How Digital Twins Can Enhance Formwork Planning and Execution
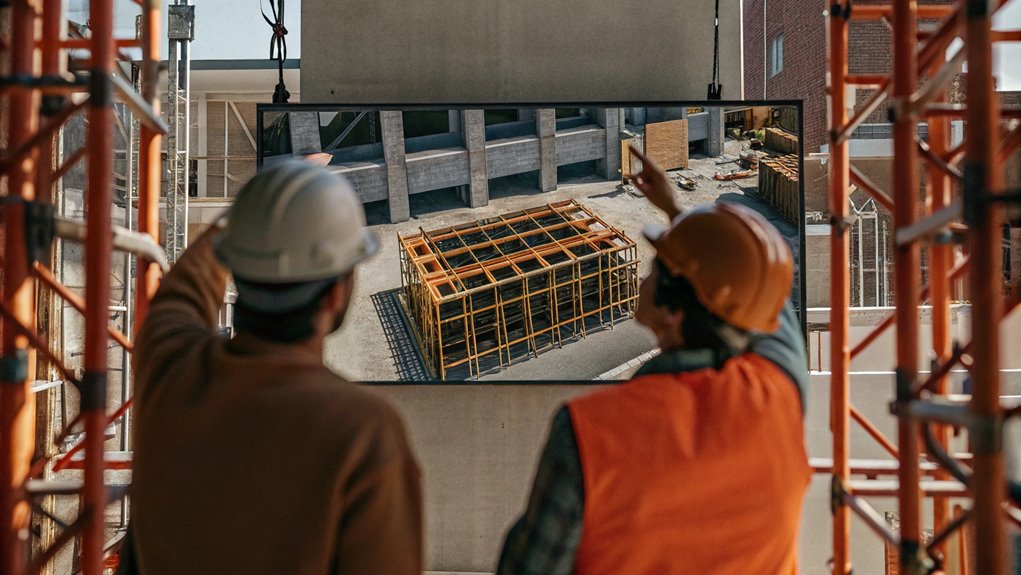
When we use digital twins in formwork planning and execution, we can substantially enhance the entire process. We create detailed virtual models of the proposed project, simulating multiple scenarios to test design options and identify potential issues. This allows us to optimize resource allocation in real-time, reducing costs and minimizing waste. Digital twins also enable us to make real-time design adjustments and visualize their impact, ensuring projects are completed on time and within budget. By integrating IoT and other measurement technologies, we get real-time updates on the project's status, enhancing visibility and facilitating better communication among team members. As we continue to utilize these tools, we'll uncover even more ways to streamline our workflow and improve project outcomes.
Enhanced Feasibility Studies
When it comes to formwork planning in construction, digital twins revolutionize the process by substantially enhancing feasibility studies. Imagine you're planning a complex construction project, and you need to guarantee that every aspect, from the design to the execution, is flawless. Digital twins make this possible by allowing us to create virtual representations of the proposed project.
With digital twins, we can perform more thorough feasibility studies than ever before. We simulate multiple scenarios and test various design options, which helps us identify potential issues early on.
For instance, if we're planning to construct a high-rise building, we can use digital twins to simulate different load conditions, environmental factors, and construction sequences. This allows us to optimize the design, estimate costs accurately, and assess the overall viability of the project.
These simulations also enable us to visualize the project in 3D, conduct virtual walkthroughs, and identify any clashes or inefficiencies. We can quickly iterate the design, making adjustments in real-time and seeing how these changes impact the project.
This level of detail and precision means we can create a more realistic project plan that considers a wide range of factors, reducing the risk of costly rework and delays.
Optimized Design and Planning
Building on the enhanced feasibility studies enabled by digital twins, we can now focus on optimizing the design and planning phases of formwork in construction projects. This is where the real power of digital twins comes into play, transforming what was once a cumbersome and error-prone process into a streamlined and highly efficient one.
With digital twins, we can create virtual models of our formwork designs, allowing us to test and evaluate different scenarios before any physical construction begins. This virtual environment enables us to identify and address potential issues, such as structural weaknesses or logistical bottlenecks, early on.
For instance, we can simulate various construction sequences to predict and mitigate risks, ensuring that our formwork is both stable and efficient.
The use of digital twins also allows for real-time monitoring and adjustments. We can track resource allocation, material use, and workforce deployment with unprecedented accuracy. This data-driven approach helps us optimize equipment allocation, reduce waste, and lower costs.
Imagine being able to adjust your formwork layout based on real-time data, ensuring that every beam and column is perfectly aligned and that the workforce is utilized to its fullest potential.
Moreover, digital twins facilitate the comparison of as-built vs. as-designed models, helping us detect any deviations from the original plan at the earliest stage. This proactive approach enables quick quality control measures and prevents further deflection from the original design.
By leveraging predictive analytics and AI, we can anticipate challenges and plan future phases more accurately, ensuring that our formwork isn't just functional but also of the highest quality.
In essence, digital twins turn the design and planning phase into a highly interactive and collaborative process. We can visualize, simulate, and optimize our formwork designs in a virtual space, making informed decisions that save time, reduce costs, and enhance overall project efficiency.
This is how we harness the full potential of digital twins in formwork planning, creating a smoother, more efficient construction process that benefits everyone involved.
Real-Time Design Visualization
How can we guarantee that our formwork designs are not just theoretically sound, but also visually aligned with the actual construction process? The answer lies in real-time design visualization, a tool that has revolutionized the way we plan and execute formwork.
Real-time visualization allows us to generate high-quality renderings from our BIM or CAD models instantly. This capability is vital for several reasons:
With real-time visualization, we can engage clients more effectively by presenting them with photorealistic images of the formwork design. This eliminates the subjective interpretation of sketches and reduces misunderstandings. We can also answer key questions about daylight exposure, views, and other critical design aspects swiftly and intuitively.
In our design development phase, real-time visualization enables us to review and compare different design options rapidly. This not only streamlines our decision-making process but also confirms that we can incorporate last-minute changes without delaying the construction schedule. Additionally, this process ensures that our designs meet project specifications and compliance standards, a critical aspect emphasized in the role of a Formwork Designer.
Benefits of Real-Time Design Visualization
Benefit | Description |
---|---|
Client Engagement | Instantly share realistic visuals with clients to verify they understand the design. |
Design Assessment | Rapidly assess viewsheds, shading, and radiation exposure in the schematic design phase. |
Option Comparison | Quickly compare multiple design options and materials without switching views or interfaces. |
| Collaboration | Enhance collaboration across teams and geographical boundaries with real-time design changes.
Cross-Disciplinary Collaboration
As we explore the complexities of formwork planning, it becomes clear that effective cross-disciplinary collaboration is the linchpin that holds the entire process together. When architects, engineers, contractors, and other stakeholders work together seamlessly, the outcomes are far more innovative and efficient.
In the context of formwork planning, cross-disciplinary collaboration allows us to leverage a diverse array of skills and knowledge. Here are some key aspects of this collaboration:
- Integrated Problem Solving: By combining the expertise of architects, structural engineers, and construction managers, we can address complex issues from multiple angles, guaranteeing thorough and effective solutions.
- Resource Optimization: Cross-disciplinary teams can optimize resource use, reducing both costs and environmental impact. This is particularly important in formwork planning, where material selection and structural design can substantially affect the project's overall efficiency.
- Regular Workshops and Reviews: Conducting regular workshops and reviews helps team members understand the basics of each other's domains. This ongoing knowledge exchange fosters a deeper understanding of the project's various facets and guarantees that everyone is aligned with the project's goals.
- Utilization of Advanced Tools: Tools like Building Information Modeling (BIM) and digital twins enable cross-disciplinary teams to work on a single, shared model of the project. This minimizes miscommunication and aligns efforts effectively, leading to more accurate and efficient formwork planning.
- Ensuring compliance with building codes and safety standards, such as those required for aluminium formwork systems, is crucial and can be achieved through close collaboration among team members.
Through this collaborative approach, we can create formwork plans that aren't only structurally sound but also innovative, sustainable, and aligned with the project's overall vision.
Accurate Resource Planning
What if we could plan resources for formwork with unprecedented precision, cutting down on waste and saving both time and money? This is exactly what digital twins can offer in the context of formwork planning and execution.
Digital twins are virtual replicas of physical objects, processes, or systems that can be updated in real-time using data from various sources, including the Internet of Things (IoT) and other sensors. When applied to formwork planning, these digital models allow us to simulate the entire product lifecycle, optimizing the allocation of equipment, materials, and workforce.
Imagine being able to create a virtual representation of your formwork project, where you can input variables such as the number of employees, client demand, lead times, and selection ratios. This simulation enables you to forecast future performance and identify potential bottlenecks before they become actual issues.
For instance, if you're planning a concrete pour, the digital twin can help you sequence activities more efficiently, guaranteeing that the right materials and workforce are available at the right time. This is particularly crucial for project managers who must ensure timely delivery and budget adherence, as it allows for more accurate resource allocation and project timeline management.
This level of accuracy in resource planning minimizes delays and reduces waste. It allows project managers to make proactive decisions, such as adjusting the number of workers or the timing of material deliveries, based on real-time data and simulations.
By doing so, we can streamline the entire process, from design to execution, and guarantee that our formwork projects are completed on time, within budget, and to the highest standards.
In essence, digital twins empower us to manage resources with greater precision, leading to more efficient, cost-effective, and sustainable formwork projects. This technology isn't just about optimizing processes; it's about liberating us from the inefficiencies of traditional methods, allowing us to focus on what truly matters – delivering exceptional results.
Real-Time Project Monitoring
With accurate resource planning in place, the next step is to guarantee that our formwork projects are monitored in real-time to maintain efficiency and quality. This is where Digital Twins come into play, revolutionizing the way we manage and oversee our construction projects.
Digital Twins provide a virtual duplicate of our physical formwork project, integrating real-time data from various sources such as sensors, project management applications, and operational frameworks. This allows us to track progress, identify issues, and make informed decisions swiftly.
Some key benefits of using Digital Twins for real-time project monitoring include:
- Enhanced Visibility: We can create detailed 3D models of the project, giving us and our stakeholders a clear visual representation of the formwork's status. This helps in better communication and understanding among team members and clients.
- Real-Time Updates: The integration of IoT and other measurement technologies guarantees that our Digital Twin is updated in real-time, reflecting the current state of the project. This enables us to monitor key performance indicators and adjust our strategies accordingly.
- Early Issue Detection: With predictive analytics and scenario simulations, we can anticipate potential problems before they arise. This proactive approach reduces risks and uncertainties, leading to smoother project implementation.
- Improved Collaboration: Digital Twins foster better collaboration by providing a shared, up-to-date view of the project. This guarantees that all team members are on the same page, enhancing communication and coordination across different teams and disciplines.
Predictive Maintenance Strategies
Predictive maintenance is the backbone of guaranteeing our construction projects and completed assets operate at peak efficiency throughout their lifecycle. When we integrate Digital Twins into our maintenance strategies, we gain a powerful tool that transforms how we manage and maintain our buildings and infrastructure.
Imagine having a virtual replica of your physical assets, continuously gathering real-time data from embedded sensors. This is what Digital Twins offer. They enable us to shift from traditional scheduled maintenance to condition-based maintenance, where maintenance activities are triggered automatically based on the actual condition and performance of the asset.
This approach minimizes unnecessary maintenance and guarantees that repairs are performed at the ideal time, optimizing resource allocation and reducing costs by 4%.
By leveraging Digital Twins, we can analyze historical and real-time data to predict equipment failures before they happen. Advanced analytics and machine learning algorithms help us detect anomalies and potential issues, allowing us to take proactive measures such as replacing components or scheduling repairs.
This proactive approach can reduce maintenance costs by 25-35%, decrease downtime by 35-45%, and even extend the lifespan of our equipment by 20%.
Digital Twins also facilitate better collaboration among stakeholders by providing a shared, up-to-date view of the project. This enhances communication and coordination, guaranteeing that everyone is on the same page.
For existing buildings, Digital Twins can be created using high-resolution 3D scans and AI-enabled technology to identify structural issues, allowing us to design sustainable mitigative measures and maintain our assets efficiently throughout their entire lifecycle.
In essence, incorporating Digital Twins into our predictive maintenance strategies liberates us from the inefficiencies of traditional maintenance approaches, allowing us to make informed decisions, reduce costs, and guarantee our assets operate at their best.
This isn't just about maintenance; it's about creating a more efficient, safe, and sustainable future for our projects.
Efficient Asset Management**
When we think about managing our assets efficiently, we often realize that traditional methods can fall short. This is where Digital Twins come into play, revolutionizing the way we approach asset management in formwork planning and execution.
Digital Twins provide a virtual mirror of our physical assets, allowing us to monitor, analyze, and optimize their performance in real-time.
Here are some key ways Digital Twins enhance our asset management:
- Predictive Maintenance: Digital Twins enable us to anticipate issues before they arise, streamlining our maintenance schedules and reducing unexpected equipment shutdowns. This proactive approach saves time, cuts costs, and improves overall efficiency.
- Better Asset Utilization: By analyzing performance trends and usage data, we can identify underutilized assets and develop strategies to optimize their use. This guarantees that every piece of equipment is working at its peak, maximizing our return on investment.
- Improved Design and Testing: Digital Twins allow us to simulate different designs and test various scenarios in a virtual environment before implementing them in real life. This not only saves time but also guarantees that our assets are optimized from the outset.
- Centralized Asset Register: Digital Twins help us maintain a thorough and centralized asset register, keeping track of all our assets, their maintenance history, and their current status. This centralized repository reduces confusion, increases visibility, and makes it easier to make informed decisions about asset management.
- By integrating Digital Twins with aluminium formwork refurbishment, we can extend the lifespan of our formwork systems up to 200-250 repetitions, significantly reducing costs and enhancing overall project efficiency.
Frequently Asked Questions
What Are the Initial Investment Costs for Implementing Digital Twins in Formwork Planning?
When we think about implementing digital twins, the initial investment costs can vary widely.
For a basic digital twin platform, we're looking at costs between $35,000 to $50,000. If we opt for more advanced features or a larger, more complex setup, the costs can range from $50,000 to $90,000.
Additionally, there are costs for designing the digital twin ($10k to $20k), deployment ($15k), integration ($10k), and ongoing maintenance ($1,500 to $4,000).
How Do Digital Twins Address Cybersecurity Risks in Construction Projects?
When we implement digital twins in construction projects, we've to be keenly aware of the cybersecurity risks. These virtual replicas, interconnected with IoT devices and cloud services, can create vulnerabilities if not secured properly.
We use threat modeling to identify potential attack points and enhance encryption and secure communication protocols. Regular penetration testing helps us simulate real-world attacks, uncovering weaknesses before they can be exploited.
This proactive approach guarantees our digital twins are resilient and our data is protected.
What Are the Challenges in Integrating Digital Twins With Existing Legacy Systems?
When integrating digital twins with existing legacy systems, we face several challenges. First, we've to deal with the complexity of integrating data from old, often unstructured sources like CAD files, PDFs, and Word documents.
First, ensuring these systems can communicate effectively is a hurdle, as legacy equipment might lack the necessary hardware for digital data tracking.
Additionally, we must navigate the issue of data silos, where information is scattered across different software and systems. This requires robust integration and interoperability solutions. This can be time-consuming and resource-intensive, but using flexible digital twin software and APIs can help consolidate information into a single, accurate source.
How Can Organizations Overcome the Shortage of Skilled Personnel for Digital Twin Management?
To overcome the shortage of skilled personnel for digital twin management, we need to invest in local workforce training and upskilling.
Partnering with third-party industry leaders can help fill skill gaps.
We should also adopt agile methodologies for rapid development cycles, ensuring product managers and other teams, like data engineers and full-stack developers, receive the necessary training.
Additionally, leveraging digital twins as a training tool can help onboard less experienced personnel faster and more effectively.
What Legal and Regulatory Considerations Are Involved in Using Digital Twins for Infrastructure Projects?
When we use digital twins for infrastructure projects, we face several legal and regulatory challenges.
Data ownership and liability are key concerns; we need to clearly define who owns the data and who's liable in case of errors or damages.
Contracts must be detailed, covering data sharing, confidentiality, and intellectual property rights.
We also have to comply with data privacy laws and industry regulations, ensuring transparency and trust among all parties involved.
Conclusion
In summary, digital twins have revolutionized formwork planning and execution in profound ways. We can now conduct enhanced feasibility studies, optimizing designs and plans from the outset. Real-time design visualization and cross-disciplinary collaboration streamline our processes, reducing errors and rework. Accurate resource planning and real-time project monitoring keep us on track. Predictive maintenance strategies and efficient asset management guarantee our projects run smoothly and safely. With digital twins, we're not just building structures; we're building a better future.