How to Safely Disassemble Aluminium Formwork Systems
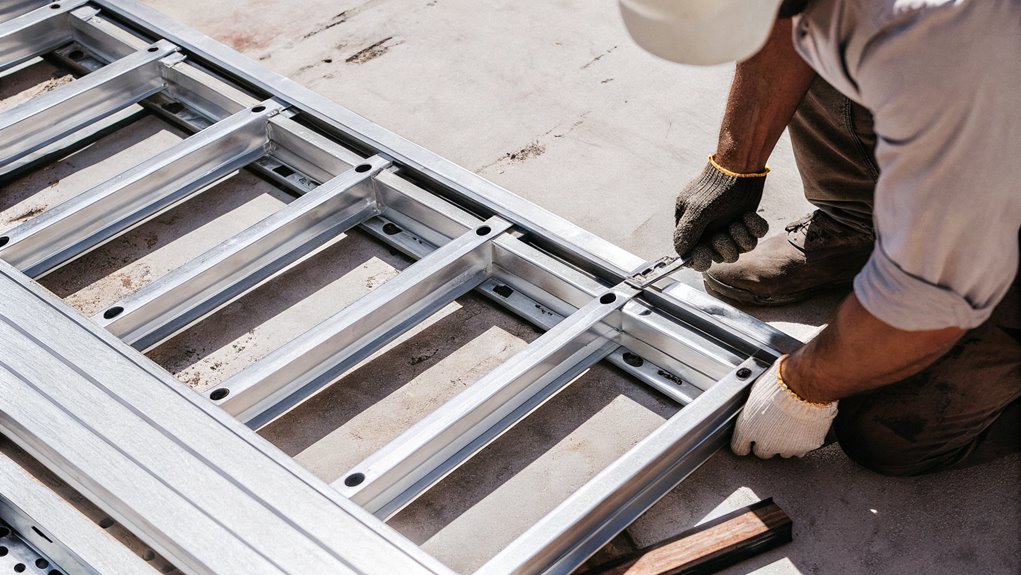
To safely disassemble aluminium formwork systems, we start by clearing the workspace of debris and securing the area to prevent unauthorized access. Each team member must be fully trained and equipped with necessary Personal Protective Equipment (PPE). We conduct a thorough briefing on the disassembly plan, highlighting potential risks and safety protocols. When removing components, we follow the manufacturer's guidelines, use appropriate lifting equipment, and maintain structural integrity by removing fasteners in a systematic order. After disassembly, we handle and store aluminium panels carefully to prevent damage. By following these steps, you can guarantee a safe and efficient process; continuing with these guidelines will provide more detailed insights into each phase.
Preparing the Site and Team
Preparing the site and team is the first essential step in safely disassembling aluminium formwork systems. Before we begin, we need to guarantee that our workspace is clear of any hazards and obstacles. This involves removing any debris, tools, or materials that could interfere with the disassembly process.
We also need to secure the area to prevent unauthorized access, using barriers or warning signs if necessary.
Next, we focus on preparing our team. Each member should be fully trained and experienced in handling aluminium formwork systems, ensuring they are well-versed in quality control procedures. We conduct a thorough briefing to go over the disassembly plan, highlighting potential risks and safety protocols.
It's imperative that everyone understands their role and the steps involved in the process.
Personal Protective Equipment (PPE) is mandatory for all team members. This includes hard hats, safety glasses, gloves, and non-slip boots. We also guarantee that all necessary tools are in good condition and readily available.
We perform a risk assessment to identify any specific hazards associated with the particular formwork system we're working on. This helps us anticipate and mitigate potential dangers such as falling objects or structural instability.
Finally, we establish clear communication channels among team members. This guarantees that everyone is aware of what's happening at every stage of the disassembly process, reducing the risk of accidents and misunderstandings.
Removing Formwork Components
With the site and team fully prepared, we proceed to the critical step of removing formwork components. This phase requires meticulous attention to detail and a systematic approach to guarantee safety and efficiency.
First, we begin by inspecting the formwork system for any damage or deformities that could affect its removal. We check for any signs of wear, corrosion, or damage that might've occurred during the concrete pouring process.
This inspection helps us identify potential bottlenecks and plan accordingly.
Next, we disconnect the formwork panels from the supporting structure. This involves carefully loosening and removing the fasteners such as clamps, screws, or bolts that hold the panels in place. It's vital to follow the manufacturer's guidelines for disassembly to avoid damaging the components.
As we remove each panel, we guarantee it's safely supported to prevent it from falling or shifting unexpectedly. We use appropriate lifting equipment like cranes or hoists if necessary, and always maintain a secure grip on the panels to control their descent.
We also pay close attention to electrical and plumbing lines that may be embedded within the concrete or attached to the formwork. These need to be carefully disentangled and removed without causing any damage.
Finally, once all components are removed, we clean and inspect them for reuse. Proper cleaning and storage are essential to maintain the quality and longevity of the aluminium formwork system, which can be reused up to 150 times.
This ensures the formwork remains in good condition for future projects.
Handling and Storing Aluminium Panels
After successfully removing the aluminium formwork components, we focus on the critical task of handling and storing these panels to guarantee their longevity and future usability. Proper handling is essential to prevent damage, which can render the panels useless for future projects.
When handling aluminium panels, we must be mindful of their edges and surfaces. Sharp edges can cause injuries, so it's important to wear protective gloves and confirm that all personnel are aware of potential hazards.
We should also avoid dragging the panels on the ground, as this can scratch or dent them. Instead, we use lifting straps or clamps to move them securely.
Once the panels are off the site, we need to store them in a way that protects them from environmental factors and physical damage. We recommend storing them in a clean, dry area away from direct sunlight and moisture.
The panels should be stacked vertically rather than horizontally to prevent warping or bending.
To add an extra layer of protection, we can wrap the panels in durable covers or plastic sheets. This helps shield them from dust, dirt, and other contaminants that could compromise their surface quality.
Additionally, labeling each panel with its dimensions and any relevant information confirms easy identification when they're needed again.
Tools and Equipment Needed
Disassembling aluminium formwork systems requires the right tools and equipment to guarantee efficiency and safety. When we approach this task, having the correct gear isn't just a convenience, but a necessity to avoid accidents and guarantee that the process is smooth.
First and foremost, we need to identify the essential tools that will help us dismantle the system without causing damage or injury.
Here are some of the key items:
- Socket Wrench Set: This is vital for loosening bolts and nuts that hold the formwork panels together. A socket wrench set with various sizes guarantees we can handle different types of fasteners.
- Tensioning Tools: These include wrenches or spanners specifically designed for releasing tension in the formwork system. They help in safely lowering or removing panels without sudden drops.
- Lifting Equipment: Depending on the size and weight of the panels, we may need pulleys, hoists, or even cranes to lift them safely off the structure. This equipment must be inspected for safety before use.
- Protective Gear: Hard hats, safety glasses, gloves, and steel-toed boots are indispensable for protecting ourselves from falling objects and sharp edges.
When selecting these tools and equipment, it's important to check their condition regularly to guarantee they're in good working order.
We should also follow manufacturer guidelines for their use to prevent any malfunctions or accidents.
Safety Protocols and Precautions
When disassembling aluminium formwork systems, safety protocols and precautions are paramount to guarantee an accident-free process. We must prioritize our safety and the safety of others involved in the process.
First, verify that all personnel involved in the disassembly are properly trained and equipped with the necessary personal protective equipment (PPE). This includes hard hats, safety glasses, gloves, and sturdy boots.
We should also conduct a thorough risk assessment before starting the disassembly to identify any potential hazards such as loose components, structural weaknesses, or environmental factors like weather conditions.
Proper sequencing is vital. Start by removing the top layers of formwork first and work your way down to avoid any structural instability.
Use appropriate tools for each task to prevent damage to the aluminium components or injury to workers. For example, use a wrench or spanner instead of a hammer to loosen bolts.
Communication is key. Verify that all team members are aware of their roles and responsibilities and maintain continuous communication throughout the process.
Use clear and concise commands and signals to coordinate actions, especially when lifting heavy sections of formwork.
Additionally, verify that the working area is clear of debris and obstacles to prevent tripping hazards. Regularly inspect tools and equipment for any signs of wear or damage and replace them as necessary.
Ensure that the designs and specifications of the aluminium formwork systems comply with project specifications before starting the disassembly to ensure all components are correctly identified and handled.
Finally, follow strict procedures for handling and storing disassembled components to avoid damage or loss. By adhering to these safety protocols and precautions, we can guarantee a safe and efficient disassembly of aluminium formwork systems.
Frequently Asked Questions
How Often Should Aluminium Formwork Systems Be Inspected for Wear and Tear?
We should inspect aluminium formwork systems regularly to guarantee safety and efficiency. Ideally, inspections should be conducted after every use, especially if the system has been subjected to heavy loads or harsh conditions.
Additionally, schedule thorough inspections at least every six months to check for signs of wear and tear, such as cracks, corrosion, or damage to the structure. This proactive approach helps prevent accidents and maintains the system's integrity.
Can Aluminium Formwork Be Reused After a Certain Number of Projects?
Aluminium formwork can be reused multiple times, but its lifespan depends on how well it's maintained and handled.
We guarantee each component is inspected thoroughly after every project for any signs of damage or wear. If it passes inspection, we clean and store it properly to extend its reuse potential.
This way, we maximize the value of our equipment while guaranteeing safety and quality in our projects.
What Are the Environmental Impacts of Disposing of Aluminium Formwork?
When we dispose of aluminium formwork, it has significant environmental impacts. Aluminium is a non-renewable resource, and its extraction and processing require substantial energy and water, leading to greenhouse gas emissions and water pollution.
Improper disposal can result in aluminium ending up in landfills or oceans, contributing to environmental degradation. Recycling aluminium formwork is vital to mitigate these effects and conserve natural resources.
We must prioritize recycling to reduce the demand for primary aluminium production and its associated environmental harms.
How Do You Handle Damaged or Bent Aluminium Formwork Components?
When handling damaged or bent aluminium formwork components, we first assess the extent of the damage to determine if they can be repaired or must be replaced.
If repairable, we use specialized tools to straighten and restore the components.
For irreparable damage, we safely dispose of the components according to environmental guidelines to minimize waste and prevent harm.
We prioritize both safety and sustainability in our handling process.
Are There Specific Regulations for Disposing of Aluminium Formwork in Different Regions?
When disposing of aluminium formwork, we must adhere to regional regulations. In many areas, aluminium is considered recyclable and must be handled accordingly.
We need to check local environmental laws and guidelines for specific disposal protocols. Some regions have designated recycling centers or collection programs for metal waste.
Ensuring compliance helps protect the environment and avoids legal penalties. Always verify the regulations in your area before disposing of any aluminium formwork components.
Conclusion
When disassembling aluminium formwork systems, it's vital to follow the steps outlined carefully. Make certain the site is prepared, and your team is well-trained and equipped. Remove components systematically, handle panels with care, and store them securely. Use the right tools and adhere strictly to safety protocols. By doing so, you'll minimize risks and make certain a safe, efficient disassembly process. This approach not only protects your team but also preserves the integrity of the formwork for future use.