Custom Aluminium Formwork for Complex Curved Structures
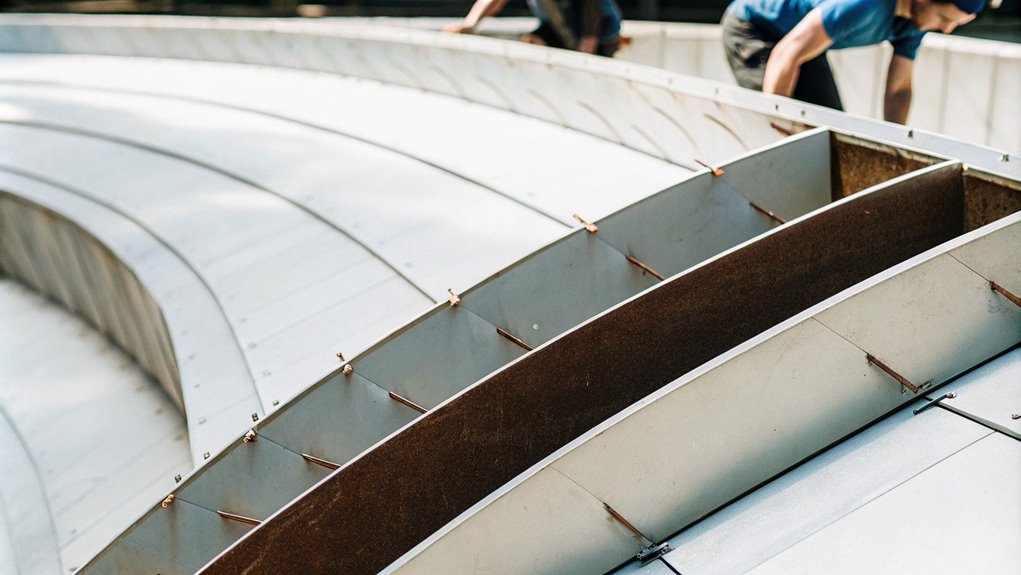
When it comes to constructing complex curved structures, we find that custom aluminium formwork is a game-changer. Its lightweight yet durable nature makes it easy to handle and transport, even without heavy machinery. Aluminium formwork can be reused up to 250 times, substantially reducing long-term costs and waste. For curved structures, flexible formwork systems and curved aluminium extrusions allow for precise and efficient shaping. Advanced CAD/CAM design and laser-guided systems guarantee high accuracy, enabling us to achieve smooth, uniform concrete surfaces. With its adaptability and reusability, aluminium formwork is perfect for innovative architectural designs, and if you continue, you'll see just how it can transform your construction projects.
Benefits of Aluminium Formwork
When it comes to constructing curved structures, one of the most invaluable tools in our arsenal is aluminium formwork. This technology has revolutionized the way we build, offering a multitude of benefits that make it an essential choice for any construction project.
First and foremost, aluminium formwork is incredibly lightweight, making it easy to handle and transport. This feature is a game-changer, especially for projects that involve complex or curved designs.
With an average weight of around 25 kg per square meter, we can easily manage and maneuver the formwork without the need for heavy machinery, saving both time and labor costs.
The durability and reusability of aluminium formwork are also significant advantages. These panels can be reused up to 300 times, which is a substantial reduction in the long-term costs associated with formwork.
This reusability, combined with the fact that aluminium is fully recyclable, makes it an eco-friendly choice that aligns with our commitment to sustainable construction practices.
Another critical benefit is the speed of construction. Aluminium formwork systems are designed for quick assembly and disassembly, allowing us to complete projects up to 20-30% faster than traditional methods.
This efficiency, coupled with the precision and consistency of the formwork, results in high-quality finishes that often eliminate the need for additional plastering or finishing processes.
In addition, aluminium formwork requires less skilled labor to install, making it more accessible and cost-effective. The panels are connected using simple pin and wedge systems, which can be managed by unskilled workers, further reducing labor costs and enhancing project feasibility.
Materials and Construction
In constructing curved structures with aluminium formwork, the choice of materials and the construction process are crucial for achieving the desired results. When we opt for aluminium, we're choosing a material that is not only lightweight and strong but also highly versatile and durable.
Aluminium extrusions can be curved into complex shapes, making them ideal for architectural features like curved walls, domes, and arches. Here's a breakdown of the key materials and techniques we use:
Material/Technique | Description | Benefits |
---|---|---|
Aluminium Extrusions | Curved into various shapes | Lightweight, strong, corrosion-resistant |
Phenolic Plywood | Used as formwork surface | Adapts to unique curvatures, easy to handle |
Flexible Formwork | Adjustable systems for curves | Precise, efficient, reduces labor time |
The construction process involves several innovative techniques. For instance, we use steam bending to shape wood into required curved forms, and 3D printing for precision and efficiency. Flexible formwork systems, such as the O-ROUND system, allow us to adjust the radius easily on-site without needing special equipment.
Aluminium formwork is also supported by advanced tools like laser-guided systems and computer-controlled bending machines, which enhance accuracy and efficiency. These tools guarantee that our constructions are not only aesthetically pleasing but also structurally sound and environmentally friendly, as aluminium is highly recyclable.
Flexible Formwork Techniques
As we leverage the strengths of aluminium in our formwork, we also incorporate flexible formwork techniques to achieve the intricate curves and complex shapes that define many modern architectural projects. Flexible formwork is a game-changer, allowing us to break free from the constraints of traditional rigid formwork and open up a world of creative possibilities.
One of the key advantages of flexible formwork is its versatility. Unlike static curved formwork, which has a predetermined shape and can't be adapted to different radii of curvature, flexible formwork can be shaped to the exact curves required for a specific structure.
This flexibility is achieved using materials such as steel or aluminum frames combined with materials like phenolic plywood or even fabric moulds. These materials can be prestressed or have their stiffness characteristics adjusted to assume the desired geometry, resisting the hydrostatic pressure of the concrete effectively.
In practice, this means we can create smooth, continuous curves in structures like roads, canals, and water channels, ensuring ideal hydraulic performance and aesthetic appeal. For example, in road construction, flexible formwork allows for faster installation and removal, reducing construction schedules and minimizing traffic disruptions.
It also eliminates the need for joints in curved sections, improving durability and reducing maintenance requirements.
Moreover, flexible formwork is highly adaptable and can be easily modified on-site to accommodate design changes or unforeseen adjustments. This adaptability not only speeds up the construction process but also reduces labor costs and material waste, aligning with sustainable construction practices.
Additionally, our aluminium formwork can be reused up to 150 times, maximizing re-usability, which further enhances the efficiency and sustainability of the construction process.
Curved Structure Applications
Curved structures, made possible by flexible and custom aluminium formwork, are transforming various sectors of construction with their unique aesthetic and functional benefits. These structures break free from the conventional boxy designs, offering a plethora of advantages that go beyond mere aesthetics.
In terms of aesthetics, curved structures create a sense of movement and flow, guiding the eye effortlessly around the space. This not only enhances the visual appeal but also imparts an organic and natural look, making the environment feel elegant and graceful.
Functionally, curved buildings are highly efficient. They can optimise the use of space, particularly in urban environments where land is limited. Rounded corners and walls eliminate wasted areas, creating more usable interior spaces.
Additionally, curved roofs promote better airflow and natural light distribution, contributing to more energy-efficient designs.
The strength and durability of curved structures are also significant. They offer superior resistance against wind and other external forces, making them ideal for areas prone to harsh weather conditions.
For instance, curved buildings can deflect strong gusts of wind and allow rain to slide off more easily, reducing the potential for water damage.
In residential and healthcare settings, curved shapes evoke a sense of enclosure and intimacy, fostering a sense of comfort. This makes them perfect for family homes and healthcare facilities where creating a welcoming environment is vital.
Furthermore, curved structures like dome-shaped shelters are used in various industries such as mining, transport, and agriculture due to their lightweight, cost-effective, and durable nature.
Precision and Accuracy
Achieving precision and accuracy in the construction of curved structures is crucial, and it's here that custom aluminium formwork truly shines. When we're talking about bringing intricate architectural visions to life, there's no room for error.
Here's how we guarantee that our custom aluminium formwork meets the highest standards of precision and accuracy:
Key Factors in Achieving Precision
1. Advanced CAD/CAM Design
We use state-of-the-art CAD/CAM software to design our formwork panels. This technology allows us to tailor each component to specific project requirements, guaranteeing precision in dimensions and configuration.
Our engineers meticulously plan every detail to optimize material usage and enhance structural integrity.
2. High-Precision Extrusion and Fabrication
Our aluminium formwork is processed through high-pressure extrusion lines, where heated aluminium billets are forced through precision-cut dies to form the desired shapes and profiles.
For components requiring thicker sections or intricate designs, we utilize casting processes that maintain impeccable accuracy.
3. Innovative Tools and Technologies
We employ cutting-edge tools like 3D printing, laser-guided formwork systems, and computer-controlled bending machines. These technologies enable us to visualize, plan, and execute complex curved forms with a higher degree of accuracy, reducing errors and wastage.
Techniques such as steam bending wood and using flexible systems like phenolic plywood also contribute to achieving the desired curvature with precision.
Assembly and Disassembly
When it comes to assembling and disassembling our custom aluminium formwork for curved structures, precision and efficiency are paramount. We recognize that the speed and ease of this process can make or break a project's timeline and budget.
That's why our aluminium formwork systems are designed with modular components that fit together seamlessly, allowing for rapid assembly and disassembly.
The modular nature of our aluminium formwork is a game-changer. Pre-designed panels and locking systems enable us to construct and remove the formwork in substantially less time than traditional methods. For instance, we can complete the assembly and disassembly of our formwork in as little as 4-7 days per floor, which is a substantial reduction compared to the weeks or even months required by other systems.
Our precision-engineered aluminium formwork is lightweight yet incredibly durable, making it easy to transport, assemble, and reposition on-site. This not only speeds up the construction process but also reduces our dependency on heavy machinery, which is particularly beneficial for projects in remote or space-constrained areas.
The lightweight nature of aluminium also means less labor is required, reducing the physical strain on our workers and enhancing site safety.
We've seen firsthand how our custom aluminium formwork can transform the construction process. With the ability to reuse these systems up to 250 cycles or more, we can guarantee consistent performance throughout the project lifecycle.
This reusability minimizes downtime caused by formwork replacement and markedly reduces overall construction costs. By streamlining the assembly and disassembly process, we're not just saving time and money; we're also guaranteeing that our projects are completed with the highest quality and precision.
Reusability and Sustainability
Our custom aluminium formwork systems are designed with reusability and sustainability at their core. When we talk about building complex curved structures, we're not just focusing on the aesthetics or the technical challenges; we're also committed to reducing our environmental footprint.
One of the most substantial advantages of our aluminium formwork is its durability and reusability. Here are three key ways this benefits both our projects and the planet:
1. Reduction in Construction Waste
Our aluminium formwork can be reused up to 200 times, considerably cutting down on the waste generated by traditional formwork materials like wood, which often end up in landfills after a few uses.
This not only reduces waste but also minimizes the need for constant replacements.
2. Energy and Resource Efficiency
Producing new formwork is energy-intensive, but since our aluminium systems can be reused multiple times, the initial energy investment pays off in the long run.
This reduces the continuous demand for new materials and the energy required to produce them, leading to lower carbon emissions.
3. Cost Savings and Circular Economy****
By reusing our aluminium formwork, we save on costs associated with purchasing new materials for every project.
Additionally, aluminium is fully recyclable, aligning perfectly with the principles of a circular economy.
This means that at the end of its life cycle, our formwork can be recycled without losing its properties, further reducing waste and energy consumption.
These benefits make our custom aluminium formwork systems a game-changer for sustainable construction.
We're not just building structures; we're building a greener future, one reusable form at a time.
Load Bearing Capacity
In constructing complex curved structures, the load bearing capacity of our custom aluminium formwork is a critical factor we meticulously address. When it comes to aluminium formwork, its ability to withstand heavy loads is one of its most compelling advantages.
Our aluminium formwork systems are designed to handle substantial pressure, ensuring that they maintain their shape and stability even under the weight of freshly poured concrete. Here are some key metrics that highlight the load bearing capacity of our custom aluminium formwork:
Component | Load Bearing Capacity | Weight | Reusability |
---|---|---|---|
Slab Panel | Up to 60 kN/m² | 13 kg | ≥ 300 times |
Wall Panel | Up to 60 kN/m² | 28 kg | ≥ 300 times |
Middle Beam | Shear force: 27.3 kN | 9 kg | ≥ 300 times |
End Beam | Shear force: 27.3 kN | 9 kg | ≥ 300 times |
Aluminium Formwork Beam | Moment: 16.8 kNm, Shear force: 50.0 kN | 6.4 kg/lin.m | ≥ 200 times |
These numbers are not just statistics; they represent the reliability and strength that our aluminium formwork brings to your construction site. The high load-bearing capacity, combined with its lightweight nature, makes it an ideal choice for complex curved structures. This means you can achieve the intricate designs you envision without compromising on safety or structural integrity.
In addition, the reusability of our aluminium formwork up to 300 times markedly reduces the overall construction costs and minimizes waste, aligning perfectly with our commitment to sustainability. When you choose our custom aluminium formwork, you are not only ensuring the structural soundness of your project but also contributing to a more environmentally friendly construction process.
Customization and Adaptability
Customizing aluminium formwork for curved structures is where our expertise truly shines, allowing us to adapt to even the most complex and unique architectural designs. When it comes to customization and adaptability, aluminium formwork stands out for its versatility and the precision it offers.
Here are a few key ways we tailor aluminium formwork to your specific needs:
- Flexible Curved Extrusions: We can curve aluminium extrusions into a variety of shapes and sizes, making them ideal for curved walls, domes, arches, and other architectural features that require a high degree of precision. This flexibility allows architects and builders to create custom designs that match the unique vision of each project.
- Precision Engineering: Our engineered aluminium formwork systems are designed with precision engineering and advanced techniques. These systems include prefabricated panels, beams, and props that are manufactured to guarantee seamless assembly and superior structural integrity. This precision is vital for achieving high-quality concrete finishes in complex construction projects.
- Adjustable Formwork Systems: For curved walls, we use systems like the O-ROUND formwork, which allows for the casting of curvilinear, closed, or semicircular walls with variable radii. This system is easily adjustable on site, eliminating the need for special tailored formworks and reducing the economic burden associated with them.
Our ability to customize and adapt aluminium formwork guarantees that we can meet the specific requirements of any project, no matter how complex or unique.
Whether it's bending alkus all-plastic facings to exact shapes or using curved aluminium extrusions for intricate designs, we're committed to delivering solutions that match your vision and needs perfectly.
This adaptability is what sets our aluminium formwork apart and empowers you to bring your most ambitious architectural designs to life.
Frequently Asked Questions
How Do Environmental Conditions Affect the Stability of Aluminium Formwork?
When it comes to environmental conditions, we need to evaluate how they impact the stability of aluminium formwork. Harsh weather, such as intense heat or cold, doesn't substantially compromise aluminium's structural integrity due to its high melting point and low coefficient of expansion.
It resists brittleness in cold and efficiently dissipates heat in hot conditions, ensuring it remains stable. Additionally, aluminium formwork is resilient against heavy snow and ice, and its corrosion resistance protects it from moisture and pollutants, making it reliable in various weather conditions.
What Safety Measures Are Essential for Workers Handling Aluminium Formwork?
When we handle aluminium formwork, safety is our top priority. We guarantee all workers wear personal protective equipment (PPE) like helmets, gloves, and safety boots.
Safety harnesses and guardrails are a must when working at heights to prevent falls. Regular inspections of the formwork and electrical equipment are vital to avoid defects and electrical hazards.
We also use proper lifting techniques and equipment, like cranes or hoists, to handle heavy panels safely.
Additionally, we conduct thorough safety briefings and have an emergency plan in place.
Can Aluminium Formwork Be Used in Areas With High Electrical Conductivity Risks?
When working with aluminium formwork in areas with high electrical conductivity risks, we must be extremely cautious. Aluminium can conduct electricity, so it's vital to guarantee all electrical equipment is properly insulated and grounded.
Regular inspections to detect any potential defects or signs of wear and tear are essential. We also need to keep electrical wires away from water sources and guarantee workers are equipped with the right personal protective equipment to prevent electrocution.
How Often Should Aluminium Formwork Be Inspected for Wear and Tear?
We need to inspect our aluminium formwork regularly to guarantee it lasts. After each use, we should clean the panels thoroughly to remove any concrete residue, dirt, or debris.
Then, we must inspect them carefully for any signs of damage, such as dents, cracks, or rust. This routine inspection helps us identify potential problems early, preventing them from becoming major issues.
We should also conduct periodic inspections before and after each cycle to maintain the formwork's integrity and extend its lifespan, which can be up to 200-300 cycles with proper care.
Are There Specific Training Requirements for Workers Using Aluminium Formwork?
When it comes to using aluminium formwork, we can't stress enough the importance of proper training for our workers. We need to guarantee they understand everything from safety protocols to the correct installation and handling of the formwork.
For instance, JUSTFORM offers thorough training packages that include identifying components, reading drawings, and achieving efficient cycle times, all with a mix of theoretical and practical sessions.
Additionally, programs like the one from VIP ALUFORM provide ISO certification and cover critical aspects such as safety, measurement, and the 8-day cycle process of aluminium formwork.
These trainings are vital for our workers' safety and the quality of our projects.
Conclusion
In summary, custom aluminium formwork is a game-changer for complex curved structures. It offers precision, flexibility, and reusability, making it ideal for unique architectural designs. With its high load-bearing capacity and ease of assembly and disassembly, aluminium formwork streamlines the construction process. It's perfect for curved walls, tunnels, and water treatment plants, ensuring smooth curves and superior performance. This isn't just about building; it's about creating functional, beautiful spaces that defy traditional boundaries.