How Iot Sensors Are Enhancing the Monitoring of Formwork Stability
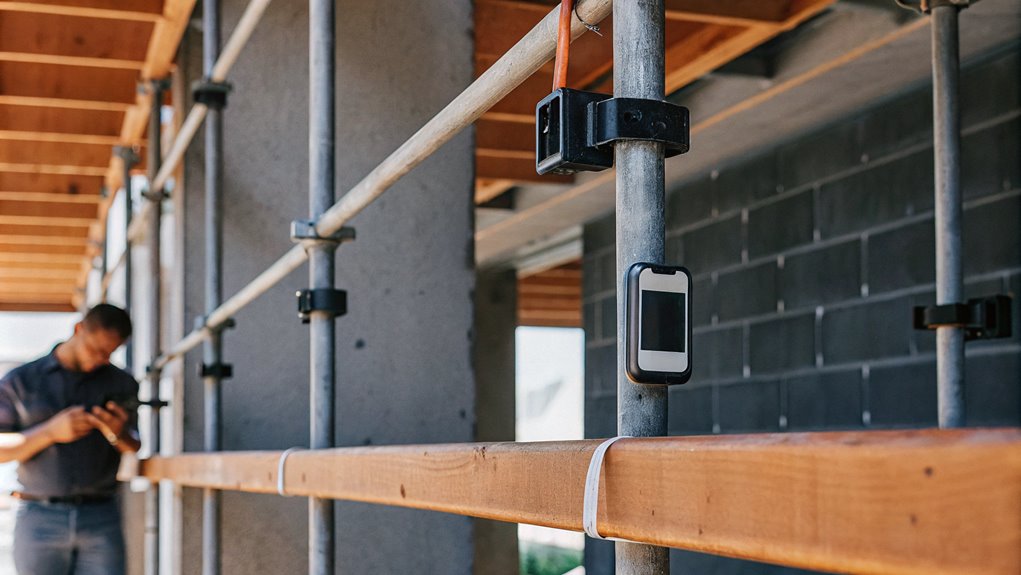
IoT sensors are drastically enhancing the monitoring of formwork stability by providing us with real-time data on vital parameters like temperature, humidity, and structural strain. These sensors, such as those in the MONSEC system, are distributed throughout the formwork and transmit data to a central system or cloud platform for immediate analysis and alerts. This allows us to detect potential issues before they become major problems, ensuring the structural integrity and safety of the construction site. For instance, force and strain sensors alert workers if loads exceed the structure's capacity, and environmental sensors detect hazardous conditions like toxic gas leaks. By continuous monitoring and automated alerts, we can optimize resource utilization, prevent delays, and make data-driven decisions promptly. If you're curious about how these advancements can further streamline your construction processes, there's more to explore.
IoT Sensors in Scaffold Monitoring
When it comes to guaranteeing the stability and safety of scaffolding during concrete formwork, IoT sensors have emerged as a game-changer. These sensors are part of what's often termed "smart scaffolding," a system that combines wireless sensors, computer software, and machine learning algorithms to automate monitoring and enhance safety.
Imagine a construction site where scaffolds stretch high into the air, supporting workers and heavy loads. Traditionally, monitoring these structures involved manual checks and periodic inspections, which could be time-consuming and prone to human error.
With IoT sensors, this process is revolutionized. Wireless displacement sensors, for example, can be installed directly on the scaffolding to monitor slab settlements and horizontal displacements in real-time. These sensors eliminate the "blind areas" that optical monitoring systems often miss, providing an exhaustive view of the scaffold's condition.
Force and strain sensors are also vital. They detect axial forces acting on the columns and alert workers if loads exceed the structure's capacity. Angle sensors monitor angular displacements, and fracture wire or tension link load cells detect any fracture or removal of anchors.
This continuous monitoring guarantees that any potential failure is identified and addressed promptly, preventing accidents and saving lives. Effective site supervision, such as ensuring adherence to installation plans and specifications, is also crucial in maintaining safety and quality.
The data collected by these sensors is sent to a central monitoring application via wireless communication, eliminating the need for cables and reducing safety risks. This data is then analyzed in real-time, providing actionable insights and triggering alarms or warnings if necessary.
Machine learning algorithms further enhance the accuracy of these predictions, helping to generate finite-element models of the scaffold system to study its load-bearing capacity.
In essence, IoT sensors in scaffold monitoring aren't just tools but guardians of safety, guaranteeing that construction sites are safer and more efficient. They're evidence to how technology can liberate us from the risks and inefficiencies of traditional methods, making our workplaces better and our lives safer.
Eliminating Blind Areas in Monitoring
In the domain of scaffold monitoring, one of the most significant challenges has always been the presence of "blind areas" – areas that traditional optical monitoring systems can't see. These blind spots can hide critical issues, such as structural weaknesses or material failures, which can lead to catastrophic collapses.
However, with the advent of IoT sensors, we're now able to eliminate these blind areas and guarantee thorough monitoring of our scaffolding systems, particularly in structures like those using aluminium formwork systems.
IoT sensors are designed to be installed directly within the scaffold structure, allowing us to monitor every aspect of the system in real-time. Unlike optical monitoring instruments that can only observe the outer rim of the scaffold, these wireless sensors can be placed at various points inside the structure.
For instance, wireless displacement sensors can measure slab settlement and horizontal displacement, providing detailed data on the scaffold's stability.
These sensors are wireless, which means they don't require cables or extensive installation procedures. This not only makes them easier to set up but also guarantees that the monitoring process is uninterrupted and efficient.
In practical applications, these IoT sensors have already proven their effectiveness. For example, in a project where an IoT-based monitoring system was implemented, it successfully detected the breaking of a slab and alerted the project managers, preventing a potential collapse.
Real-Time Data Collection
Real-time data collection is a cornerstone of IoT sensor systems in scaffold monitoring, enabling us to respond swiftly to any changes or potential hazards. With IoT sensors, we can gather and transmit data continuously, ensuring that every aspect of the formwork is closely monitored.
In the context of scaffold shoring systems, these sensors can be installed directly within the structure, eliminating the blind areas that traditional optical monitoring methods often miss. For instance, wireless displacement sensors can track the settlement and horizontal displacement of the scaffold, providing critical insights into its stability.
The real-time data collected by these sensors is transmitted to a central monitoring system or cloud platform, where it can be analyzed and visualized. This allows construction managers to keep a constant eye on the health of the formwork, receiving immediate alerts if any parameters exceed safe limits.
For example, the MONSEC system uses ultra-low consumption wireless sensors to measure temperature and humidity within the formwork, providing real-time information on concrete strength and maturity. This data helps in optimizing the concrete curing process and ensuring the formwork is removed at the ideal moment.
The frequency of data collection is also a major advantage. Systems like the intelligent high-formwork support monitoring system can obtain equipment monitoring data every two seconds, which is then transmitted to a database for real-time analysis and visualization.
This rapid data acquisition and transmission enable quick decision-making and timely interventions, substantially enhancing the safety and efficiency of the construction process.
Detecting Potential Malfunctions
Detecting potential malfunctions in scaffold shoring systems is essential for preventing collapses and guaranteeing construction safety. When we talk about formwork stability, we're not just discussing numbers and data; we're talking about the safety of the people working on the site and the integrity of the structure being built.
Using IoT sensors, we can monitor the scaffold shoring system in real-time, which is a game-changer. These sensors can be installed at critical points, such as the middle of beams, where the load is highest. They track parameters like strain, temperature, and humidity, sending alerts if there are any deviations from expected values.
For instance, if a sensor detects that a certain component is nearing its critical buckling strength or if there's a failure in the materials, it can send an immediate alarm to the managers and workers via a mobile client or SMS.
This proactive approach allows us to identify and address issues before they become major problems. In one practical application, an IoT-based monitoring system detected a broken slab in a scaffold shoring system, preventing a potential collapse.
By continuously monitoring the health of the scaffold, we can extend its lifespan, reduce the risk of accidents, and guarantee that the construction project stays on track. Ensuring compliance with industry standards is also crucial, as it helps maintain the quality and safety of the formwork products.
The data collected by these sensors isn't just reactive; it's also predictive. By analyzing trends and patterns, we can anticipate potential malfunctions and perform maintenance before anything goes wrong.
This not only saves time and money but also enhances worker safety and the overall quality of the construction project. With IoT sensors, we're not just monitoring formwork; we're safeguarding the future of our buildings and the people who build them.
Material Failure Prevention
Preventing material failures in scaffold shoring systems is crucial for maintaining the integrity and safety of construction projects. When we think about the risks involved in construction, the stability of the materials used in scaffolding is paramount.
IoT sensors are designed to monitor the health and condition of scaffold shoring systems in real-time. By installing these sensors at critical points, such as the middle of beams and other load-bearing areas, we can detect early signs of material failure.
Here are some key ways IoT sensors help in material failure prevention:
- Real-time Monitoring: IoT sensors continuously collect data on factors like stress, deformation, and environmental conditions that could affect the scaffold's structural integrity. This real-time data allows us to take immediate action if any anomalies are detected.
- Predictive Alerts: These sensors can trigger alerts when they detect conditions that could lead to material failure, such as excessive stress or instability. This proactive approach enables us to address issues before they become major problems.
- Automated Safety Protocols: When IoT sensors detect a potential material failure, they can automatically trigger safety protocols, such as alerts to site managers and emergency shutdowns if necessary. This guarantees that workers are promptly notified and can evacuate the area if there's a risk of collapse.
- Ensuring the longevity of formwork systems, such as those provided by Fommec Global Private Limited, which can be reused up to 150 times, is also critical in preventing material failures and maintaining overall construction efficiency.
Enhancing Construction Safety
Enhancing construction safety is at the heart of what IoT sensors can achieve in the scaffolding sector. When we think about construction sites, we often imagine bustling areas with workers, machinery, and a myriad of potential hazards.
IoT sensors are revolutionizing this landscape by providing real-time data that helps us identify and mitigate risks before they become serious issues.
One of the key ways IoT sensors enhance safety is through continuous monitoring of various parameters. For instance, wearable IoT devices can track workers' physiological conditions, such as fatigue or heat stress, and alert supervisors if there's a problem.
Environmental sensors can detect hazardous conditions like toxic gas leaks or structural instabilities in the scaffolding, allowing for immediate intervention.
These sensors also facilitate seamless communication between workers and supervisors, ensuring everyone is informed about current conditions and any emerging safety concerns. Drones equipped with IoT capabilities can offer aerial views for site inspections, while sensors on the ground provide detailed real-time data on equipment performance and environmental conditions.
This holistic monitoring approach reduces the risk of accidents due to miscommunication or coordination errors.
In practical terms, IoT-based monitoring systems, like those used for scaffold shoring systems, can detect malfunctions and material failures before they lead to collapses. For example, an IoT system installed on a scaffold shoring system can monitor critical spots where the load is large and alert managers in real-time if there are any issues, such as a broken slab or instability in the scaffold.
Optimizing Resource Utilization
When it comes to optimizing resource utilization on construction sites, IoT sensors play a crucial role in streamlining operations and reducing waste. These sensors are the unsung heroes that help us manage our resources more efficiently, ensuring that every piece of equipment, every drop of fuel, and every hour of labor is used to its fullest potential.
Imagine having real-time data on the health and performance of your machinery. IoT-enabled sensors can monitor equipment health, alerting us to potential issues before they become major problems. This proactive approach allows us to schedule maintenance ideally, minimizing downtime and repair costs.
For instance, IoT-enabled fuel sensors help us manage fuel consumption efficiently, optimizing refueling operations and reducing unnecessary waste.
Here are a few ways IoT sensors help us optimize resource utilization:
- Efficient Fleet Management: With IoT telematics, we can track vehicles, monitor fuel levels, and optimize routes in real time. This helps prevent unnecessary wear and tear on our vehicles, lowers operational costs, and keeps projects moving smoothly.
- Predictive Maintenance: Sensors can detect potential issues in equipment before they become costly breakdowns. By scheduling preventative maintenance ideally, we minimize downtime and reduce repair costs.
- Resource Tracking: IoT sensors enable us to track the precise location and utilization of materials and equipment. This eliminates waste and unnecessary costs, ensuring that everything is available and functioning when needed.
Preventing Unnecessary Delays
Delays on construction sites can be costly and frustrating, especially when they could have been avoided. This is where IoT sensors come into play, revolutionizing the way we monitor formwork stability and prevent unnecessary delays.
With IoT technology, we can guarantee that our construction projects stay on track. Here's how:
Real-Time Monitoring
IoT sensors, such as those used in the MONSEC® system, provide real-time data on the conditions inside the formwork. These sensors measure temperature, humidity, and other critical parameters, allowing us to monitor the concrete setting process accurately and make informed decisions promptly.
Early Detection of Issues
These sensors can detect potential issues before they become major problems. For example, if there is an anomaly in the concrete setting process, the sensors can alert us immediately, enabling us to take corrective action and prevent delays. In one instance, an IoT-based monitoring system detected a broken slab and concrete bursting out, which could have led to a significant delay if not addressed quickly.
Efficient Resource Allocation
Here's a breakdown of how IoT sensors help in preventing delays:
Aspect | Traditional Method | IoT-Based Method |
---|---|---|
Data Collection | Manual, time-consuming | Automated, real-time |
Issue Detection | Late detection, often after damage | Early detection, proactive |
Decision Making | Based on delayed data | Based on real-time data |
Resource Allocation | Inefficient, reactive | Efficient, proactive |
Overall Impact | Increased risk of delays | Reduced risk of delays |
Advanced Data Analytics and Insights
Advanced data analytics and insights are essential in the integration of IoT sensors for formwork stability, as they enable construction teams to make informed, data-driven decisions promptly. When we talk about formwork stability, the accuracy and real-time nature of the data collected by IoT sensors are critical.
Here's how advanced data analytics transforms this process:
Real-Time Monitoring and Alerts
– Immediate Action: With IoT sensors, we can receive real-time data on the condition of the formwork. This allows us to identify potential issues immediately, such as the instability of the scaffold or material failures, and take prompt action to prevent collapses.
Data-Driven Decision Making
– Optimized Resource Allocation: Advanced analytics help us understand where resources are being used efficiently and where adjustments are needed. This guarantees that materials and labor are allocated effectively, reducing waste and enhancing project efficiency.
Predictive Maintenance
– Preventing Failures: By analyzing the data collected from IoT sensors, we can predict when maintenance is required, preventing sudden failures that could delay the project or cause safety hazards. This proactive approach enhances the overall reliability of the formwork system.
In practice, this means we can monitor the temperature and humidity inside the concrete formwork in real-time. We can adjust the curing process accordingly to guarantee that the concrete achieves the required strength on time. This level of insights liberates us from relying on traditional methods and gut feelings.
Frequently Asked Questions
How Do Iot Sensors Handle Data Security and Privacy in Construction?
When it comes to handling data security and privacy in construction, we need to be vigilant. IoT sensors generate a lot of sensitive data, so we must safeguard it from cyber attacks.
We guarantee compliance with data protection requirements, restrict access to sensitive information, and monitor for any unauthorized system access. Our approach includes secure integrations, continuous monitoring for breaches, and swift action to minimize damage if a breach occurs.
This way, we protect our data and maintain trust.
What Are the Initial Costs and ROI of Implementing Iot Sensors in Formwork Monitoring?
When we implement IoT sensors for formwork monitoring, the initial costs can be significant. Hardware costs, which make up about 30% of the total, can vary but start as low as $0.38 per sensor.
However, an extensive system can range from $40,000 to $120,000 or more, depending on the complexity and scope of the project.
The ROI is substantial though; real-time monitoring and predictive maintenance can minimize downtime, reduce costly repairs, and enhance overall site safety and efficiency, leading to major cost savings and improved productivity.
Can Iot Sensors Be Integrated With Existing Construction Management Systems?
We can definitely integrate IoT sensors with our existing construction management systems. By connecting these sensors to our current infrastructure, we can stream real-time data directly into our project management tools.
This integration allows us to track site conditions, monitor asset performance, and adjust workflows dynamically, all while keeping our projects on schedule and budget. It's a seamless way to enhance our operations and make informed decisions quickly.
How Often Do Iot Sensors in Formwork Need Maintenance or Battery Replacement?
When it comes to maintaining IoT sensors in formwork, the frequency of maintenance and battery replacement can be a significant concern. Ideally, we'd want these sensors to be as hands-off as possible.
However, traditional battery-powered IoT sensors often need their batteries replaced regularly, which can be time-consuming and costly. For instance, if you have a large number of sensors, you might need to replace thousands of batteries annually, adding up to several replacements every day.
To liberate ourselves from this hassle, some companies are shifting towards self-powered sensors that eliminate the need for battery replacements altogether. This innovation can save us a lot of time and resources, ensuring our formwork monitoring runs smoothly without constant interruptions.
What Are the Potential Environmental Impacts of Using Iot Sensors on Construction Sites?
When we use IoT sensors on construction sites, we're not just improving efficiency and safety; we're also minimizing our environmental footprint.
These sensors help us monitor and comply with environmental regulations by tracking air quality, noise levels, and dust particles in real-time. This guarantees we reduce pollution, prevent hazardous conditions, and optimize energy consumption, making our construction processes more sustainable and environmentally friendly.
Conclusion
Using IoT sensors in scaffold monitoring has revolutionized the way we guarantee formwork stability. These sensors eliminate blind areas by being installed directly on the scaffold, providing real-time data on displacement, inclination, and axial forces. This immediate feedback helps detect potential malfunctions and prevent material failures, substantially enhancing construction safety. By optimizing resource utilization and preventing unnecessary delays, IoT sensors make our construction projects more efficient and safer for everyone involved.