A Checklist for Pre-Installation Inspections of Formwork
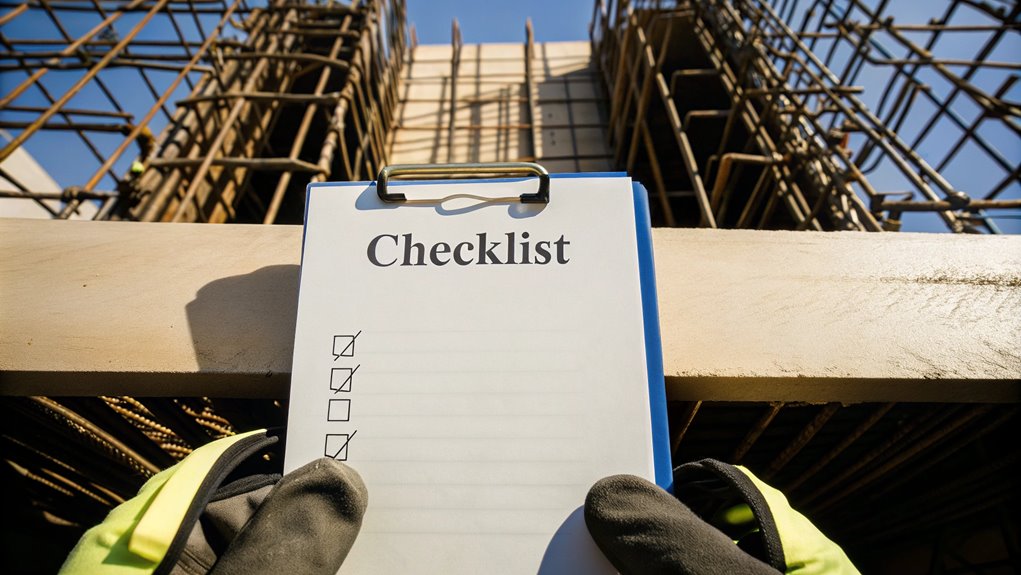
When preparing for formwork installation, we start with a thorough material quality check to guarantee plywood is free from damage and properly treated, and steel frames are free from rust or corrosion. We verify that the assembled formwork aligns perfectly with design specifications and is securely fastened. Safety standards compliance is paramount, so we adhere to local, national, and international regulations and guarantee all personnel are trained and equipped with PPE. We assess the structural integrity of the formwork to guarantee it can resist deformation and settle correctly. Finally, we review regulatory requirements to guarantee compliance with all legal standards. By following this checklist, we set the stage for a safe and structurally sound build – let's plunge into each step in detail to guarantee your project's success.
Material Quality Check
When it comes to pre-installation inspections of formwork, we must start with a thorough material quality check. This step is vital because the integrity of the entire structure depends on the quality of the materials used. We need to guarantee that every component, from the plywood to the steel frames, meets the specified standards.
First, we inspect the plywood for any signs of damage or deterioration. This includes checking for cracks, warping, or rotting. We also verify that the plywood has been properly treated and sealed to withstand the elements and chemical exposure during concrete pouring.
The surface should be smooth and free of debris to guarantee a clean finish on the concrete.
Next, we examine the steel frames for any signs of rust or corrosion. These frames need to be robust and able to support significant weight without bending or breaking. We check for any cracks in welds and guarantee that all connections are secure and properly aligned.
Additionally, we review certifications and documentation from suppliers to confirm that all materials comply with industry standards and local building codes. This includes verifying certifications such as ISO 9001 for quality management and any specific regional compliance requirements.
Assembly and Installation
Once we've confirmed the quality of our materials, we move on to the critical phase of assembly and installation. This stage is where precision and attention to detail are paramount, as any errors can lead to structural issues or delays in the project.
Key Steps in Assembly and Installation
- Verification of Design Specifications
- Guarantee that the assembled formwork aligns perfectly with the design specifications. This includes checking the dimensions, angles, and placement of all components. Any deviation from the plan can compromise the integrity of the structure.
- Secure Fastening and Anchoring
- Properly secure all formwork elements using approved fasteners and anchoring systems. This step is vital to prevent movement or collapse during concrete pouring and curing.
- Alignment and Leveling
- Use leveling tools to guarantee that the formwork is perfectly aligned and level. Misaligned formwork can result in uneven surfaces or structural defects in the finished concrete.
During assembly, it's imperative to follow a systematic approach to avoid mistakes and ensure compliance with building codes. Start with a clean and prepared site to prevent any obstacles or hazards. Use a checklist to track each component as it's assembled. Conduct interim inspections to catch any issues before they become major problems.
Safety Standards Compliance
Ensuring safety standards compliance is a non-negotiable aspect of pre-installation inspections for formwork. When we begin a construction project, the well-being of our workers and the integrity of the structure are paramount.
Compliance with safety standards isn't just a regulatory requirement; it's a moral imperative.
We must start by reviewing and adhering to all relevant local, national, and international safety regulations. This includes OSHA guidelines in the U.S., EU directives in Europe, or any other pertinent standards in your region.
These regulations are designed to protect workers from hazards such as falls, structural collapses, and other potential dangers associated with formwork.
During pre-installation inspections, we need to verify that all formwork components meet these safety standards. This involves checking for any damage or wear on the formwork materials.
Guaranteeing proper anchorage and support systems are in place, and confirming that load calculations have been accurately performed is also crucial.
Additionally, we should guarantee that all personnel involved in the installation process are properly trained and equipped with personal protective equipment (PPE).
Safety training should cover topics such as safe handling of materials, correct use of scaffolding, and emergency procedures.
Ensuring that a Site Supervisor is present to oversee the installation and enforce safety protocols is essential for maintaining a safe working environment.
Structural Integrity Assessment
As we move from safety standards compliance to evaluating the structural integrity of formwork, our focus shifts to the robustness and stability of the entire system. This critical step guarantees that the formwork can withstand the stresses and loads it will be subjected to during the construction process.
When evaluating structural integrity, we must consider several key factors:
- Material Quality: We need to verify that all materials used in the formwork are of high quality and meet the specified standards. This includes checking for any defects or damage in the wood, steel, or other components.
- Design Accuracy: The design of the formwork must be accurate and aligned with the project specifications. Any deviations or miscalculations could compromise the structural integrity.
- Assembly Correctness: Proper assembly is vital. We must guarantee that all components are correctly fitted together and securely fastened according to the manufacturer's instructions and industry best practices.
During this evaluation, we should also inspect the supports, bracing systems, and tie systems to guarantee they're properly installed and can handle the anticipated loads.
The formwork should be able to resist settlement, deflection, and other forms of deformation that could affect its stability.
Regulatory Requirements Review
When it comes to pre-installation inspections of formwork, complying with regulatory requirements is paramount. We must guarantee that every aspect of our formwork meets or exceeds the standards set by local, national, and international regulations.
This involves a thorough review of all relevant codes and guidelines to avoid any potential legal issues or safety hazards.
We start by familiarizing ourselves with the specific regulations governing our project location. This could include OSHA standards in the United States, CSA standards in Canada, or Eurocode standards in Europe.
Each region has its own set of rules that dictate how formwork should be designed, constructed, and inspected.
During the review process, we pay close attention to details such as load capacities, material specifications, and safety protocols. For example, OSHA requires that formwork be capable of supporting all loads during construction without collapsing or failing.
We also need to guarantee that all personnel involved in the installation are properly trained and equipped.
Additionally, we consider environmental regulations and any special conditions that might apply to our site. This includes guaranteeing that our formwork doesn't pose a risk to nearby structures or public spaces.
Frequently Asked Questions
How Often Should Formwork Inspections Be Conducted?
We conduct formwork inspections regularly to guarantee safety and quality. Before installation, we inspect the formwork to check for any damage or defects.
During the construction process, we perform daily checks to verify that the formwork remains stable and secure.
After each use, a thorough inspection is necessary to identify any wear and tear, guaranteeing it's safe for the next application. This frequent monitoring prevents accidents and maintains structural integrity.
Who Is Responsible for Conducting Pre-Installation Inspections?
We're responsible for conducting pre-installation inspections. It's our duty to verify that every component is in perfect condition before it's put to use.
We must scrutinize each piece of formwork, checking for any signs of damage or wear. This proactive approach guarantees safety and quality, liberating us from the risks of faulty installations and verifying our projects stand the test of time.
What Are the Consequences of Failing a Pre-Installation Inspection?
If we fail a pre-installation inspection, we risk serious safety hazards and potential structural failures. This can lead to costly repairs, project delays, and even legal repercussions.
It also undermines the trust of our clients and compromises our professional integrity. Ensuring thorough inspections is vital for maintaining high standards and safeguarding everyone involved in the project.
We must take these inspections seriously to avoid such detrimental consequences.
Can Pre-Installation Inspections Be Performed by Non-Specialists?
We must be clear: pre-installation inspections shouldn't be performed by non-specialists. These inspections require specialized knowledge and skills to guarantee safety and accuracy.
Allowing non-specialists to perform these inspections can lead to overlooked critical issues, potentially resulting in structural failures or accidents. We need experts who can identify and address any problems before they become major hazards.
It's about guaranteeing our safety and the integrity of the project.
Are There Any Specific Tools Required for Formwork Inspections?
For formwork inspections, we need specific tools to guarantee accuracy and safety.
We use tape measures to check dimensions, levels to verify alignment, and spirit levels for guaranteeing the formwork is plumb and level. Safety gear like hard hats and steel-toed boots are also essential.
Additionally, we employ calipers for precise measurements and visual inspection tools such as magnifying glasses or binoculars for detailed checks. These tools empower us to conduct thorough inspections.
Conclusion
We've outlined a thorough checklist for pre-installation inspections of formwork to guarantee your project meets the highest standards. By checking material quality, verifying assembly and installation, complying with safety standards, evaluating structural integrity, and reviewing regulatory requirements, you'll mitigate risks and guarantee a successful construction process. This proactive approach will save time, reduce costs, and enhance overall project quality. Let's build with confidence and precision.