Cost Optimization Through Modular Formwork Customization
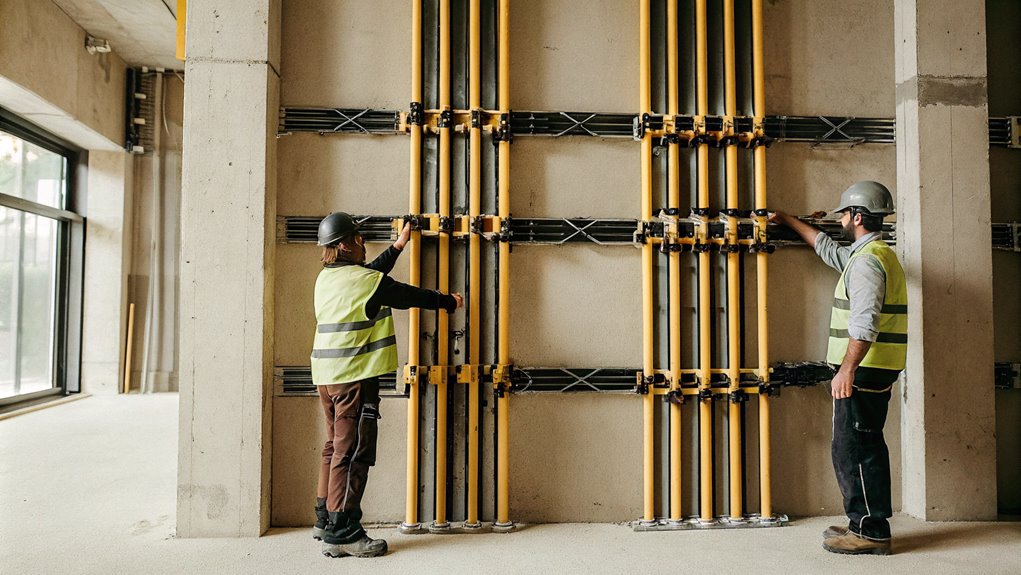
By leveraging modular formwork customization, we can substantially optimize costs in construction projects. This approach reduces material waste by up to 30% and labor costs by as much as 25%, while guaranteeing faster completion times and higher quality finishes. Customizable modules are designed to fit specific project needs, minimizing excess material and errors. Advanced software and 3D modeling guarantee precise engineering, reducing unnecessary cuts and mistakes. This method also allows for reusable components, just-in-time production, and streamlined processes, all of which contribute to a more sustainable and cost-effective construction process. Discover how these innovations can transform your next project.
Benefits of Modular Formwork
When it comes to construction projects, modular formwork stands out as a game-changer. We've seen firsthand how this innovative approach can transform the way we build, saving time, money, and resources.
First and foremost, modular formwork offers unparalleled efficiency. By using pre-fabricated modules, we can assemble and disassemble the formwork quickly and easily. This not only accelerates the construction process but also reduces labor costs substantially.
Unlike traditional methods that require extensive on-site preparation and customization, modular formwork is ready to go as soon as it arrives on the site.
Another substantial advantage is its versatility. Modular formwork systems are highly adaptable and can be customized to fit various project requirements. Whether we're working on a sleek skyscraper or a complex infrastructure project, these modules can be rearranged and reused multiple times without losing their integrity.
This flexibility reduces waste and minimizes the environmental impact of our projects.
Furthermore, safety is greatly enhanced with modular formwork. The pre-fabricated modules are designed with safety in mind, ensuring that every component meets stringent quality standards. This reduces the risk of accidents and injuries associated with traditional formwork methods.
In addition to these practical benefits, modular formwork also allows for greater precision in construction. The modules are engineered to exact specifications, ensuring that every pour of concrete is perfect.
This precision leads to higher quality finishes and reduces the need for costly rework.
Customization Process Overview
To fully leverage the potential of modular formwork, we need to understand the customization process that makes it so versatile. This process is at the heart of what sets modular formwork apart from traditional methods, allowing us to tailor solutions to specific project needs.
First, we start with a thorough analysis of the project requirements. This involves collaborating closely with architects, engineers, and contractors to understand the design specifications, structural demands, and any unique challenges the project may present.
By doing so, we can identify areas where customization will yield the greatest benefits in terms of cost savings, efficiency, and quality.
Next, we utilize advanced design software to create detailed models of the formwork system. This digital approach allows us to simulate various scenarios and make adjustments in real-time, guaranteeing that every component is optimized for its intended purpose.
We also consider factors such as material selection and reusability to maximize cost efficiency.
The manufacturing phase is where our vision takes shape. Using precision engineering techniques and high-quality materials, we produce custom formwork components that fit together seamlessly.
Each piece is designed with interoperability in mind, enabling easy assembly and disassembly on site.
Finally, we conduct rigorous testing and quality control checks to guarantee that all customized formwork meets or exceeds industry standards.
This attention to detail guarantees that the final product not only meets but exceeds expectations in terms of performance and durability.
Reducing Material Waste
By leveraging advanced design and manufacturing techniques, we can substantially reduce material waste in modular formwork projects. This is a vital step in our journey towards cost optimization and sustainable construction practices.
When we customize modular formwork, we aren't just building structures; we're crafting solutions that minimize environmental impact and maximize efficiency.
One of the key strategies we employ is precise engineering. Using advanced software and 3D modeling, we can design formwork systems that fit the project's specifications with minimal excess material. This precision guarantees that every piece of formwork is used effectively, reducing the likelihood of unnecessary cuts or mistakes on-site.
Another critical aspect is the use of reusable components. Modular formwork systems are designed to be dismantled and reused multiple times, drastically cutting down on the amount of new material required for each project. This approach not only reduces waste but also lowers overall project costs by extending the lifespan of the formwork, similar to how aluminium formwork accessories can be reused multiple times to ensure durability and cost-effectiveness.
Additionally, we adopt a just-in-time production strategy. By manufacturing components only when they're needed, we avoid stockpiling materials that might go unused or become obsolete. This method guarantees that every piece of material is utilized at the right time and in the right place.
Through these innovative approaches, we're transforming the way construction projects are managed. By reducing material waste, we aren't only saving resources but also contributing to a more sustainable future.
Our commitment to advanced design, precision engineering, and efficient production methods sets a new standard for modular formwork customization—a standard that prioritizes both cost optimization and environmental stewardship.
Streamlining Construction Processes
Streamlining construction processes is at the heart of our modular formwork customization strategy. When we tailor formwork to specific project needs, we aren't just reducing material waste; we're also revolutionizing the way construction sites operate.
By designing and fabricating formwork modules that fit together seamlessly, we eliminate the need for on-site adjustments and manual labor-intensive tasks.
This approach substantially cuts down on setup and dismantle times, allowing crews to move more quickly from one phase of the project to the next. Customized modular formwork guarantees that each component is precision-engineered to fit perfectly, reducing errors and rework. This precision engineering translates into fewer delays and a more predictable construction schedule.
Moreover, our modular formwork systems are designed with ease of use in mind. They're lighter and easier to handle, which reduces the physical strain on workers and enhances safety on the job site. This not only improves worker well-being but also boosts productivity as teams can work more efficiently without fatigue.
In addition, our customization process involves detailed planning and simulation before any physical construction begins. This pre-construction phase allows us to identify potential issues early on and make necessary adjustments, guaranteeing that when the actual building starts, everything runs smoothly.
Accommodating Complex Geometries
Accommodating complex geometries is a cornerstone of our modular formwork customization strategy. In the pursuit of cost optimization, we recognize that traditional formwork methods often fall short when faced with intricate designs and unique architectural features.
This is where modular formwork excels, offering a flexible and adaptable solution that can be tailored to meet the most demanding project requirements.
When dealing with complex geometries, precision and versatility are paramount. Here are some key ways we achieve this:
- Customizable Modules: We design our modular formwork systems to be highly customizable, allowing us to create unique shapes and configurations that match the specific needs of each project. This guarantees that even the most intricate designs can be accurately replicated.
- Advanced Engineering: Leveraging advanced engineering techniques and software, we can model and simulate complex geometries before construction begins. This proactive approach helps identify potential issues early on, streamlining the process and reducing errors.
- Iterative Design: Our iterative design process involves continuous collaboration with architects, engineers, and contractors. This guarantees that every aspect of the formwork is optimized for the specific geometry of the project, leading to more efficient construction and cost savings.
Long-Term Cost Savings
When it comes to long-term cost savings, our modular formwork customization strategy really pays off. By investing in a system that's tailored to our specific needs, we avoid the inefficiencies and waste associated with traditional formwork methods.
First, modular formwork is reusable, which drastically reduces the cost of materials over time. Unlike traditional plywood or steel forms that often need to be replaced after a few uses, modular systems can be reused hundreds of times without losing their integrity. This reusability means we don't have to constantly purchase new materials for each project, leading to considerable cost savings.
Another key benefit is the speed of construction. Customized modular formwork allows us to work more efficiently because it's designed with our specific project requirements in mind. Faster construction times mean lower labor costs and quicker project completion, which in turn allows us to take on more projects and increase our revenue.
Additionally, modular formwork minimizes the need for on-site adjustments and modifications. Since it's pre-assembled and precision-engineered, it fits perfectly into place without requiring extensive alterations. This reduces downtime and eliminates unnecessary labor expenses associated with making adjustments.
Finally, the durability of modular formwork extends its lifespan notably. With proper maintenance, these systems can last for decades, providing a long-term asset that continues to save us money project after project.
In essence, our modular formwork customization strategy is a game-changer when it comes to long-term cost savings. It combines reusability, efficiency, precision engineering, and durability to create a cost-effective solution that liberates us from the financial burdens of traditional construction methods.
Frequently Asked Questions
How Does Modular Formwork Impact Labor Costs?
Modular formwork substantially reduces labor costs for us. By using pre-assembled, reusable components, we minimize the time spent on site preparation and formwork assembly.
This efficiency cuts down on manual labor hours and reduces the need for skilled workers to construct complex formwork systems. Additionally, modular formwork enhances safety by reducing the risks associated with traditional formwork methods, further optimizing our workforce's productivity and overall project timeline.
Can Modular Formwork Be Used for Small-Scale Projects?
Absolutely, we can use modular formwork for small-scale projects. It's about flexibility and efficiency.
By customizing the formwork to fit the specific needs of the project, we can reduce waste and save time. This approach allows us to be more agile and responsive, even on smaller sites.
It's a game-changer for liberating construction from traditional constraints, making it more accessible and cost-effective for all types of projects.
What Are the Environmental Benefits of Customized Modular Formwork?
Customized modular formwork offers significant environmental benefits. We reduce waste by designing forms that fit specific project needs, minimizing excess materials.
Reusable modules cut down on the overall material consumption and the energy required for production. This approach also helps in reducing the carbon footprint associated with transportation and storage of bulky, one-time-use formwork systems.
How Quickly Can Customized Modular Formwork Be Delivered?
We can deliver customized modular formwork swiftly, leveraging advanced manufacturing techniques and a streamlined supply chain.
Our process allows for rapid design customization, efficient production, and prompt shipping. This means you can receive your tailored formwork solutions within a few weeks, depending on the complexity of the design and your location.
We're committed to getting you the tools you need quickly, so you can start building sooner.
Is Modular Formwork Compatible With All Types of Concrete Mixes?
Modular formwork is highly versatile and can be compatible with a wide range of concrete mixes. However, the specific type of concrete mix can affect the formwork's performance.
We guarantee that our modular formwork is designed to handle various mix designs, from high-strength concretes to self-consolidating concretes. By customizing the formwork to the specific concrete mix, we can optimize its use and achieve the desired structural integrity and finish.
This flexibility liberates us to innovate and deliver superior results in any project.
Conclusion
By embracing modular formwork customization, we can revolutionize the construction industry. We reduce material waste, streamline processes, and accommodate complex geometries with precision. This approach not only enhances efficiency but also leads to significant long-term cost savings. As we move forward, it's clear that tailored formwork solutions are the key to a more sustainable and economically viable future in construction. Let's harness this technology to build smarter and more efficiently.