Advances in Adjustable Formwork for Evolving Construction Needs
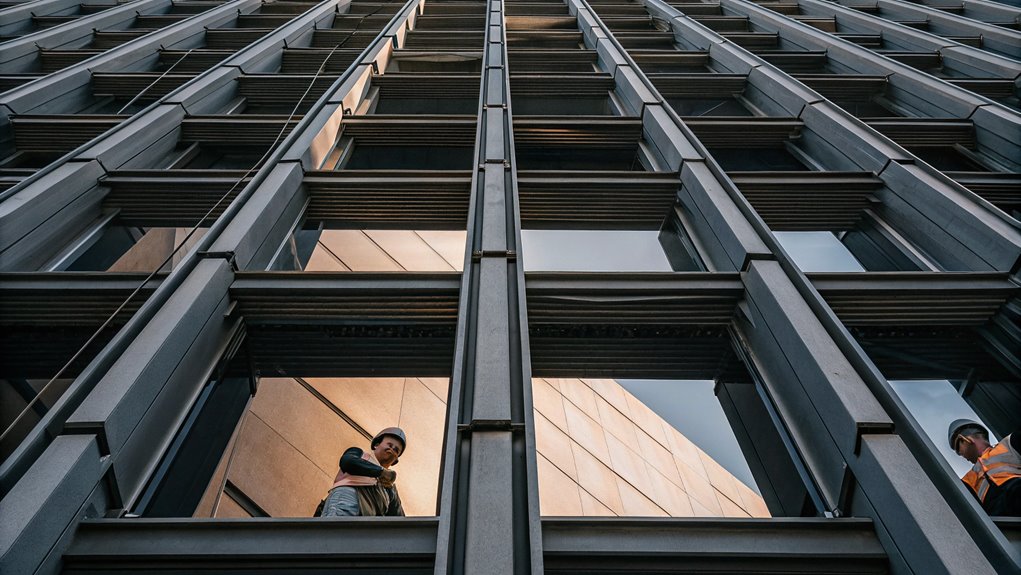
When it comes to advances in adjustable formwork for evolving construction needs, we've seen some remarkable innovations. Self-climbing formwork systems, for instance, use hydraulic mechanisms to climb up buildings independently, reducing construction time and labor costs while enhancing safety. Flexible formwork allows for complex architectural designs with curves and organic forms, minimizing material waste and labor costs. Modular and prefabricated formwork systems offer rapid assembly and disassembly, making them highly reusable and cost-effective. Additionally, digital technologies like BIM and automated robotic systems are streamlining the process, improving precision and safety. As we continue to explore these advancements, you'll discover how they're revolutionizing the construction landscape.
Evolution of Formwork Technology
The evolution of formwork technology has been a remarkable journey, shaping the construction industry in profound ways. When we look back, it's clear that formwork has come a long way from its humble beginnings.
In ancient times, formwork was as simple as using timber to create molds for concrete. Our ancestors, such as the Egyptians and Romans, relied on wooden frames and molds to construct their iconic structures like the pyramids and aqueducts.
The Industrial Revolution marked a significant turning point. With the introduction of steel and advanced types of timber, formwork became more durable and reusable. Steel formwork, in particular, revolutionized the industry by enabling the rapid construction of large-scale projects like skyscrapers.
This shift not only reduced construction times but also lowered labor costs and improved the overall quality of the finished structures.
As we entered the 20th century, materials like aluminum and plastic became popular, offering even more versatility and efficiency. These lighter materials made handling easier, reduced labor costs, and sped up construction processes. For instance, aluminium formwork systems like those provided by Fommec Global Private Limited, can be reused up to 150 times and enable simultaneous casting of walls and slabs.
The development of modular formwork systems further streamlined the process, allowing for quick assembly and disassembly, and the creation of complex architectural designs.
Today, we're in an era driven by digital technologies and automation. Building Information Modeling (BIM) and advanced software enable precise planning and visualization of formwork designs.
Robotic systems are now assisting in the assembly and placement of formwork components, enhancing precision, speed, and safety. Additionally, there's a growing focus on sustainability, with modern formwork systems designed to minimize waste and use eco-friendly materials.
This evolution hasn't only made construction more efficient and sustainable but has also given us the freedom to design and build structures that were once unimaginable. As we continue to innovate, we're excited to see what the future holds for formwork technology.
Self-Climbing Formwork Systems
As we explore the world of advanced formwork technologies, self-climbing formwork systems stand out as a game-changer in modern construction. These systems are particularly useful for building large vertical concrete structures, such as high-rise buildings, silos, and bridge piers, where traditional formwork methods can be cumbersome and time-consuming.
One of the key benefits of self-climbing formwork is its independence from cranes. Unlike traditional methods that require significant crane time to set and move formwork, self-climbing systems use hydraulic or electric jacks to elevate themselves. This not only frees up cranes for other tasks on congested sites but also accelerates overall project schedules and improves site productivity.
The process of self-climbing formwork is highly efficient and safe. The system involves the elevation of the mast and the climbing bracket-formwork-set along the wall surface. This is achieved through hydraulic climbing mechanisms that raise the climbing rails, automatically lock them into place, and then release the forms after concrete pouring.
This automation minimizes labor time, reduces the need for manual handling, and enhances worker safety by keeping them out of harm's way during the lifting process.
Self-climbing formwork also offers versatility and adaptability. It can be customized to fit various building geometries, providing safe working areas even in complex structures.
The systems are designed for repetitive actions, which increases construction speed and productivity. Additionally, they're easy to clean and reuse, generating minimal waste and reducing overall costs in the long run.
In ensuring the structural integrity of these systems, engineers must conduct thorough structural analysis and design, often utilizing engineering software to create detailed designs and comply with building codesbuilding codes.
Flexible Formwork Innovations
Building on the efficiencies of self-climbing formwork, flexible formwork innovations take construction to the next level by offering even more adaptability and precision. This technology is revolutionizing the way we approach complex architectural designs, road construction, and water management projects.
Flexible formwork stands out for its ability to conform to a wide range of shapes and contours, making it an ideal solution for projects that require intricate curves and organic forms.
Here are some key benefits and applications of flexible formwork innovations:
- Complex Architectural Designs: Flexible formwork allows architects to create structures that go beyond conventional geometric boundaries, enabling the realization of complex and visually striking designs that were previously difficult or expensive to achieve.
- Efficient Road Construction: It plays a vital role in road construction, particularly for curved or winding roads, by offering time efficiency, adaptability to curved designs, and material optimization. This results in faster installation, reduced material waste, and lower labor costs.
- Water Management Structures: Flexible formwork is used in the construction of canals, water channels, dams, and reservoirs to create precise geometries and smooth curves, ensuring peak hydraulic performance and structural integrity.
- Reduced Material Waste and Labor Costs: The lightweight and durable nature of flexible formwork minimizes material waste and reduces labor costs by being quicker to install and demobilize compared to traditional rigid formwork.
- Sustainability and Reusability: Flexible formwork is designed with sustainability in mind, allowing for the reuse of formwork materials, reducing the demand for new materials, and minimizing the environmental impact associated with transportation and handling.
These innovations not only enhance the aesthetic appeal and functionality of structures but also contribute to more sustainable and efficient construction practices.
They liberate builders from the constraints of traditional formwork methods.
Modular Prefabricated Formwork
When it comes to streamlining construction processes, modular and prefabricated formwork systems have emerged as a game-changer. These innovative systems are transforming the way we build concrete structures, offering a plethora of benefits that make them an indispensable tool in modern construction.
At the heart of modular formwork are prefabricated panels and components that can be easily assembled and disassembled. This design allows for rapid formwork setup and concrete pouring, substantially reducing construction time.
For instance, with modular formwork, builders can complete multiple construction cycles in a much shorter period than traditional methods, making it ideal for projects with tight deadlines.
One of the standout advantages of modular formwork is its cost-effectiveness. While the initial investment might be higher, the long-term savings are considerable. The reusable nature of these systems means you don't need to purchase new materials for each project, leading to lower material costs over time.
Additionally, the reduction in labor and construction time further contributes to overall cost savings.
Modular formwork also prioritizes worker safety and quality. The components are lightweight and easy to handle, reducing the risk of accidents during assembly and disassembly.
The system's stability guarantees that the formwork can withstand the weight of the concrete, minimizing the risk of structural failure. Furthermore, these systems are designed to provide precision and quality, guaranteeing that the concrete structures meet high standards.
The flexibility and versatility of modular formwork are also remarkable. Standardized panels and components can be configured to suit various construction projects, from residential buildings to complex infrastructure projects.
This adaptability makes modular formwork a versatile solution for different architectural and structural requirements.
Material Selection and Design
In the domain of modular formwork, the choice of materials and the design process are essential elements that dictate the efficiency, safety, and quality of the construction project.
When we select materials for adjustable formwork, we consider several critical factors to guarantee our projects are both cost-effective and environmentally friendly.
Key Considerations in Material Selection and Design
- Durability and Reusability: We opt for materials that offer greater durability and the capability for multiple uses. For instance, steel formwork made from Q235 steel plate can be reused up to 300 times and is 100% recyclable, making it a highly efficient choice. Aluminium formwork, for example, can be reused up to 150 times, enhancing project efficiency.
- Lightweight yet Strong: Materials like recycled plastics and lightweight steel are favored for their ability to support heavy weights while being easier to handle and transport. This reduces the overall weight of the formwork, enhancing its performance and safety.
- Customizability: The ability to modify standard formwork to suit specific project needs is imperative. Materials like alkus all-plastic facings can be adapted and molded around sub-structures to achieve the perfect finish, especially for complex geometries and curved structures.
- Environmental Impact: We prioritize eco-friendly materials and consider the environmental impact of our choices. This includes selecting materials with minimal waste generation and those that can be easily recycled or reused.
- Compliance with Standards: Ensuring that the materials and design comply with local building codes and standards is essential. This involves integrating regulatory requirements into the design phase to avoid any compliance issues during the project.
Installation and Alignment
Precision is key when it comes to the installation and alignment of adjustable formwork. As we explore this critical phase, it's clear that careful planning and execution are essential to guarantee the structural integrity and stability of our construction projects.
First, we need to prepare the construction site thoroughly. This involves clearing any debris or obstacles and guaranteeing a level and stable foundation to support the formwork system.
Once the site is ready, we move on to marking and aligning the beam positions. We use tools like string lines, laser levels, or other alignment instruments to guarantee that the beams are precisely positioned according to our design specifications.
Next, we assemble the formwork panels, which are typically made of materials such as timber, steel, or aluminum. Following the manufacturer's instructions, we make sure these panels are correctly assembled to provide the necessary support and shape for the concrete.
After assembly, we place and secure these panels in their marked positions, guaranteeing they're tightly attached to each other and to the supporting structure using appropriate fasteners or clamps.
Adjusting the formwork elements is a delicate process. We use adjusting spindles that allow for both vertical and horizontal adjustments. For vertical adjustments, we turn the adjusting spindles while guaranteeing the waling-to-bracket holders don't jam.
For horizontal adjustments, we gently push the formwork to the desired side. Once adjusted, we tighten the waling-to-bracket holders and the pressure wedges to secure the formwork in place.
Finally, we install any necessary shuttering and reinforcements, such as steel bars or mesh, to enhance the strength and load-bearing capacity of the beams. By following these steps meticulously, we can guarantee that our adjustable formwork is installed and aligned correctly, setting the stage for a successful and durable concrete structure.
Load and Support Considerations
To guarantee the structural integrity of our construction projects, we must meticulously consider the load and support requirements of our adjustable formwork. This involves a thorough understanding of the various types of loads that the formwork will need to withstand.
When designing and constructing formwork, we've to account for several key load types:
- Dead Load: This includes the weight of the formwork itself and the wet concrete. It's a static load that remains constant over time.
- Live Load: This encompasses the weight of workers, equipment, and materials temporarily placed on the formwork. Safety standards often dictate a minimum live load capacity that the formwork must accommodate.
- Environmental Load: Factors such as wind, vibration, and seismic activity can exert additional forces on the formwork structure, especially in areas prone to these conditions.
Here are some vital considerations for load and support:
- Calculate Concrete Weight: We need to calculate the weight of the concrete based on its volume and density to verify that the formwork can support the significant downward force exerted by the concrete.
- Verify Proper Bracing: The formwork must be properly braced and tied to resist forces such as side thrusts and uplift, especially for battered or sloping forms. This includes using bracing systems and spreaders to maintain the integrity of the formwork.
- Comply with Standards: Our design and calculations must adhere to national and international construction standards, such as CAN/CSA S269.1-16, to verify that the formwork meets minimum load capacities and safety factors.
- Material Selection: The choice of formwork material, whether timber, steel, or aluminum, is essential as it affects the load-bearing capacity of the formwork system.
- Safety Factors: Incorporating safety factors into our load capacity calculations helps account for uncertainties and verifies the formwork system's safety under unexpected conditions.
Safety and Efficiency Benefits
Designing and constructing adjustable formwork with a focus on load and support considerations directly translates into significant safety and efficiency benefits. When we use adjustable formwork systems, we guarantee that our construction projects aren't only safer but also more efficient.
From a safety perspective, adjustable formwork systems, such as self-climbing systems, eliminate the need for external scaffolding and the associated manual labor. This reduces the risk of accidents and injuries, making the workplace safer for everyone involved.
For instance, in high-rise construction, self-climbing formwork systems climb vertically as the building height increases, using hydraulic or mechanical systems. This automated process minimizes the exposure of workers to hazardous conditions, guaranteeing their safety and well-being.
Efficiency is another key benefit of adjustable formwork. These systems are designed to be flexible and versatile, allowing us to adjust components for different heights, thicknesses, and wall angles without the need for custom-made formwork.
This adaptability saves time, money, and resources, as it reduces the need for frequent formwork replacements and the labor involved in adjusting traditional formwork. Effective project management, including ensuring timely delivery, budget adherence, and client satisfaction, further enhances the efficiency of these systemsproject management.
Additionally, system formwork enhances structural integrity and quality by using standardized, modular components engineered to precise specifications. This consistency guarantees fewer imperfections in the finished concrete, meeting strict engineering standards more reliably.
The modular nature of these systems also includes integrated safety components like guardrails and access platforms, further enhancing on-site safety and efficiency.
In essence, adjustable formwork systems streamline construction processes, reduce labor and material costs, and promote a safer working environment. These benefits are vital for modern construction, allowing us to complete projects more efficiently while guaranteeing the highest standards of safety and quality.
Sustainability and Environmental Impact**
When it comes to sustainability and environmental impact, adjustable formwork systems offer several compelling advantages. As we endeavor to make our construction practices more eco-friendly, the choice of formwork plays a vital role.
Adjustable formwork, particularly those made from materials like plastic, aluminum, or recyclable components, substantially reduces the environmental footprint of construction projects.
Here are some key ways in which these systems contribute to sustainability:
- Reduced Waste Generation: Adjustable formwork can be reused hundreds of times, drastically cutting down on the waste generated by traditional wooden or steel formworks that are often discarded after a few uses.
- Conservation of Natural Resources: By using recycled materials and minimizing the need for new raw materials, adjustable formwork helps in conserving forests and other natural resources.
- Lower Carbon Footprint: The lightweight and reusable nature of adjustable formwork reduces transportation emissions and the overall carbon footprint associated with the production and transportation of materials.
- Energy Efficiency: The production of adjustable formwork, especially those made from recycled plastics, is less energy-intensive compared to traditional formwork materials. This contributes to reduced overall energy consumption and lower emissions.
- Recycling and Responsible Sourcing: Adjustable formwork is designed with end-of-life considerations in mind, allowing components to be recycled at the end of their useful life. Additionally, sourcing materials from responsible suppliers guarantees a sustainable supply chain.
Frequently Asked Questions
How Do Advances in Formwork Impact Labor Training and Skill Requirements?
Advances in formwork substantially impact labor training and skill requirements. We need to focus more on technical skills, such as using sensors and digital tools like Concremote to monitor concrete strength and temperature.
Regular training programs are essential to keep workers updated on the latest technologies, such as Building Information Modeling (BIM) and modular formwork systems, which enhance efficiency and safety. This confirms workers are adept at handling modern materials and techniques, making construction projects more efficient and safer.
Can Adjustable Formwork Be Used for Restoration of Historical Buildings?
When it comes to restoring historical buildings, we can indeed use adjustable formwork, but with careful consideration. This method allows for precision and flexibility, which is vital for preserving the original architectural and structural details.
However, we must guarantee that the materials and techniques used match the historic period as closely as possible, and any replacements should be substantiated by documentary and physical evidence to maintain the building's authentic character.
What Are the Cost Implications of Adopting Advanced Formwork Technologies?
When we adopt advanced formwork technologies, the cost implications can be significant. Initially, we face high upfront costs, especially for systems like steel, aluminum, or climbing formwork, which can be costly to purchase and require specialized handling equipment.
However, these technologies often pay off in the long run. For instance, steel and aluminum formwork are highly reusable, reducing long-term material costs and labor expenses.
Climbing and flying formwork systems, although expensive to implement, can accelerate construction schedules and reduce overall project costs through increased efficiency and speed.
Additionally, technologies like precast concrete elements and adjustable formwork can minimize waste and optimize material usage, further reducing costs and enhancing the overall economy of the project.
How Do Drones and Ar/Vr Technologies Enhance Formwork Inspection and Planning?
We're transforming formwork inspection and planning with drones and AR/VR technologies. Drones inspect hard-to-reach areas, capturing high-definition images and videos to identify structural defects and safety hazards, ensuring compliance and safety.
With AR, we overlay 3D models on the construction site, detecting errors before building and visualizing designs in real-time. This enhances collaboration, reduces mistakes, and streamlines progress tracking.
VR allows us to take virtual tours, evaluating design choices and potential issues, making our planning more accurate and efficient.
Are There Specific Regulations or Standards for Using Automated Formwork Systems?
When it comes to using automated formwork systems, we need to adhere to strict safety regulations and standards.
For instance, the selection of formwork systems now must comply with stringent safety criteria, as outlined in various studies and guidelines.
Additionally, automated electrical controls, such as those in formwork, must meet general requirements set by standards like the IEC 60730, which guarantees safety and efficiency in household and similar use equipment.
These standards help us guarantee that our automated systems are both safe and effective.
Conclusion
As we embrace the latest advances in adjustable formwork, we're not just building structures; we're shaping the future of construction. With self-climbing systems, flexible formwork, and modular prefabricated solutions, we're achieving unprecedented efficiency, safety, and sustainability. These innovations allow us to create complex designs with ease, reduce environmental impact, and guarantee our construction sites are safer for everyone involved. It's a new era, and we're excited to see what the future holds for our industry and our families.