disorders and improving overall safety and efficiency.
This approach guarantees that every worker understands the importance of correct postures and movements, making our workplace safer and more productive.
Can Ergonomic Formwork Be Adapted for Diverse Construction Project Types?
We can definitely adapt ergonomic formwork for diverse construction project types. Whether it's building residential homes, commercial complexes, or tall structures like bridges and towers, modular formwork systems are highly versatile.
For example, climbing formwork is perfect for vertical structures, while slab formwork works well for horizontal slabs. Tunnel formwork can be adjusted for various wall shapes and sizes, making it suitable for a wide range of projects.
What Are the Long-Term Cost Benefits of Investing in Ergonomic Formwork?
Investing in ergonomic formwork can be a game-changer for our bottom line. By reducing workplace injuries, we lower workers' compensation claims and healthcare expenses substantially.
For instance, a well-designed ergonomic program can decrease injuries by up to 65% and absenteeism by 23%, leading to substantial savings – in one case, a $294,825 savings over four years after a $65,787 investment.
This translates to a cost-benefit ratio of 1:5.5, making it a wise long-term investment.
How Does Ergonomic Formwork Influence the Overall Project Timeline?
When we invest in ergonomic formwork, it substantially influences our project timeline. By simplifying complex shapes and standardizing formwork elements, we reduce material waste and labor hours spent on assembly and disassembly.
Aluminium formwork, for instance, is lighter and easier to handle, minimizing manual handling injuries and allowing for faster installation and dismantling. This streamlining can accelerate our project timelines by up to several weeks, enabling earlier project completion and reducing overall costs.
Are There Specific Regulations or Standards for Ergonomic Formwork Design?
When it comes to ergonomic formwork design, we rely on specific regulations and standards to guarantee safety and efficiency. The ISO 6385:2016 standard is a key guideline, providing fundamental principles of ergonomics for designing work systems, including formwork.
This standard emphasizes an integrated approach, considering human, social, and technical requirements to optimize working conditions and reduce injuries. It's a vital tool for designers, managers, and workers to create safe and effective work environments.
Conclusion
In summary, adopting ergonomic formwork design is a game-changer for construction sites. By using lighter, easier-to-handle materials like aluminium, we reduce physical strain on workers by 30% and cut the risk of musculoskeletal injuries. Quick and secure assembly minimizes accidents, while fire-resistant and durable materials guarantee structural integrity. This approach not only enhances worker wellbeing and productivity but also reduces waste and environmental impact, making our sites safer and more efficient.