Budget Planning for First-Time Aluminium Formwork Users
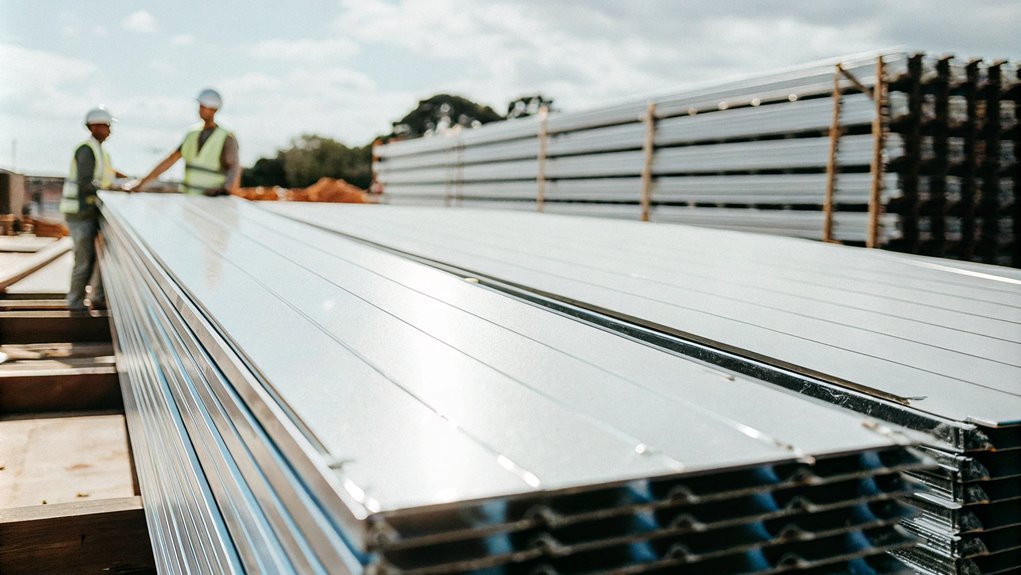
When planning your budget for using aluminium formwork for the first time, consider the higher initial investment, but also the long-term savings. Aluminium formwork can be reused up to 200-300 times, substantially reducing material costs per project. Although the initial cost is high, it spreads out over multiple projects, making it cost-effective in the long run. This method also accelerates construction speed, reducing the timeline by up to 50% and labor costs due to quicker assembly and disassembly. Additionally, aluminium formwork produces high-quality, uniform concrete surfaces, eliminating the need for extra finishing work. As you delve into the details, you'll find how these efficiencies can transform your construction projects.
Project Size Considerations
When planning a construction project, the size of the project is a crucial factor to think about, especially when deciding between aluminium and traditional formwork. For us, understanding the project's scale helps in making informed decisions that can substantially impact our budget and timeline.
Larger projects often benefit greatly from the use of aluminium formwork. This is because aluminium formwork is highly efficient and reusable, which can offset its higher initial cost over time.
For example, if we're working on a large residential complex, aluminium formwork can be reused for multiple floors and even across different buildings, reducing the overall cost per unit area. In such cases, the rapid assembly and disassembly of aluminium formwork can accelerate construction, minimizing the need for skilled labor and reducing the construction cycle to as little as 4-5 days per layer.
On the other hand, smaller projects might find traditional formwork more cost-effective. Traditional formwork, though less efficient regarding reusability and assembly time, has a lower upfront cost.
This makes it more appealing for projects with tight budgets or those that don't require the precision and consistency that aluminium formwork provides. For a small family home or a minor renovation, traditional formwork could be the more economical choice, even if it means a bit more time and labor to set up and dismantle.
In essence, our project size will guide us in choosing the right formwork system. By considering whether our project is large and repetitive or small and straightforward, we can make a decision that aligns with our budgetary constraints and construction goals.
This careful consideration guarantees that we optimize our resources and deliver a quality project efficiently.
Cost Comparison Analysis
As we explore the cost comparison analysis, it's clear that the choice between aluminium and traditional formwork can substantially impact our budget. At first glance, traditional formwork systems seem like the more affordable option due to their lower upfront costs.
However, when we dig deeper, the long-term benefits of aluminium formwork become palpable. The initial investment in aluminium formwork is indeed higher, but this cost can be spread out over multiple projects. Aluminium formwork can be reused up to 200-300 times, markedly reducing the material cost per project.
In contrast, traditional formwork, typically made from timber or plywood, has a much shorter lifespan. Timber formwork might last for around 20-30 uses before needing replacement, while plywood fares slightly better but still falls short of aluminium's durability.
The labor costs also vary markedly. Aluminium formwork systems are pre-engineered for quick assembly and disassembly, reducing labor requirements and speeding up the construction process. This efficiency can save us up to 30% in labor costs compared to traditional formwork.
Additionally, aluminium formwork minimizes maintenance and repair costs due to its durability and resistance to damage. This translates to fewer resources spent on repairs and less equipment downtime, further enhancing our overall efficiency and cost savings.
Time Efficiency Benefits
The significant cost savings from aluminium formwork are closely tied to its time efficiency benefits. When we first considered switching to aluminium formwork, one of the key factors that swayed our decision was the potential to save time. Traditional formwork methods, such as those using wood or steel, require a substantial amount of time for setup, alignment, and dismantling.
In contrast, aluminium formwork systems are designed for quick assembly and disassembly. For instance, aluminium formwork can be reused multiple times without losing its shape or integrity. This means we can achieve faster turnover between construction cycles.
In high-rise constructions, we can complete a four to five-day cycle per floor, which is a significant improvement over traditional methods. The lightweight and flexible nature of aluminium formwork allows for quick and easy setup, resulting in faster construction progress.
For example, with aluminium formwork, we can reduce the construction time of a building by up to 50% compared to conventional methods. This speed is particularly beneficial for large-scale projects where reducing construction time can lead to significant cost savings and quicker project completion.
Additionally, the modular nature of aluminium formwork simplifies construction processes, minimizing delays and streamlining our workflow. By automating some of the planning and quantity estimation of formwork accessories, we can further reduce the time required, saving up to 87.5% of the time engineers spend on these tasks.
In essence, the time efficiency benefits of aluminium formwork are a game-changer for our construction projects. It allows us to deliver projects on time, reduce labor costs, and enhance the overall quality of our constructions.
Quality and Finish Advantages
Our experience with aluminium formwork has consistently shown that it delivers superior quality and finish, a critical aspect that sets it apart from traditional methods. When we first adopted aluminium formwork, we were impressed by the smooth and uniform concrete surfaces it produced.
This precision is due to the precise engineering of the aluminium panels, which guarantees that the concrete cures with minimal defects and no substantial variations in dimensions.
One of the most noticeable benefits is the elimination of the need for additional plastering or finishing work. With aluminium formwork, the concrete surfaces are so smooth that they often require no further treatment, saving us both time and money.
This high-quality finish is particularly important for us, as it enhances the overall aesthetic and structural integrity of our buildings.
The dimensional accuracy of aluminium formwork is another key advantage. It guarantees consistent dimensions throughout the structure, reducing the likelihood of defects and the need for costly corrections.
For example, in high-rise constructions, we can achieve a four to five-day cycle per floor, which is considerably faster than what conventional formwork can offer. This speed and accuracy have been game-changers for our projects, allowing us to meet tight deadlines while maintaining exceptional quality.
Construction Timeline Impact
When it comes to managing construction timelines, aluminium formwork has been a game-changer for our projects. The speed and efficiency it brings have substantially reduced our project completion times, allowing us to deliver high-quality structures faster than ever before.
One of the key advantages of aluminium formwork is its lightweight and modular design, which makes assembly and disassembly a breeze. Here's a comparison of how aluminium formwork impacts our construction timelines versus traditional methods:
Aspect | Aluminium Formwork | Traditional Formwork |
---|---|---|
Assembly Time | 2-4 hours | 1-3 days |
Disassembly Time | 1-2 hours | 1-2 days |
Number of Workers Required | 2-4 workers | 6-8 workers |
Reuse Cycles | Up to 250 cycles | 7-8 cycles |
Floor Cycle Time | 4 days | 7-10 days |
With aluminium formwork, we can assemble the formwork quickly, often within hours, and disassemble it just as fast. This modular system allows for concurrent operations, such as pouring concrete while setting up the next level of formwork, which eliminates downtime and streamlines the construction process.
In urban areas, this efficiency is particularly beneficial. For instance, in high-rise projects, aluminium formwork has enabled us to complete floor cycles in just four days, a marked reduction from the 7-10 days required with traditional methods. This accelerated timeline not only saves time but also reduces labor costs and overall project expenses, making our projects more profitable and efficient. By adopting aluminium formwork, we've liberated ourselves from the constraints of traditional construction methods, allowing us to deliver projects faster and with higher quality.
Local Market and Labor Costs
As we explore the nuances of budget planning for aluminium formwork, it's essential to examine the local market and labor costs, which can substantially impact the overall project expenses. The availability and cost of skilled labor in your area are critical factors to take into account.
For instance, if you're working in a region where skilled labor is scarce or highly priced, the efficiency of aluminium formwork becomes even more valuable. These systems require less labor for setup and removal compared to traditional formwork, which can markedly reduce your labor costs over time.
Local market conditions also influence the demand for sustainable construction practices. In areas where eco-friendly methods are highly valued, the long-term benefits of aluminium formwork, such as reusability and waste reduction, can be a major selling point.
This not only aligns with local preferences but also contributes to a more sustainable construction process, which can lead to cost savings in the long run.
When calculating labor costs, consider that aluminium formwork systems typically need fewer workers to assemble and handle. This reduces the overall labor expenditure and improves productivity.
For example, if a traditional formwork system requires a crew of 10 workers for assembly, an aluminium formwork system might only need 6, resulting in substantial labor cost savings.
Additionally, the ease of assembly and disassembly of aluminium formwork means less time spent on these tasks, allowing your workforce to focus on other critical aspects of the project.
This streamlined process not only saves time but also minimizes the risk of errors and rework, further reducing labor hours and associated costs.
Frequently Asked Questions
Can Aluminium Formwork Be Used for Curved or Complex Structures?
We can definitely use aluminium formwork for curved or complex structures. Aluminium formwork systems are versatile and can be engineered to fit specific curves and geometries.
For instance, flexible formwork made from aluminium can be shaped to exact curves, making it ideal for structures like curved walls, vaulted ceilings, and circular tanks. These systems offer precision, ease of adjustment, and the ability to handle complex architectural designs efficiently.
How Does Aluminium Formwork Impact the Environment and Sustainability?
When we adopt aluminium formwork, we substantially reduce our environmental footprint. By replacing traditional timber, we protect forests and minimize carbon emissions from deforestation and transportation.
Aluminium is fully recyclable, reducing waste and the demand for new raw materials. It can be reused over 200 times, cutting down construction time by 20-30% and lowering energy consumption.
This approach aligns perfectly with our goal of a sustainable future, making our construction processes more eco-friendly and resource-efficient.
What Are the Maintenance Requirements for Aluminium Formwork?
To keep our aluminium formwork in top shape, we need to follow some key maintenance steps.
After each use, we clean the panels to remove any residual concrete, dust, or debris.
Regular inspections help identify any damage, dents, or cracks, which can often be repaired to maintain the formwork's condition.
Proper storage in a dry, covered area prevents moisture and corrosion.
This care guarantees our formwork can be reused over 200 times, making it a worthwhile investment.
Can Aluminium Formwork Be Combined With Other Materials for Specific Designs?
When we use aluminium formwork, we can definitely combine it with other materials to achieve specific designs.
For instance, we can use aluminium alloy formwork for the beam sides and bottom, while connecting them with aluminium male and female corner formwork.
Additionally, we can incorporate independent steel supports for the floor formwork to enhance stability and efficiency.
This flexibility allows us to tailor our formwork to various structural sizes and needs.
Are There Any Specific Safety Considerations When Using Aluminium Formwork?
When using aluminium formwork, we must prioritize several safety considerations. First, guarantee proper installation and regular inspections to maintain structural stability.
We need to provide fall protection and stable work platforms, especially at elevated heights. Electrical safety is essential, as aluminium can conduct electricity, so regular inspections and grounding of equipment are necessary.
Additionally, we should handle and lift panels correctly using cranes or hoists, and shield the formwork from extreme weather conditions. Worker training and compliance with international safety standards are also critical to prevent accidents and guarantee a safe working environment.
Conclusion
When budgeting for aluminium formwork as a first-time user, it's vital to consider several key factors. Here's a concise conclusion:
As we plan our construction project, we must weigh the initial higher cost of aluminium formwork against its long-term benefits. With the ability to reuse these panels up to 250 times, we can substantially cut down on overall expenses. The speed and efficiency of aluminium formwork shorten our construction timeline, reduce labor costs, and guarantee high-quality finishes. By factoring in project size, local market conditions, and labor costs, we can make an informed decision that balances our budget with the need for efficiency and quality. This approach will help us streamline our process, save money, and deliver a superior final product.