A Beginner’s Guide to Formwork Planning for Large-Scale Projects
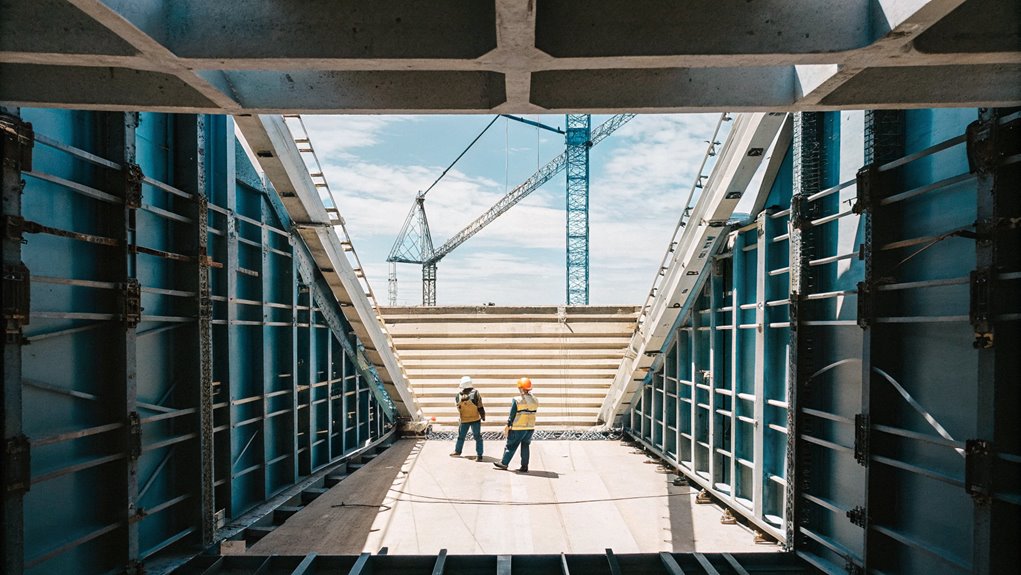
When planning formwork for large-scale projects, we start by understanding the basics: formwork is a temporary structure that shapes and supports concrete until it hardens. We select materials like aluminum or steel for their durability and reusability, ensuring they can handle the weight of the concrete and additional loads. Design alignment with architectural plans and structural requirements is vital, along with ensuring precise geometry for easy placement and removal. Safety protocols include PPE, fall protection, and regular structural inspections. Logistical planning involves phased project management, detailed scheduling, and effective communication. Budgeting and cost management are also key, as are site preparation and layout. By mastering these elements, you'll be well on your way to successful formwork planning; continue to explore these topics for an in-depth understanding.
Understanding Formwork Basics
When undertaking large-scale construction projects, it's crucial to begin with a solid understanding of formwork basics. Formwork is the temporary structure used to shape and support concrete until it hardens and gains enough strength to stand on its own. This foundational element of construction can make or break the success of a project, so let's delve into the fundamentals.
First, we need to understand the different types of formwork. Traditional timber formwork is still widely used due to its cost-effectiveness and ease of use, but modern projects often opt for more advanced materials like aluminum, steel, or plastic.
These materials offer greater durability and can be reused multiple times, making them a more sustainable choice for large-scale projects. For instance, aluminium formwork systems are particularly advantageous due to their lightweight, easy assembly, and high reusability, which can significantly accelerate construction timelines and reduce costs.
Another critical aspect is the design and planning phase. Here, precision is key. We must guarantee that our formwork designs align perfectly with the architectural plans and structural requirements of the building.
This involves meticulous calculations to guarantee that the formwork can withstand the weight and pressure of the concrete as it sets.
Safety is also a paramount consideration in formwork planning. We need to guarantee that all formwork is securely anchored and braced to prevent collapse during concrete placement and curing.
Regular inspections are crucial to identify any potential weaknesses or issues before they become major problems.
Finally, sustainability should be at the forefront of our minds. Choosing reusable formwork materials and implementing efficient dismantling processes can substantially reduce waste and lower environmental impact.
Material Selection and Quality
Having mastered the fundamentals of formwork, we now focus on the critical aspect of material selection and quality. This step is pivotal in guaranteeing that your large-scale project meets the required standards of strength, durability, and safety.
When selecting materials for formwork, several factors need to be considered. Here are some key points to keep in mind:
- Durability and Reusability: Choose materials that can withstand multiple uses without significant degradation. This not only saves costs but also guarantees consistent results.
- Load-Bearing Capacity: Verify that the materials can handle the weight of the concrete and any additional loads during the construction process.
- Surface Finish: Select materials that will produce the desired surface finish for your concrete. For example, plywood or steel forms can provide a smooth finish.
- Eco-Friendliness: Opt for sustainable materials where possible to reduce environmental impact and align with green building practices.
- Cost-Effectiveness: Balance the cost of materials with their quality and performance. Cheap materials may not always be the best value in the long run.
The quality of the materials is equally important. High-quality materials will guarantee that your formwork stands up to the rigors of construction and produces high-quality concrete finishes.
Regularly inspect your materials for any defects or damage before use, and maintain them properly to extend their lifespan.
Design Considerations and Standards
Designing formwork for large-scale projects involves a meticulous approach to guarantee that the structure meets both functional and aesthetic requirements. When we initiate such projects, we must consider several key design elements to guarantee the formwork is robust, efficient, and compliant with industry standards.
First and foremost, we need to adhere to local building codes and international standards such as those set by the American Concrete Institute (ACI) or the International Building Code (IBC). These standards provide guidelines on load calculations, material strengths, and safety protocols that are vital for the structural integrity of the formwork.
Another critical aspect is the geometry of the formwork. We must guarantee that the design allows for easy placement and removal of the forms without compromising the concrete's finish. This involves careful planning of form tie spacings, formwork joints, and access points for workers.
Sustainability is also a key consideration. We aim to use reusable formwork materials whenever possible to reduce waste and lower the environmental impact of the project. Additionally, incorporating modular formwork systems can enhance efficiency by allowing for quicker assembly and disassembly.
Safety is paramount in large-scale projects. Our design must include robust fall protection systems, secure working platforms, and clear evacuation routes. Regular inspections and maintenance schedules are also essential to prevent accidents.
Finally, we consider the long-term durability of the structure. By choosing high-quality materials and guaranteeing precise alignment during construction, we can achieve a finish that not only meets but exceeds client expectations.
Safety Protocols and Regulations
Ensuring the safety of workers and project integrity is a top priority in large-scale formwork planning. As we explore the complexities of formwork, it's vital to adhere to stringent safety protocols and regulations to prevent accidents and guarantee the structural soundness of the project.
Safety protocols aren't just compliance requirements but integral components of a successful project.
Here are some key aspects we must consider:
- Personal Protective Equipment (PPE): Ensuring all workers have access to and use appropriate PPE such as hard hats, safety glasses, gloves, and harnesses.
- Fall Protection: Implementing measures like guardrails, safety nets, and fall arrest systems to protect workers from falls.
- Structural Stability: Regularly inspecting formwork structures to guarantee they're stable and can withstand loads during construction.
- Training and Education: Providing thorough training on formwork assembly, dismantling, and safety procedures for all workers involved.
- Emergency Response Plans: Developing and regularly updating emergency response plans that include evacuation procedures and first aid protocols.
Adhering to these protocols not only safeguards the well-being of our workforce but also enhances overall project efficiency.
Regulatory compliance is another critical aspect; we must be well-versed in local and international standards such as OSHA regulations in the US or EU's Construction Products Regulation.
Logistical Planning and Scheduling
As we focus on the safety and structural integrity of our formwork, we must also prioritize the meticulous planning and scheduling that underpin the success of large-scale projects. Logistical planning is more than just a checklist; it's a strategic blueprint that guarantees every component of the project aligns seamlessly.
First, we need to break down the project into manageable phases. This involves identifying key milestones, such as site preparation, material delivery, formwork installation, and concrete pouring. Each phase should have clear start and end dates, along with detailed tasks and responsibilities assigned to specific team members.
Next, we must develop a thorough scheduling plan. This includes creating a Gantt chart or similar timeline tool to visualize the sequence of events.
We should also conduct critical path analysis to identify potential bottlenecks and plan contingencies accordingly.
Effective communication is vital in logistical planning. Regular meetings with all stakeholders, including contractors, suppliers, and labor teams, help make sure everyone is on the same page.
We must also establish clear channels for reporting issues or changes in the schedule.
Additionally, we need to think about resource allocation carefully. This involves making sure adequate equipment, materials, and labor are available at the right time.
Inventory management systems can help track materials and prevent shortages or overstocking.
Ensuring project management software proficiency, such as MS Project or Primavera, is essential for managing and tracking the project's progress efficiently.
Budgeting and Cost Management
Budgeting and cost management are the financial backbone of any large-scale project. When it comes to formwork planning, these aspects are vital for guaranteeing that the project stays on track and within budget.
First, we need to establish a thorough budget that accounts for all potential costs associated with the formwork. This includes the cost of materials, labor, equipment rental, and any additional expenses such as transportation and storage.
Effective budgeting and cost management also require close collaboration with the financial manager to ensure compliance with financial regulations and standards.
Here are some key considerations for effective budgeting and cost management in formwork planning:
- Detailed Cost Estimation: Break down the project into smaller components to estimate costs accurately. This involves calculating material quantities, labor hours, and equipment needs.
- Risk Assessment: Identify potential risks that could impact costs, such as delays in material delivery or changes in weather conditions.
- Value Engineering: Continuously look for ways to optimize costs without compromising quality. This might involve selecting more cost-effective materials or streamlining processes.
- Regular Audits: Conduct regular financial audits to guarantee that the project is staying within budget. This helps in identifying any discrepancies early on.
- Contingency Planning: Allocate a portion of the budget as a contingency fund to handle unexpected expenses or changes in the project scope.
Site Preparation and Layout
Site Preparation
Site preparation involves several key activities:
- Clearing and Grading: Removing any debris, vegetation, and existing structures to create a flat surface.
- Geotechnical Investigation: Conducting tests to determine the soil's bearing capacity and other geological conditions.
- Drainage: Ensuring proper water drainage to prevent water accumulation which can interfere with formwork installation.
Ensuring the site is prepared according to the installation plans and specifications is crucial, and this often involves close coordination with the site supervisor to ensure safety compliance.
Site Layout
The site layout is critical for organizing the workspace efficiently. Here are some key considerations:
Aspect | Description | Importance |
---|---|---|
Formwork Zones | Divide the site into zones where different types of formwork will be used. | Guarantees organized workflow. |
Material Storage | Designate areas for storing formwork materials and equipment. | Prevents clutter and improves safety. |
Access Roads | Establish clear access routes for heavy machinery and personnel. | Facilitates smooth logistics. |
Work Stations | Set up designated work stations for formwork assembly and maintenance. | Enhances efficiency and productivity. |
| Safety Zones | Identify and mark safety zones to protect workers from hazards. | Guarantees compliance with safety regulations.
Formwork Installation Techniques
With the site prepared and laid out efficiently, we can now focus on the precise execution of formwork installation techniques. This phase is critical as it directly impacts the quality and durability of the final structure.
Here are some key strategies to guarantee a successful formwork installation:
- Pre-Assembly: Whenever possible, pre-assemble formwork components in a controlled environment to minimize on-site assembly time and reduce errors.
- Modular Formwork Systems: Utilize modular formwork systems that offer versatility and simplicity in design. These systems can be easily customized to fit various project requirements.
- Formwork Tolerances: Guarantee that all formwork is installed within strict tolerance limits to maintain the integrity of the structure. Regular checks and adjustments are essential.
- Material Selection: Choose high-quality formwork materials that are durable and resistant to wear and tear. This includes selecting the right type of plywood, steel, or plastic forms based on the project's specific needs.
- Safety Protocols: Implement rigorous safety protocols during formwork installation. This includes securing forms properly, using appropriate lifting equipment, and guaranteeing that all workers are trained and equipped with necessary safety gear.
Quality Control and Inspection
As we shift from the meticulous process of formwork installation, we must guarantee that every aspect of the structure meets the highest standards. Quality control and inspection are vital phases in formwork planning for large-scale projects, ensuring that the final product is safe, durable, and aesthetically pleasing.
We begin by establishing a robust quality control plan that outlines clear criteria for each stage of the process. This plan should include detailed checklists, regular inspection schedules, and protocols for addressing any discrepancies or defects.
It's imperative to involve experienced engineers and inspectors who can identify potential issues before they become major problems. These professionals must ensure compliance with industry standards and regulations to maintain the integrity of the project.
During the inspection phase, we focus on several key areas. First, we verify that the formwork is properly aligned and securely fastened to prevent any shifts or collapses during concrete pouring.
We also check for any signs of damage or wear on the formwork materials, ensuring they're in good condition to produce high-quality finishes.
Furthermore, we conduct thorough inspections after concrete has been poured to ensure it meets the specified strength and quality standards. This includes testing for density, compressive strength, and surface finish.
Any deviations from the specifications are immediately addressed through corrective actions.
In addition to technical inspections, we emphasize the importance of documentation. Detailed records of all inspections and tests are kept to provide a transparent audit trail and facilitate continuous improvement in future projects.
Frequently Asked Questions
How Do I Handle Formwork for Curved or Irregular Shapes?
When handling formwork for curved or irregular shapes, we use specialized techniques and materials. We often employ flexible formwork systems like plywood or fabric forms that can be shaped to fit the desired curve.
Additionally, we utilize 3D modeling and prefabrication to guarantee precision and efficiency. This approach allows us to achieve complex geometries while maintaining structural integrity and aesthetic appeal. It's all about combining innovative materials with precise planning.
What Are the Best Practices for Reusing Formwork Materials?
When reusing formwork materials, we prioritize meticulous inspection and maintenance. We guarantee each component is thoroughly cleaned and inspected for damage or wear.
Any damaged parts are replaced immediately to maintain structural integrity. We also implement a systematic storage and retrieval process to prevent damage during storage and transportation.
This approach maximizes the lifespan of our formwork materials, reducing costs and environmental impact while guaranteeing consistent quality in our projects.
Can I Use 3D Printing for Custom Formwork Components?
We can indeed use 3D printing for custom formwork components, revolutionizing the way we approach formwork planning.
This technology allows us to create complex geometries and bespoke pieces that traditional methods can't match. It enhances precision, reduces material waste, and speeds up production times.
How Do I Integrate Formwork With Other Construction Processes?
To integrate formwork with other construction processes, we must synchronize our planning across all phases. We start by aligning formwork schedules with concrete pouring and finishing timelines.
Next, we guarantee that formwork design complements the structural integrity and aesthetic goals of the project. We also coordinate with crane operations and site logistics to guarantee efficient placement and removal of formwork components.
This holistic approach streamlines the process, reducing delays and enhancing overall project efficiency.
What Are the Environmental Impacts of Formwork Materials?
When we consider the environmental impacts of formwork materials, we must think about the lifecycle of these materials. We're talking about wood, steel, aluminum, and plastics, which can contribute to deforestation, energy consumption, and greenhouse gas emissions.
Reusing and recycling formwork materials can substantially reduce waste and environmental harm. It's vital for us to choose sustainable options and implement efficient disposal practices to minimize our ecological footprint.
Conclusion
In summary, effective formwork planning for large-scale projects requires a comprehensive approach. We must understand the basics, select high-quality materials, adhere to design standards, prioritize safety protocols, manage logistics and schedules meticulously, and control costs. Thorough site preparation and precise installation techniques are essential. Continuous quality control and inspection guarantee the integrity of the structure. By integrating these elements strategically, we can execute successful and efficient formwork operations that meet the highest standards.